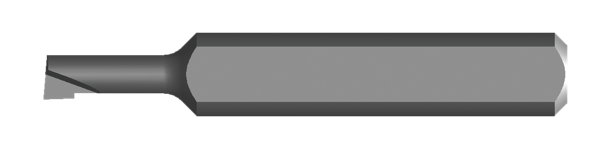
In connection with my canvassing efforts to best focus the boring tools topic scheduled for the January issue of Cutting Tool Engineering, I spoke with Harvey Patterson, product development engineer at Scientific Cutting Tools Inc., Simi Valley, Calif. When it comes to boring tools, he said SCT primarily makes ones for boring holes ½” in diameter and smaller and that he addressed most of the main issues about boring tools in the article CTE published last year titled “Troubleshooting solid-carbide boring bars requires the right diagnosis,” such as chip packing and tapered holes.
According to Patterson, there hasn’t been much innovation in the manufacturing and application of these tools during the past 10 to 20 years, but toolmakers such as SCT are producing smaller solid-carbide boring bars. The smallest from SCT is 0.015” in diameter. The tool can bore only a maximum depth of 0.050” because a lot of overhang for a single-point boring tool that size isn’t possible.
External coolant would be applied for microboring applications, possibly via a toolholder with SCT’s Coolant Ring technology, which enables coolant to be applied around the circumference of a boring bar. For tools 5/8” in diameter and smaller, there’s not enough room in the tool to create a hollow section for adding a vibration-damping material, such as shot. Instead, an end user must reduce the cutting speed and increase the feed rate to eliminate chatter if it’s present. “There are no hard and fast rules,” he said.
Related Glossary Terms
- boring
boring
Enlarging a hole that already has been drilled or cored. Generally, it is an operation of truing the previously drilled hole with a single-point, lathe-type tool. Boring is essentially internal turning, in that usually a single-point cutting tool forms the internal shape. Some tools are available with two cutting edges to balance cutting forces.
- boring bar
boring bar
Essentially a cantilever beam that holds one or more cutting tools in position during a boring operation. Can be held stationary and moved axially while the workpiece revolves around it, or revolved and moved axially while the workpiece is held stationary, or a combination of these actions. Installed on milling, drilling and boring machines, as well as lathes and machining centers.
- chatter
chatter
Condition of vibration involving the machine, workpiece and cutting tool. Once this condition arises, it is often self-sustaining until the problem is corrected. Chatter can be identified when lines or grooves appear at regular intervals in the workpiece. These lines or grooves are caused by the teeth of the cutter as they vibrate in and out of the workpiece and their spacing depends on the frequency of vibration.
- coolant
coolant
Fluid that reduces temperature buildup at the tool/workpiece interface during machining. Normally takes the form of a liquid such as soluble or chemical mixtures (semisynthetic, synthetic) but can be pressurized air or other gas. Because of water’s ability to absorb great quantities of heat, it is widely used as a coolant and vehicle for various cutting compounds, with the water-to-compound ratio varying with the machining task. See cutting fluid; semisynthetic cutting fluid; soluble-oil cutting fluid; synthetic cutting fluid.
- cutting speed
cutting speed
Tangential velocity on the surface of the tool or workpiece at the cutting interface. The formula for cutting speed (sfm) is tool diameter 5 0.26 5 spindle speed (rpm). The formula for feed per tooth (fpt) is table feed (ipm)/number of flutes/spindle speed (rpm). The formula for spindle speed (rpm) is cutting speed (sfm) 5 3.82/tool diameter. The formula for table feed (ipm) is feed per tooth (ftp) 5 number of tool flutes 5 spindle speed (rpm).
- feed
feed
Rate of change of position of the tool as a whole, relative to the workpiece while cutting.
- toolholder
toolholder
Secures a cutting tool during a machining operation. Basic types include block, cartridge, chuck, collet, fixed, modular, quick-change and rotating.