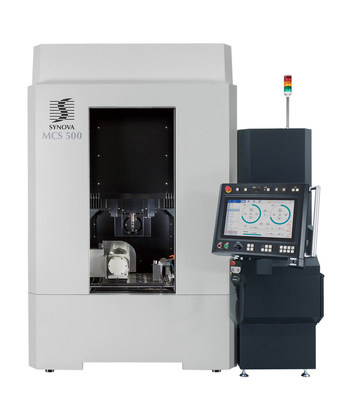
Synova SA, Duillier, Switzerland, a provider of advanced laser-cutting systems, has developed a CNC machine with 5-axis capability to satisfy stringent technical requirements in the aerospace and energy sectors. As engine manufacturers continuously seek to improve performance, high-quality machining of turbine engine components and process stability in production are critical to success. The new MCS 500 with waterjet-guided Laser MicroJet (LMJ) technology allows precise, fast 2D and 3D laser cutting and drilling of hot section components used in modern jet engines and industrial gas turbines with high repeatability.
The MCS 500 is based on a platform manufactured by Makino Milling Machine Co. Ltd., Tokyo. Thanks to Synova's "wet" laser process, the machine drills cylindrical cooling air holes in turbine blades and vanes and cuts complex geometries, such as diffuser shapes, without any heat damage. Superalloy turbine blades with nonconducting thermal barrier coating can be processed in one simple step without cracks or delamination in the ceramic coating and with extremely low recast.
"Synova's MCS 500 Laser MicroJet machine enables our customers to drill holes and to shape diffusers in components already pre-coated with a thermal barrier as opposed to post-coating drilling processes currently being used," said Dr. Bernold Richerzhagen, founder and CEO. "This approach significantly simplifies the overall process, improves quality and reduces overall manufacturing."
The LMJ machine also enables 3D machining of components that are made of new heat-resistant and ultrahard materials, such as ceramic matrix composites (CMCs) without affecting their basic structure. GE Aviation, Evendale, Ohio, is an aero-engine manufacturer that relies on Synova's MCS 500 for machining CMC shrouds for its LEAP engines.
The LMJ system can be flexibly incorporated into production as a standalone system or into automated lines for operator-free, high-volume production. The system is equipped with various interfaces that can be custom configured with automation and handling according to individual needs.
All MCS machines incorporate Synova's waterjet-guided laser technology, which generates a cylindrical laser beam within a hair-thin water jet, resulting in perfectly parallel walls, tight kerf widths, smooth cutting surfaces and sharp edges without a heat-affected zone and free of microcracks, oxidation and depositions.
Synova will premiere the system at EMO Hannover in Germany from Sept. 18 to 23 in hall 12, booth A39.
Information provided by Synova.
Related Glossary Terms
- composites
composites
Materials composed of different elements, with one element normally embedded in another, held together by a compatible binder.
- computer numerical control ( CNC)
computer numerical control ( CNC)
Microprocessor-based controller dedicated to a machine tool that permits the creation or modification of parts. Programmed numerical control activates the machine’s servos and spindle drives and controls the various machining operations. See DNC, direct numerical control; NC, numerical control.
- gang cutting ( milling)
gang cutting ( milling)
Machining with several cutters mounted on a single arbor, generally for simultaneous cutting.
- heat-affected zone
heat-affected zone
That portion of the base metal that was not melted during brazing, cutting or welding, but whose microstructure and mechanical properties were altered by the heat.
- kerf
kerf
Width of cut left after a blade or tool makes a pass.
- milling
milling
Machining operation in which metal or other material is removed by applying power to a rotating cutter. In vertical milling, the cutting tool is mounted vertically on the spindle. In horizontal milling, the cutting tool is mounted horizontally, either directly on the spindle or on an arbor. Horizontal milling is further broken down into conventional milling, where the cutter rotates opposite the direction of feed, or “up” into the workpiece; and climb milling, where the cutter rotates in the direction of feed, or “down” into the workpiece. Milling operations include plane or surface milling, endmilling, facemilling, angle milling, form milling and profiling.
- milling machine ( mill)
milling machine ( mill)
Runs endmills and arbor-mounted milling cutters. Features include a head with a spindle that drives the cutters; a column, knee and table that provide motion in the three Cartesian axes; and a base that supports the components and houses the cutting-fluid pump and reservoir. The work is mounted on the table and fed into the rotating cutter or endmill to accomplish the milling steps; vertical milling machines also feed endmills into the work by means of a spindle-mounted quill. Models range from small manual machines to big bed-type and duplex mills. All take one of three basic forms: vertical, horizontal or convertible horizontal/vertical. Vertical machines may be knee-type (the table is mounted on a knee that can be elevated) or bed-type (the table is securely supported and only moves horizontally). In general, horizontal machines are bigger and more powerful, while vertical machines are lighter but more versatile and easier to set up and operate.
- parallel
parallel
Strip or block of precision-ground stock used to elevate a workpiece, while keeping it parallel to the worktable, to prevent cutter/table contact.