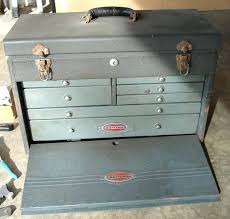
It’s a rite of passage for any new machinist. You order dial calipers, a few micrometers and a dial indicator or two, and before long you’re wondering where you’re going to stick all this stuff. It’s time to get your first toolbox.
Growing up, there was a beat-up old Craftsman in the corner of our garage. It was heavy, the upper right drawer was jammed shut, and all it contained was a hacksaw and a monkey wrench. But that’s what my father owned, so of course I wanted one for myself.
I’m not sure why Dad even had a toolbox. He was an artist and struggled with mechanical concepts. Replacing a lightbulb was in his wheelhouse, but changing out a faucet or repairing a broken door? Not a chance. Dad would rather paint a picture of some mallards paddling about a lake or sketch a portrait of the neighbor’s wife.
I went to Sears one night after work, my young wife at my side. After several hours of drawer pulling, measuring and comparing the dozens of different toolbox models (my wife waited in the food court), I settled on a 7-drawer, 26-" top chest. I knew that its matte gray finish would perfectly complement the Hardinge DSM-59 handscrew to which I’d recently been assigned. It was beautiful.
By the following evening, however, the Craftsman had been relegated to my shed. The smartass grins, the wisecracks overheard at the lunch table, the sidelong looks from my co-workers—I had learned that straying from the herd as I’d done was unacceptable behavior.
Everyone in the shop owned a Kennedy toolbox.
Actually, that’s not true. Jimmy, the old-timer back in the toolroom, had a walnut Journeyman chest from Gerstner, but there was no way I could afford one of those. Swallowing my chagrin, I quickly ordered an 11-drawer Kennedy top chest to replace my embarrassing Craftsman. And just so I could show up that smarmy Dave in the milling department, I even ordered a roller cabinet and a 2-drawer chest base for good measure. I knew that my wife wouldn’t be happy about the expense, but the boss offered to take $20 a week out of my check until it was paid off.
Over the years, I added a couple of more roller chests. A side cabinet. One of the wooden risers that the shop foreman made in his garage on weekends, which fit neatly between my roller cabinet and chest base. It cost me $30. And a whole slew of hand tools, gage pins, depth mics, angle plates, height stands, drop indicators, drill sets and all the other stuff that machinists shouldn’t have to buy but like to have.
My machinist’s tools have since been sold on eBay, my tool chests handed down to my son. He doesn’t appreciate the history, but at least I can run my hands over them when I visit the grandkids. When I lift the lid, I’m greeted with the comfortable smell of sulfur-based cutting oil. I miss the shop.
In hindsight, the guys were a little unfair and shortsighted. It doesn’t matter what kind of toolbox you own or what’s inside it. What’s important is that you enjoy what you do and that you do the very best job you can. And Jimmy was right: I wish I’d ordered one of those Gerstners as he suggested. They’re gorgeous. But you can’t argue with a Kennedy.
Related Glossary Terms
- gang cutting ( milling)
gang cutting ( milling)
Machining with several cutters mounted on a single arbor, generally for simultaneous cutting.
- milling
milling
Machining operation in which metal or other material is removed by applying power to a rotating cutter. In vertical milling, the cutting tool is mounted vertically on the spindle. In horizontal milling, the cutting tool is mounted horizontally, either directly on the spindle or on an arbor. Horizontal milling is further broken down into conventional milling, where the cutter rotates opposite the direction of feed, or “up” into the workpiece; and climb milling, where the cutter rotates in the direction of feed, or “down” into the workpiece. Milling operations include plane or surface milling, endmilling, facemilling, angle milling, form milling and profiling.