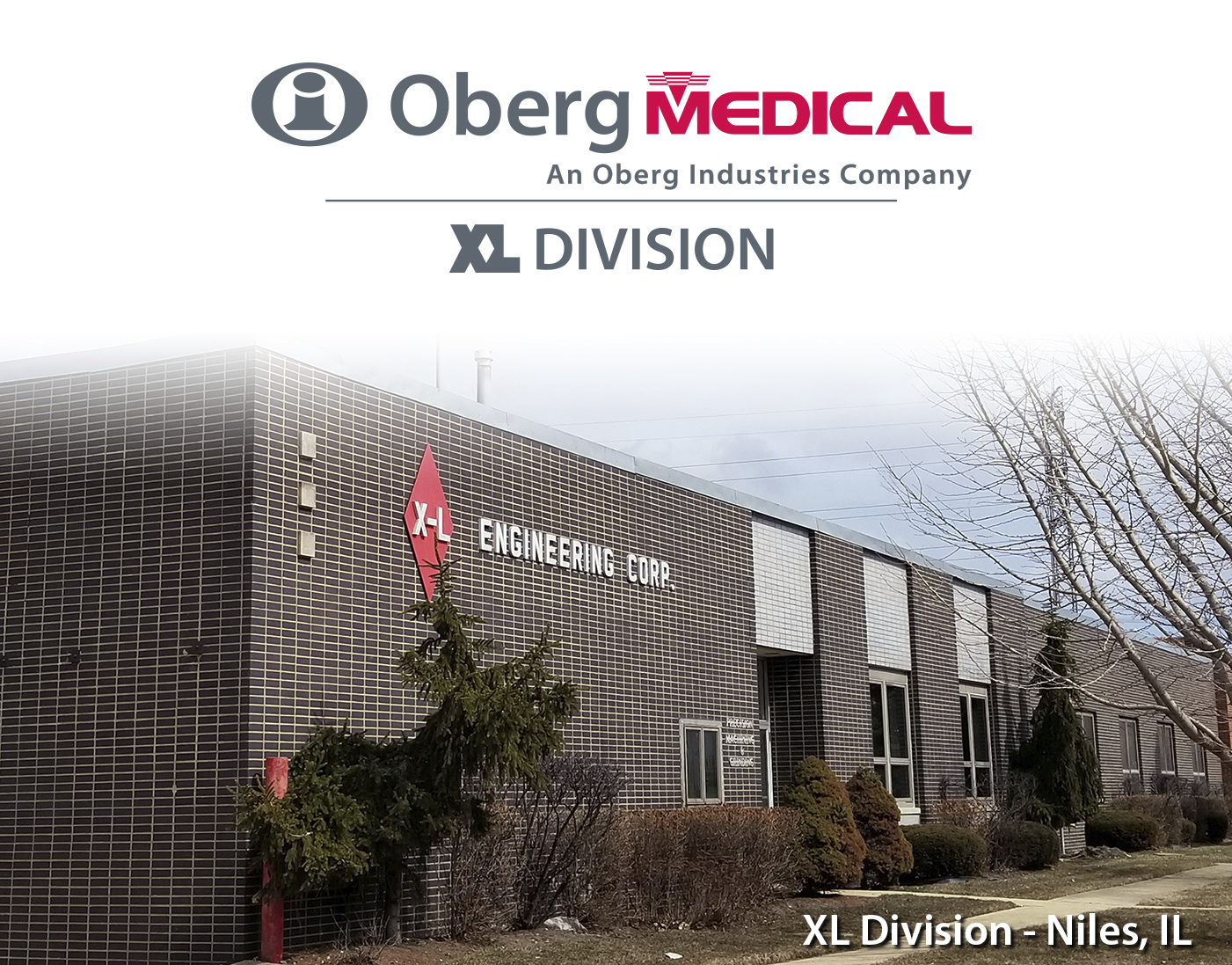
Oberg Industries Inc., Freeport, Pa., a full-service contract manufacturer of precision machined and stamped components located north of Pittsburgh, acquired X-L Engineering Corp., Niles, Ill. The family-owned precision manufacturing business is headquartered in Niles, Ill., fourteen miles northwest of Chicago, with an additional facility in nearby Elk Grove Village.
Originally incorporated in 1943 as a grinding services company, it was purchased in 1972 by Bud Prikos. The business is currently led by brothers Paul and Jack Prikos, Bud Prikos’ two sons. X-L Engineering has over ninety skilled machinists primarily focused on the medical device and aerospace markets. The company is ISO 13485 and AS9100 Rev. D certified. The organization will become an extension of Oberg Medical as its XL Division and will be re-branded externally as “Oberg Medical–XL Division.”
Paul and Jack Prikos will remain active in the business after the sale and will respectively manage the two XL Division facilities with both brothers reporting to Jay Policastro, President of Oberg’s Precision Machining Center and Oberg Medical division.
Oberg’s attraction to X-L is a result of the quality and complexity of the products they manufacture. X-L’s capabilities include grinding, turning, milling, wire EDM, Swiss machining and gun drilling. The company also shares an identical emphasis on the development and training of employees and a passionate focus on tighter tolerances and assembly for their products. X-L’s strengths in thin-walled turning, Swiss machining and, in particular, gun drilling will provide new and expanded capabilities for Oberg to offer to its customer base as well as additional resources in engineering, new product development and prototyping.
David Bonvenuto, Oberg’s CEO, commented, “The culture and passion that X-L’s management and employees embrace for precision and advanced manufacturing is a perfect fit for Oberg Industries. We believe both Oberg’s and X-L’s customer partners will benefit from our consolidated ability to provide enhanced manufacturing capacity in core areas of our business while now having new manufacturing capabilities in house that were previously limited in capacity or outsourced.”
Oberg intends to continue current operations at the XL Division while working together to integrate it into its overall business and standardize to Oberg’s Process Excellence policies. The addition of the XL Division will expand Oberg’s headcount to more than 900 skilled employees worldwide with combined sales expected to exceed $150 million by the end of 2018.
Related Glossary Terms
- electrical-discharge machining ( EDM)
electrical-discharge machining ( EDM)
Process that vaporizes conductive materials by controlled application of pulsed electrical current that flows between a workpiece and electrode (tool) in a dielectric fluid. Permits machining shapes to tight accuracies without the internal stresses conventional machining often generates. Useful in diemaking.
- gang cutting ( milling)
gang cutting ( milling)
Machining with several cutters mounted on a single arbor, generally for simultaneous cutting.
- grinding
grinding
Machining operation in which material is removed from the workpiece by a powered abrasive wheel, stone, belt, paste, sheet, compound, slurry, etc. Takes various forms: surface grinding (creates flat and/or squared surfaces); cylindrical grinding (for external cylindrical and tapered shapes, fillets, undercuts, etc.); centerless grinding; chamfering; thread and form grinding; tool and cutter grinding; offhand grinding; lapping and polishing (grinding with extremely fine grits to create ultrasmooth surfaces); honing; and disc grinding.
- machining center
machining center
CNC machine tool capable of drilling, reaming, tapping, milling and boring. Normally comes with an automatic toolchanger. See automatic toolchanger.
- milling
milling
Machining operation in which metal or other material is removed by applying power to a rotating cutter. In vertical milling, the cutting tool is mounted vertically on the spindle. In horizontal milling, the cutting tool is mounted horizontally, either directly on the spindle or on an arbor. Horizontal milling is further broken down into conventional milling, where the cutter rotates opposite the direction of feed, or “up” into the workpiece; and climb milling, where the cutter rotates in the direction of feed, or “down” into the workpiece. Milling operations include plane or surface milling, endmilling, facemilling, angle milling, form milling and profiling.
- precision machining ( precision measurement)
precision machining ( precision measurement)
Machining and measuring to exacting standards. Four basic considerations are: dimensions, or geometrical characteristics such as lengths, angles and diameters of which the sizes are numerically specified; limits, or the maximum and minimum sizes permissible for a specified dimension; tolerances, or the total permissible variations in size; and allowances, or the prescribed differences in dimensions between mating parts.
- turning
turning
Workpiece is held in a chuck, mounted on a face plate or secured between centers and rotated while a cutting tool, normally a single-point tool, is fed into it along its periphery or across its end or face. Takes the form of straight turning (cutting along the periphery of the workpiece); taper turning (creating a taper); step turning (turning different-size diameters on the same work); chamfering (beveling an edge or shoulder); facing (cutting on an end); turning threads (usually external but can be internal); roughing (high-volume metal removal); and finishing (final light cuts). Performed on lathes, turning centers, chucking machines, automatic screw machines and similar machines.
- wire EDM
wire EDM
Process similar to ram electrical-discharge machining except a small-diameter copper or brass wire is used as a traveling electrode. Usually used in conjunction with a CNC and only works when a part is to be cut completely through. A common analogy is wire electrical-discharge machining is like an ultraprecise, electrical, contour-sawing operation.