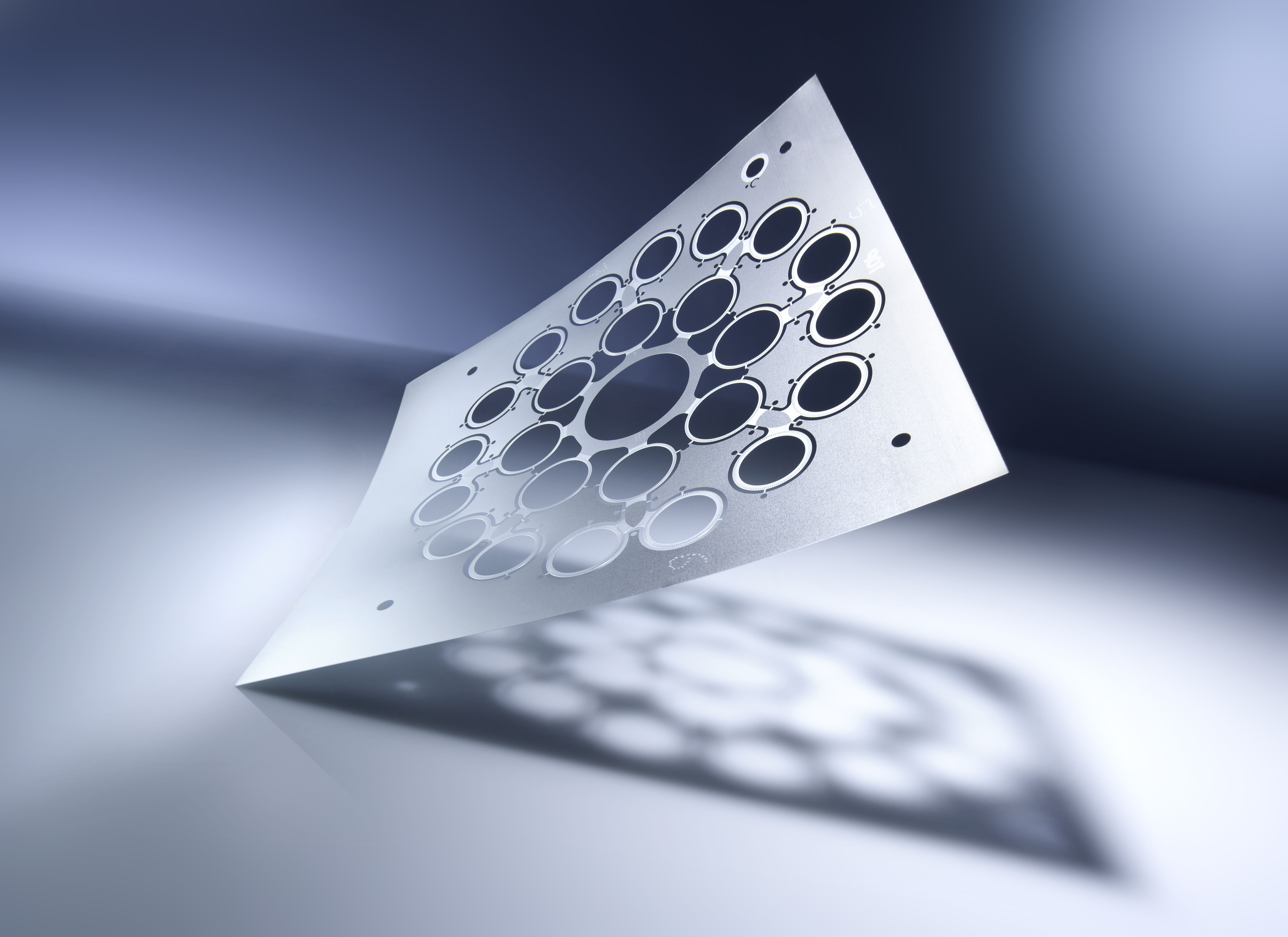
Leading European photochemical etching specialist micrometal GmbH (incorporating HP Etch and Etchform) has perfected using the PCE process for the production of ultraprecise metal parts and components and over the years has become renowned for the production of extremely exacting mesh and filters.
Advantages
PCE is a fast, efficient, and cost-effective method for the manufacture of small precision metal parts, and is well suited for development, prototype, and production volumes, and can ramp up from low to high volume runs extremely quickly. Photo-etched parts are burr and stress-free, the complexity of shape is unlimited, and there is absolute flexibility to change the design at any time as the process uses easily altered digital or glass tooling.
The company, micrometal, has taken these advantages to the next level through its use of proprietary liquid photoresist, high-resolution tooling, and extensive process control innovations. micrometal provides significantly higher precision and consistency than any other etching company.
When applied specifically to the manufacture of filters, PCE is characterized by several process advantages. Lead times are reduced dramatically — as are contingent costs — as tooling setup and iterations (which are often necessary) are quick and relatively simple. Being digital, the tooling for PCE can be manipulated on screen with ease and take a matter of hours rather than the days or weeks that would be expected with traditional processes.
Tooling never wears
Of particular interest to filter manufacturers, special features such as conical holes and complex aperture arrays can be incorporated without cost penalty, as with photo etching component features are machined simultaneously meaning you only pay for the first hole.
Using the PCE process, micrometal can produce filters in almost any metal – including hard-to-machine metals such as titanium and aluminum – and varying bar sizes and open area ratios can be incorporated to control flow rates across the filter. A key advantage: = etched filters provide comparable filtration quality (particle size) while offering significantly improved flow characteristics due to the smaller wall widths between holes.
Also, as PCE uses fluid to remove metal, it does not produce straight or orthogonal walls and edge profiles. Instead, the PCE process produces a rounding effect which, coupled with the ability to tightly control the etched profiles, can allow for the creation of special features and functionality in filters that alternative machining processes cannot achieve. For instance, holes can be etched at an angle to create very specific flow characteristics in addition to particle filtration.
Many industries demand the manufacture of increasingly intricate and geometrically complex filters, which are often designed with custom and non-standard diffusers/passages and aperture arrangements for a wide range of industrial applications.
To meet these requirements, OEMs need to choose a precise and versatile manufacturing technology tailored to the needs of companies requiring innovative filters and fabrics. This is where the micrometal Etching Group's PCE process comes into play.
The speed, cost efficiency, and accuracy of the PCE process are critical for filter applications. So is the fact that parts are stress- and burr-free, geometric complexity is not constrained and does not increase costs, and design changes are quick and simple. At micrometal, we routinely make fuel system filters, filtration grilles, automotive interior grilles, and filters for implantable medical devices and diagnostic equipment which all benefit from our unique PCE process.
micrometal has evolved the PCE process to make what is already a process synonymous with extreme accuracy and precision even more precise. The company uses a liquid resist only a few microns thick as compared to the much thicker industry standard dry resist which compromises part precision and tolerance attainment. With the liquid resist, micrometal can achieve extremely small 25-micron feature sizes, minimum hole diameter of 80% of the material thickness, and single-digit micron tolerances repeatably.
When applied to the production of filters, this can produce exceptional
features not possible using any other fabrication process including traditional
PCE.
Summary
PCE is best suited to the fabrication of complex parts with high degrees of accuracy such as meshes and filters, and parts that rely on the integrity of the material. In addition to our use of wet resist instead of dry resist, whereas most PCE service suppliers use digital photo tooling created on films, micrometal uses photo tooling created on glass, which caters to the many applications that require extreme precision. Glass photo tooling can achieve tolerances in the range of 1-2 microns, and negates issues with distortion due to environmental factors such as humidity that are a constant problem when using film tooling. This is why micrometal is the go-to supplier of intricate, often safety-critical, precision filters for leading names across a range of high-tech industry sectors.
Contact Details
Related Glossary Terms
- burr
burr
Stringy portions of material formed on workpiece edges during machining. Often sharp. Can be removed with hand files, abrasive wheels or belts, wire wheels, abrasive-fiber brushes, waterjet equipment or other methods.
- micron
micron
Measure of length that is equal to one-millionth of a meter.
- process control
process control
Method of monitoring a process. Relates to electronic hardware and instrumentation used in automated process control. See in-process gaging, inspection; SPC, statistical process control.
- tolerance
tolerance
Minimum and maximum amount a workpiece dimension is allowed to vary from a set standard and still be acceptable.