Dear Doc: I took your course, and you said that in 99% of grinding operations there’s no significant difference between up-grinding and down-grinding. But I think that our case falls in that 1%. Due to centrifugal expansion, we have to cylindrical-plunge-grind our workpiece at the speed it runs in its actual application, which is 3,000 rpm. Our machine is set up to go unidirectional. Will that be a problem? Our workpiece is 200 mm in diameter, and our wheel is 450 mm in diameter running at 1,800 rpm.
The Doc replies: Yes, this would be one of the rare cases in which there will be a big difference between up-grinding (also called anti-directional) and down-grinding (also called unidirectional). Here’s why.
Imagine you’re a single grit on the wheel. As the wheel plunges into the workpiece, you will carve out a chip. If the wheel is moving fast, you will carve out a thin chip. If the wheel is moving slowly, you will carve out a thicker chip.
What we care about is how fast the wheel is moving relative to the workpiece. In the vast majority of cases, the wheel is moving so much faster than the workpiece (say, 500 times faster) that we just ignore the velocity of the workpiece. Theoretically, we are in error. But an error of 0.2% is trivial, and we ignore it.
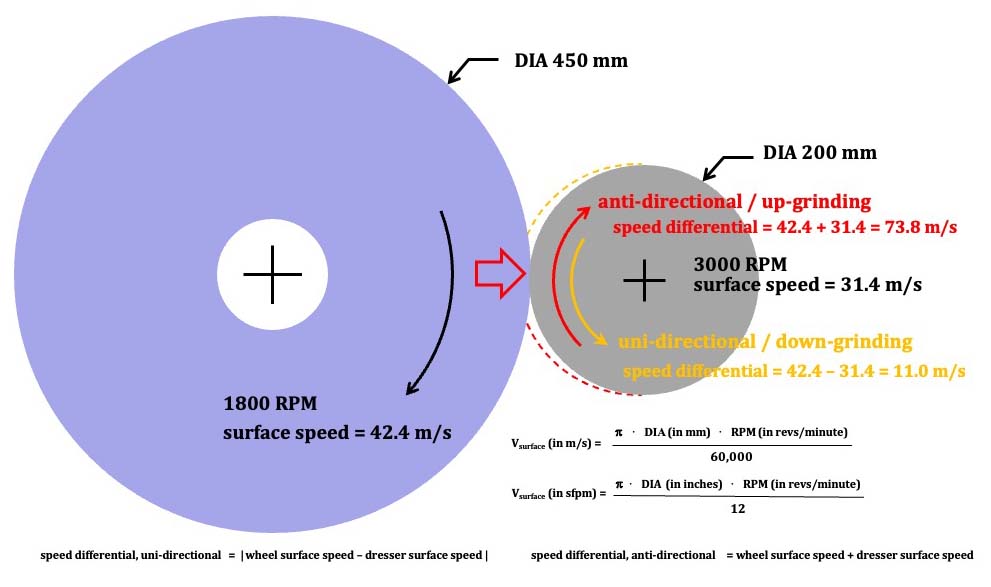
In your situation, however, your workpiece is moving almost as fast as your wheel, 31.4 m/s versus 42.4 m/s. (See the figure.) Remember, we care about the relative speed, or the speed differential. If you’re going anti-directionally, the speed differential is 73.8 m/s (42.4 + 31.4). If unidirectionally, it’s 11 m/s (42.4 - 31.4). That’s a huge difference. If you’re grinding unidirectionally, that’s akin to grinding with a wheel speed of 11 m/s. That’s low — and will give you larger chip thickness, more wheel wear and a rougher surface finish. If you go anti-directionally, that’s akin to grinding with a wheel speed of 73.8 m/s. That gives a smaller chip thickness and (usually but not always) less wheel wear, more heat generation and a smoother surface finish.
In your case, 11 m/s is probably too small of a differential, and 73.8 is a bit on the high side. If you went unidirectionally with a wheel speed of 60 m/s, that’d give you a differential of 28.6 m/s (60 - 31.4). That’s more reasonable. If you must go anti-directionally, maybe 25 m/s on your wheel speed would drop the directional from 73.8 m/s to 56.4 m/s (25 + 31.4).
Notice that by changing between uni and anti, your material removal rate doesn’t change. Nor does your cycle time change. To visualize all this, I like to imagine myself on a train going 42.4 mph. If I pass a train going in the same direction at 31.4 mph, I’m going 11 mph faster than the people on that train. That’s akin to unidirectional. If I pass a train going 31.4 mph but in the opposite direction, I’m going 73.8 mph faster than that train. That’s akin to anti-directional. And if I pass a pedestrian walking 0.1 mph? Well, it doesn’t really matter which direction he’s walking. I’m going a lot faster than he is. And I usually ignore his speed.
Related Glossary Terms
- grinding
grinding
Machining operation in which material is removed from the workpiece by a powered abrasive wheel, stone, belt, paste, sheet, compound, slurry, etc. Takes various forms: surface grinding (creates flat and/or squared surfaces); cylindrical grinding (for external cylindrical and tapered shapes, fillets, undercuts, etc.); centerless grinding; chamfering; thread and form grinding; tool and cutter grinding; offhand grinding; lapping and polishing (grinding with extremely fine grits to create ultrasmooth surfaces); honing; and disc grinding.