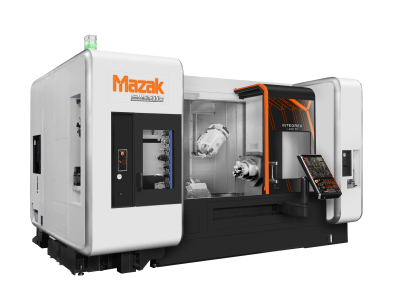
Mazak Corp.'s Integrex i-400ST multitask machine is available with two turning spindles, a milling spindle and lower turret – a configuration that can process first and second operations simultaneously or perform required sequential operations on a single workpiece. With Done In One part production ability to handle all processes from raw material
input through final machining, the Integrex i-400ST reduces lead times dramatically and eliminates multiple setups for improved part accuracy. Its full 5-axis capability can produce fully prismatic parts from solid block or castings, round parts or highly contoured sculptured parts.
Accommodating a 12" chuck, the machine’s main turning spindle provides C-axis indexing in 0.0001-degree increments. While the main turning spindle is a 40-hp integral spindle motor with a 3,300-rpm maximum spindle speed, the second, opposed headstock with 10" chuck features a 35-hp integral spindle motor and 4,000 rpm top
speed.
The Integrex i-400ST’s 30-hp, 12,000-rpm milling spindle with integral motor rotates through the B-axis from +210 to -30 degrees off vertical. On the Y-axis, the milling spindle also travels a generous 9.84", and to increase application versatility, the machine accommodates workpieces up to 25.9" in diameter and 59.8" long. Its standard 36-tool magazine meets the machining requirements of a wide variety of workpieces and can expand up to 110 tools for even greater flexibility.
The machine’s lower drum turret carries nine tools and can work at either the main or second spindle with the same tool. This enables the turret to perform balanced cutting operations on one part, working in tandem with the machine’s vertical milling spindle.
Featuring Mazak’s Mazatrol SmoothX CNC, the Integrex i-400ST makes it easy to generate programs for processing complex parts through off-centerline machining, as well as angled drilling, milling and tapping – all with effortless
programming in EIA/ISO or Mazatrol conversational language for faster part cycle times. The control incorporates a
wide variety of advanced programming functions for complete ease of use and high-speed, high-accuracy machining performance.
Contact Details
Related Glossary Terms
- chuck
chuck
Workholding device that affixes to a mill, lathe or drill-press spindle. It holds a tool or workpiece by one end, allowing it to be rotated. May also be fitted to the machine table to hold a workpiece. Two or more adjustable jaws actually hold the tool or part. May be actuated manually, pneumatically, hydraulically or electrically. See collet.
- computer numerical control ( CNC)
computer numerical control ( CNC)
Microprocessor-based controller dedicated to a machine tool that permits the creation or modification of parts. Programmed numerical control activates the machine’s servos and spindle drives and controls the various machining operations. See DNC, direct numerical control; NC, numerical control.
- gang cutting ( milling)
gang cutting ( milling)
Machining with several cutters mounted on a single arbor, generally for simultaneous cutting.
- milling
milling
Machining operation in which metal or other material is removed by applying power to a rotating cutter. In vertical milling, the cutting tool is mounted vertically on the spindle. In horizontal milling, the cutting tool is mounted horizontally, either directly on the spindle or on an arbor. Horizontal milling is further broken down into conventional milling, where the cutter rotates opposite the direction of feed, or “up” into the workpiece; and climb milling, where the cutter rotates in the direction of feed, or “down” into the workpiece. Milling operations include plane or surface milling, endmilling, facemilling, angle milling, form milling and profiling.
- tapping
tapping
Machining operation in which a tap, with teeth on its periphery, cuts internal threads in a predrilled hole having a smaller diameter than the tap diameter. Threads are formed by a combined rotary and axial-relative motion between tap and workpiece. See tap.
- turning
turning
Workpiece is held in a chuck, mounted on a face plate or secured between centers and rotated while a cutting tool, normally a single-point tool, is fed into it along its periphery or across its end or face. Takes the form of straight turning (cutting along the periphery of the workpiece); taper turning (creating a taper); step turning (turning different-size diameters on the same work); chamfering (beveling an edge or shoulder); facing (cutting on an end); turning threads (usually external but can be internal); roughing (high-volume metal removal); and finishing (final light cuts). Performed on lathes, turning centers, chucking machines, automatic screw machines and similar machines.