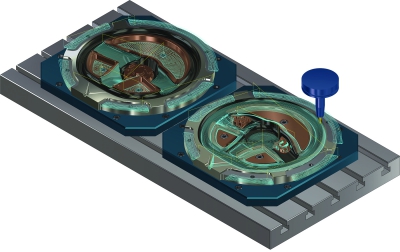
Mastercam 2018 Mill offers expanded machining flexibility and an increased emphasis on speed and automation. 2D high-speed toolpaths, 3D enhancements and multiaxis features combine with dozens of additional new enhancements in a package intended to improve shop floor productivity.
Here are some of the most significant highlights and new functionality in Mastercam Mill:
Stock awareness has been added to select 2D toolpaths and allows tool motion on the top, bottom, or both values of the stock. This provides a safer and more optimized tool motion. You can also optimize finish passes based on your rough stock, giving you more efficient and safer tool motion. Plunge entry is supported for Dynamic Mill toolpaths, allowing you to plunge directly into material. Spring passes can be used to create additional finish passes with a spacing of zero between the passes. This can be used for parts with thin material that may have flexed away from the tool during previous passes.
The workflow for all 3D high speed toolpaths has been streamlined and gives you fine control over exactly where to cut. High speed Hybrid toolpaths now offer smoothing controls and deliver a finer finish, requiring less handwork. Follow containment has been added and allows the tool to follow the containment boundary back to the start of the cut, creating clean and closed passes. It also helps to avoid partial cuts when a containment boundary was directly on top of a vertical surface.
Common direction has been added to select toolpaths and keeps the tool at a uniform tilt angle to reduce tool and machine motion. Dropping has been added to the 3- to 5-axis toolpaths and projects the 3-axis toolpath onto the selected surfaces, adjusting the tool vectors to be normal to the surface. Also, the Multiaxis Link Safety Zone page has been redesigned to better reflect the parameters. You can learn more about the dozens of additional enhancements to Mastercam Mill at whatsnew.mastercam.com.
Additional powerful tools in Mastercam 2018 Mill include:
- Many contour enhancements such as Chamfer tool offset, Machine finish passes, Multi pass order and Rough pass cut direction.
- Mastercam 2D toolpaths now support Depth cut direction and Depth cut order, allowing you to order your cuts from top to bottom or from bottom to top, as well as allowing you to set the depth cut order.
- When you select an undercut tool, but do not want to machine the undercut area, Detect undercuts disables undercutting when using an undercut tool.
- The Collision Control page has been redesigned in Mastercam Multiaxis, and Maintain Tilt keeps the tool tilted during retract and feed moves to reduce tool and machine motion.
Contact Details
Related Glossary Terms
- feed
feed
Rate of change of position of the tool as a whole, relative to the workpiece while cutting.
- milling machine ( mill)
milling machine ( mill)
Runs endmills and arbor-mounted milling cutters. Features include a head with a spindle that drives the cutters; a column, knee and table that provide motion in the three Cartesian axes; and a base that supports the components and houses the cutting-fluid pump and reservoir. The work is mounted on the table and fed into the rotating cutter or endmill to accomplish the milling steps; vertical milling machines also feed endmills into the work by means of a spindle-mounted quill. Models range from small manual machines to big bed-type and duplex mills. All take one of three basic forms: vertical, horizontal or convertible horizontal/vertical. Vertical machines may be knee-type (the table is mounted on a knee that can be elevated) or bed-type (the table is securely supported and only moves horizontally). In general, horizontal machines are bigger and more powerful, while vertical machines are lighter but more versatile and easier to set up and operate.
- toolpath( cutter path)
toolpath( cutter path)
2-D or 3-D path generated by program code or a CAM system and followed by tool when machining a part.
- undercut
undercut
In numerical-control applications, a cut shorter than the programmed cut resulting after a command change in direction. Also a condition in generated gear teeth when any part of the fillet curve lies inside of a line drawn tangent to the working profile at its point of juncture with the fillet. Undercut may be deliberately introduced to facilitate finishing operations, as in preshaving.