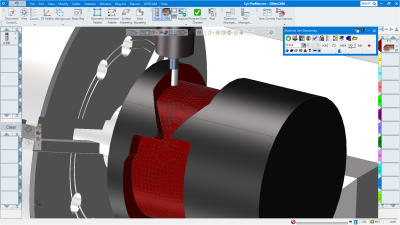
GibbsCAM will showcase its latest Simply Powerful CAM software at IMTS 2022 in September. GibbsCAM product experts will be in booth #338880 to highlight the powerful new features of version 2023, which is due to be released just weeks after the show.
GibbsCAM Vice President Nick Spurrett asserts, “We are truly excited to showcase our latest GibbsCAM release. It is packed with features and already receiving really positive reviews from our reseller network and beta program customers.”
One of the major developments for this version is the introduction of PrimeTurningTM, a high performance turning strategy for Sandvik Coromant and CoroTurn Prime Type A and Type B inserts which allows optimum feed rate adjustment for accurate cutting in either direction.
GibbsCAM GO Turning can now specify Rake and Back Relief for tool inserts to define the 3D geometry of the tool inserts more accurately. VoluTurn has been updated to include ‘Active Chip Thickness Control’ which allows the manipulation of the maximum thickness of the chips to increase productivity by optimizing cutting feed rates. Also added is an option for Lathe Drilling with counter-rotating tools which instructs the live tooling spindle to turn in the opposite direction at a specified RPM to increase spindle speed and material removal rates.
The Elliptical Contour process may now be used for elliptical bores inside of solid parts. Thread Turning operations are expanded with Face Threading, Variable Pitch Threading, Multi-pitch, and Position Tool Front options. In addition, a new highly productive tool type, Multifunction Insert Drill, has been added as a periphery insert that can seamlessly switch between turning, lathe drilling, and mill drilling without retraction or tool change motions.
Cylindrical milling in GibbsCAM 2023 is easier with direct selection of a part slice in the depth axis. Select a closed profile to machine a cylindrical boss or pocket, or select two loops to machine a groove or ring.
New Spiral Boring cuts a spiral out to the full diameter at each Z step, which increases cutting feed rate and depth due to a more consistent tool load.
Organizing parts is easier than ever to match the way you work. The ability to earmark parts by work group or coordinate system, create operation groups, and specify active and inactive operations, helps users to track part information throughout the CAM process.
GibbsCAM will exhibit alongside Cimatron in the Machinery Hall booth #338880 as key partners in the Sandvik Design and Planning Automation division. GibbsCAM VP Spurrett confirms, “Sandvik’s investment in this business segment represents a commitment toward a greater total solution for manufacturers.”
GibbsCAM software programs, simulates, and controls any CNC machine—from 2D to 5-axis milling, turning, Multi-Task Machining (MTM), including Swiss, and wire-EDM. Additionally, GibbsCAM’s in-process probing reduces handling for total accuracy, and a comprehensive CNC solution.
Contact Details
Related Glossary Terms
- boring
boring
Enlarging a hole that already has been drilled or cored. Generally, it is an operation of truing the previously drilled hole with a single-point, lathe-type tool. Boring is essentially internal turning, in that usually a single-point cutting tool forms the internal shape. Some tools are available with two cutting edges to balance cutting forces.
- computer numerical control ( CNC)
computer numerical control ( CNC)
Microprocessor-based controller dedicated to a machine tool that permits the creation or modification of parts. Programmed numerical control activates the machine’s servos and spindle drives and controls the various machining operations. See DNC, direct numerical control; NC, numerical control.
- computer-aided manufacturing ( CAM)
computer-aided manufacturing ( CAM)
Use of computers to control machining and manufacturing processes.
- feed
feed
Rate of change of position of the tool as a whole, relative to the workpiece while cutting.
- gang cutting ( milling)
gang cutting ( milling)
Machining with several cutters mounted on a single arbor, generally for simultaneous cutting.
- lathe
lathe
Turning machine capable of sawing, milling, grinding, gear-cutting, drilling, reaming, boring, threading, facing, chamfering, grooving, knurling, spinning, parting, necking, taper-cutting, and cam- and eccentric-cutting, as well as step- and straight-turning. Comes in a variety of forms, ranging from manual to semiautomatic to fully automatic, with major types being engine lathes, turning and contouring lathes, turret lathes and numerical-control lathes. The engine lathe consists of a headstock and spindle, tailstock, bed, carriage (complete with apron) and cross slides. Features include gear- (speed) and feed-selector levers, toolpost, compound rest, lead screw and reversing lead screw, threading dial and rapid-traverse lever. Special lathe types include through-the-spindle, camshaft and crankshaft, brake drum and rotor, spinning and gun-barrel machines. Toolroom and bench lathes are used for precision work; the former for tool-and-die work and similar tasks, the latter for small workpieces (instruments, watches), normally without a power feed. Models are typically designated according to their “swing,” or the largest-diameter workpiece that can be rotated; bed length, or the distance between centers; and horsepower generated. See turning machine.
- milling
milling
Machining operation in which metal or other material is removed by applying power to a rotating cutter. In vertical milling, the cutting tool is mounted vertically on the spindle. In horizontal milling, the cutting tool is mounted horizontally, either directly on the spindle or on an arbor. Horizontal milling is further broken down into conventional milling, where the cutter rotates opposite the direction of feed, or “up” into the workpiece; and climb milling, where the cutter rotates in the direction of feed, or “down” into the workpiece. Milling operations include plane or surface milling, endmilling, facemilling, angle milling, form milling and profiling.
- milling machine ( mill)
milling machine ( mill)
Runs endmills and arbor-mounted milling cutters. Features include a head with a spindle that drives the cutters; a column, knee and table that provide motion in the three Cartesian axes; and a base that supports the components and houses the cutting-fluid pump and reservoir. The work is mounted on the table and fed into the rotating cutter or endmill to accomplish the milling steps; vertical milling machines also feed endmills into the work by means of a spindle-mounted quill. Models range from small manual machines to big bed-type and duplex mills. All take one of three basic forms: vertical, horizontal or convertible horizontal/vertical. Vertical machines may be knee-type (the table is mounted on a knee that can be elevated) or bed-type (the table is securely supported and only moves horizontally). In general, horizontal machines are bigger and more powerful, while vertical machines are lighter but more versatile and easier to set up and operate.
- pitch
pitch
1. On a saw blade, the number of teeth per inch. 2. In threading, the number of threads per inch.
- rake
rake
Angle of inclination between the face of the cutting tool and the workpiece. If the face of the tool lies in a plane through the axis of the workpiece, the tool is said to have a neutral, or zero, rake. If the inclination of the tool face makes the cutting edge more acute than when the rake angle is zero, the rake is positive. If the inclination of the tool face makes the cutting edge less acute or more blunt than when the rake angle is zero, the rake is negative.
- relief
relief
Space provided behind the cutting edges to prevent rubbing. Sometimes called primary relief. Secondary relief provides additional space behind primary relief. Relief on end teeth is axial relief; relief on side teeth is peripheral relief.
- threading
threading
Process of both external (e.g., thread milling) and internal (e.g., tapping, thread milling) cutting, turning and rolling of threads into particular material. Standardized specifications are available to determine the desired results of the threading process. Numerous thread-series designations are written for specific applications. Threading often is performed on a lathe. Specifications such as thread height are critical in determining the strength of the threads. The material used is taken into consideration in determining the expected results of any particular application for that threaded piece. In external threading, a calculated depth is required as well as a particular angle to the cut. To perform internal threading, the exact diameter to bore the hole is critical before threading. The threads are distinguished from one another by the amount of tolerance and/or allowance that is specified. See turning.
- turning
turning
Workpiece is held in a chuck, mounted on a face plate or secured between centers and rotated while a cutting tool, normally a single-point tool, is fed into it along its periphery or across its end or face. Takes the form of straight turning (cutting along the periphery of the workpiece); taper turning (creating a taper); step turning (turning different-size diameters on the same work); chamfering (beveling an edge or shoulder); facing (cutting on an end); turning threads (usually external but can be internal); roughing (high-volume metal removal); and finishing (final light cuts). Performed on lathes, turning centers, chucking machines, automatic screw machines and similar machines.