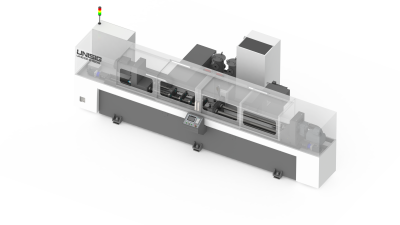
Ideal for manufacturers focused on high- volume/low-mix or low-volume/high-mix production environments, UNISIG’s next generation of UNE Series gundrilling machines delivers operational flexibility, improved performance and effortless operation. Now available, the UNE Series is engineered and designed to simplify gundrilling for all those individuals involved in a facility’s manufacturing process. The UNE Series offers gundrilling solutions that are well suited for various industries, including firearms, automotive, medical, energy, defense and aerospace.
With five models built from two frame sizes, the UNE Series can drill hole diameters from 1.4 mm to 40 mm and depths up to 3,000 mm. The compact frame construction saves valuable floor space as well. Each machine can fit in close proximity to a shop’s existing machining center, lathe or Swiss-style machine for efficient part-processing strategies. Built with quick and easy set-up in mind, the machines are also small enough to be relocated when necessary. For added flexibility to grow with future production needs, all UNE models are robot-ready, allowing shops to add a robot whenever it fits into their budget and production schedule.
“Our feature-rich UNE machines give customers a compact gundrilling solution equipped with the ability to grow alongside them,” said Anthony Fettig, CEO of UNISIG. “A lot of job shops and OEMs have the desire to automate but lack a timeline to do so. Our UNE Series gives them gundrilling benefits for today. It also provides them with security for tomorrow knowing that they can further improve production by adding automation.”
Several innovative features contribute to the performance and productivity of the UNE Series. The single main spindle servo motor delivers the necessary horsepower for two- spindle machines. When power is applied in single-spindle mode, however, shops can produce larger diameter holes to increase their capabilities and add new business without adding a new machine.
Unlike pressure-based coolant systems, the UNE Series features a programmable flow- based coolant delivery system designed to provide the right amount of coolant to the tool’s cutting edge. The end result for the operator means they can confidently predict tool breakage and spend less downtime recovering an interrupted process.
Powered by Siemens, UNE Series machines feature intuitive controls that give operators a full process picture at a glance on a rich color interface with touchscreen capabilities. The control’s heavy-duty buttons also function when operators are wearing gloves.
Ergonomically designed and engineered with the building owner and operator in mind, UNE machines offer an automated door option, which can benefit companies with or without automation. “Adding an automated door eliminates the repetitive task of opening and closing machine doors,” said Anthony. “Not only does this reduce fatigue, but it improves throughput and gives the operator an opportunity to focus on adding value in other areas.”
All UNE bases are FEA optimized and machined on five sides in single setup for highest overall precision. This allows for simplified installation with no foundation work required, and 3-point leveling on machines rated up to 1,000 mm length.
UNE Series Overview:
-
Three two-spindle models available with maximum hole diameters of 12 mm, 20 mm
and 32 mm. Hole diameters even greater when used in single-spindle mode
-
Two single-spindle models available with maximum hole diameters of 25 mm and 40
mm
-
Five rated workpiece designation options between 750 mm and 3,000 mm
-
Solid-carbide, brazed and indexable gundrill tools
-
Automation ready
Contact Details
Related Glossary Terms
- coolant
coolant
Fluid that reduces temperature buildup at the tool/workpiece interface during machining. Normally takes the form of a liquid such as soluble or chemical mixtures (semisynthetic, synthetic) but can be pressurized air or other gas. Because of water’s ability to absorb great quantities of heat, it is widely used as a coolant and vehicle for various cutting compounds, with the water-to-compound ratio varying with the machining task. See cutting fluid; semisynthetic cutting fluid; soluble-oil cutting fluid; synthetic cutting fluid.
- fatigue
fatigue
Phenomenon leading to fracture under repeated or fluctuating stresses having a maximum value less than the tensile strength of the material. Fatigue fractures are progressive, beginning as minute cracks that grow under the action of the fluctuating stress.
- gundrill
gundrill
Self-guided drill for producing deep holes with good accuracy and fine surface finish. Has coolant passages that deliver coolant to the tool/workpiece interface at high pressure.
- gundrilling
gundrilling
Drilling process using a self-guiding tool to produce deep, precise holes. High-pressure coolant is fed to the cutting area, usually through the gundrill’s shank.
- lathe
lathe
Turning machine capable of sawing, milling, grinding, gear-cutting, drilling, reaming, boring, threading, facing, chamfering, grooving, knurling, spinning, parting, necking, taper-cutting, and cam- and eccentric-cutting, as well as step- and straight-turning. Comes in a variety of forms, ranging from manual to semiautomatic to fully automatic, with major types being engine lathes, turning and contouring lathes, turret lathes and numerical-control lathes. The engine lathe consists of a headstock and spindle, tailstock, bed, carriage (complete with apron) and cross slides. Features include gear- (speed) and feed-selector levers, toolpost, compound rest, lead screw and reversing lead screw, threading dial and rapid-traverse lever. Special lathe types include through-the-spindle, camshaft and crankshaft, brake drum and rotor, spinning and gun-barrel machines. Toolroom and bench lathes are used for precision work; the former for tool-and-die work and similar tasks, the latter for small workpieces (instruments, watches), normally without a power feed. Models are typically designated according to their “swing,” or the largest-diameter workpiece that can be rotated; bed length, or the distance between centers; and horsepower generated. See turning machine.
- machining center
machining center
CNC machine tool capable of drilling, reaming, tapping, milling and boring. Normally comes with an automatic toolchanger. See automatic toolchanger.