It might seem counterintuitive to build up something to tear down another object, but toolmakers are using additive manufacturing technology to 3D-print cutting tools. However, the objective is not to eliminate conventional production of cutting tools but rather to print ones that would be impossible or cost-prohibitive to create another way for targeted applications.
“We don’t just print tools because we have the capability to do it,” said Ingo Grillenberger, product manager for Pittsburgh-based Kennametal Inc. “Rather, we’re strategically leveraging the unique benefits of 3D printing where it makes sense from a customer standpoint in order to solve specific challenges.”
Going Electric
One cutting tool that the company found suitable for 3D printing some of the components is the RIQ stator bore tool for finishing three diameters of an aluminum electric vehicle engine housing in one operation.
According to Kennametal, by machining three diameters in one operation, the tool ensures the alignment and concentricity of the machined surfaces while significantly reducing setup and cycle times.
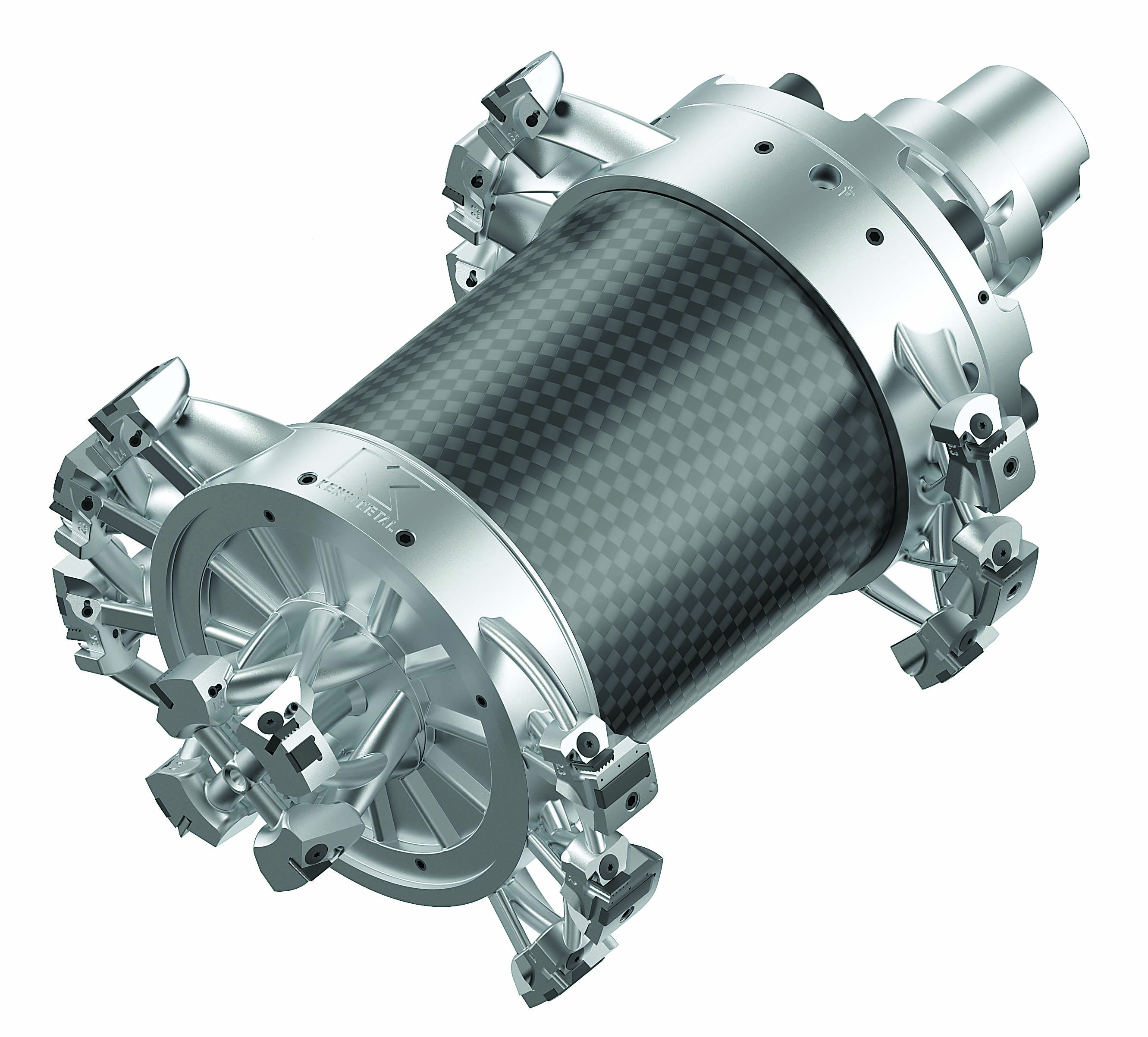
“Some of the features on this tool are simply not possible to manufacture with traditional manufacturing methods,” Grillenberger said.
He said one specific feature is the coolant channels through the tool’s airfoil-shaped arms, enabling coolant to be applied at the exact position and angle required after flowing smoothly through corners and bends.
“You cannot manufacture that in the traditional way because there are too many corners,” Grillenberger said. “You would have to drill too many angles. Here, 3D printing is a real problem-solver.”
He said the tool manufacturer used finite element analysis and calculation methods to design the tool and prints it with laser powder bed melting.
The latest version of the stator bore tool is about 20% lighter than the first-generation one and weighs 7.3 kg (16.1 lbs.).
“We reduced weight as much as possible without compromising the tool’s performance and durability,” Grillenberger said.
The lightweight, 3D-printed combination tool reportedly enables a fast tool change and rotation even on low-horsepower machines.
“You can accelerate and decelerate light tools faster than heavy tools,” Grillenberger said. “It’s also more energy-efficient to speed up and slow down lighter tools than heavier ones, and machine components, such as bearings, are less stressed when running lighter tools. Part manufacturers must also account for a tool’s tilting moment in addition to its weight. If they are too heavy, the toolchanger will have difficulties to move the tool to the spindle, and the connection process will not work properly.”
Last but not least, he said lightweight tools enhance worker safety.
“Imagine you have a machine spindle that is difficult to reach,” Grillenberger said. “It’s much easier to bring a 7-kg (15.4-lb.) tool to that spindle than a 20-kg (44.1-lb.) tool.”
Tools on a Diet
Star Cutter Co. in Farmington Hills, Michigan, is another cutting tool manufacturer 3D printing tools to significantly reduce their weight, said Jamie Dunneback, sales manager of round tool divisions. The company has an exclusive contract to sell tools from Ostrach, Germany-headquartered Neher Group, which Star Cutter distributes through its sister company Star SU LLC in Hoffman Estates, Illinois.
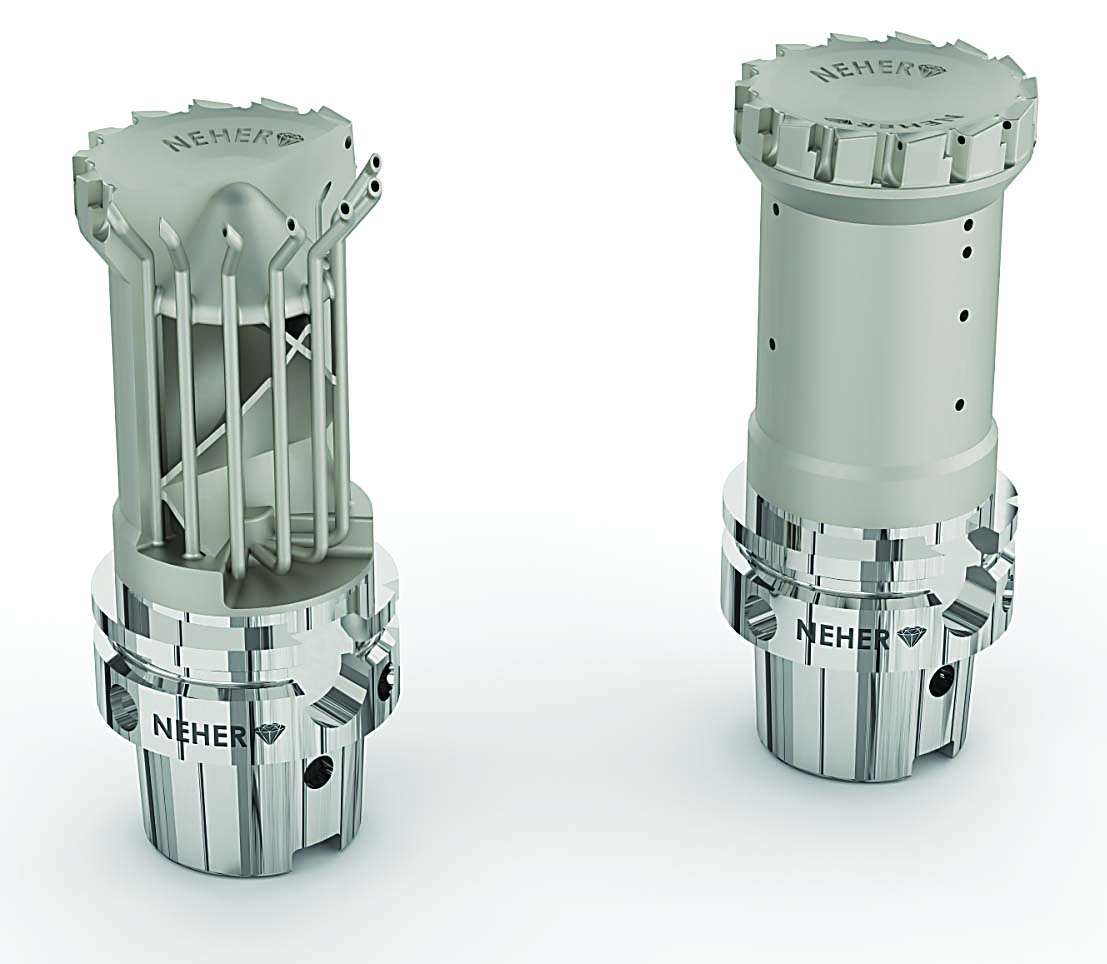
He said Neher purchased its first 3D printer in 2016 and began printing tools in 2020 on DMG Mori Lasertec 30 Dual selective laser melting machines. Nearly all of Neher’s 3D-printed tools are specials focused on large interpolating tools, such as reamers and milling cutters. Similar to Kennametal, one targeted application is machining stator housings for electric vehicles.
By 3D printing those tools for finishing large diameters, as well as other large cutters, Dunneback said Neher can reduce tool weight by up to 30%.
“It still maintains its torsional stiffness,” he said, “so the performance of the body is intact. Lightening up can be very important, especially in the aerospace business where they specify the actual max weight that a tool can be that they’re using in their process, and sometimes it is a struggle trying to get those weights.”
Dunneback said weight reduction primarily is achieved by creating a honeycomb internal lattice structure in tool bodies.
“The inner structure is where we lighten the product more than anything,” he said.
Dunneback said less tool weight means that less weight is exerted on the machine spindle, which helps with overall preventive maintenance for the spindle. In addition, when an end user has a machining center with an HSK 63 spindle interface, for example, and it should be an HSK 100 based on the weight of a conventionally manufactured tool, running a lighter 3D-printed tool can make the machine more capable.
“The worst case that we’re seeing is a tool getting dropped because of its weight,” he said, “falling out of the toolchanger because it slips from the spindle.”
In addition to being able to accurately place coolant channels of any size at any direction and anywhere they are needed in a tool body, Dunneback said additive manufacturing enables toolmakers to optimize those channels for minimal quantity lubrication applications. For both MQL and high-pressure coolant applications, consistently and correctly targeted coolant delivery can extend tool life.
“We’ve reported improvement in tool life up to 50% in some cases,” he said.
When a 3D-printed tool body becomes too worn, Dunneback said it can be reconditioned many times like any conventional body. Star Cutter reconditions tools at its facility in Farmington Hills.
“We will remove the diamond that was originally manufactured, install new diamond and finish the tool to the original condition,” he said.
Stanley X, the innovation business of Stanley Black & Decker Inc., is another company researching 3D-printed tools to optimize cooling channels, said President Michelle Bockman, who is based in Sunnyvale, California.
“Those are high-value applications that we’re trying to dig into and determine if there’s value there for our end customer,” she said.
Printing Carbide
The tool bodies that manufacturers have introduced to the market use conventionally produced inserts made of carbide and other cutting tool materials or have superhard cutting edges brazed onto them. Hyperion Materials & Technologies in Columbus, Ohio, however, developed a printable carbide powder and acquired a binder jetting system to 3D-print carbide, said Biju Varghese, vice president of the engineered solutions business and global research development.
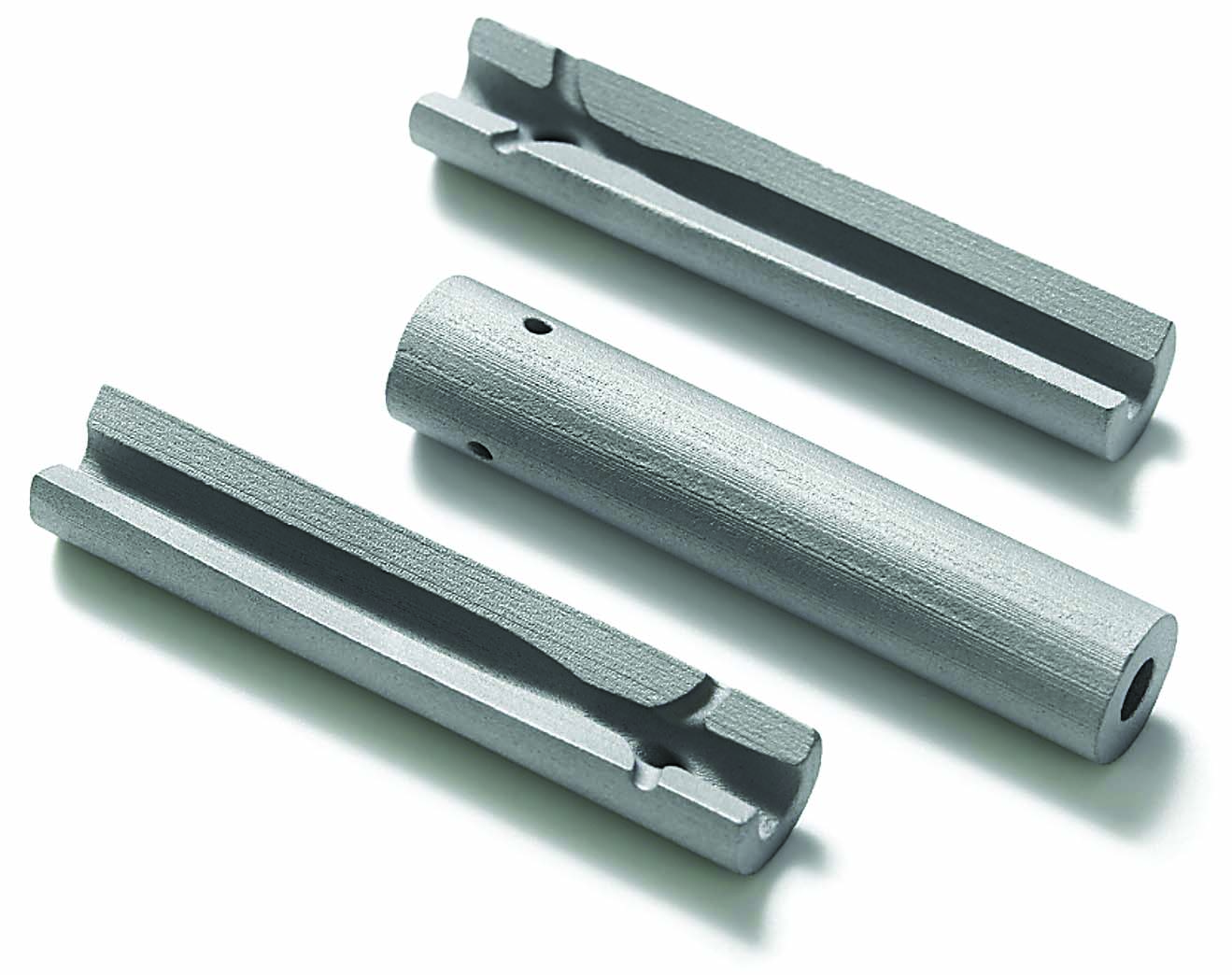
Although cutting tools, including solid-carbide cutters with special features, are part of the company’s focus in 3D printing carbide, he said other applications, such as wear parts and flow control components, are the bigger focus. The main challenge for 3D printing carbide inserts, for example, is producing them at anywhere near the speed that is achieved with conventional compacting and sintering technology.
“There are large production plants that probably produce anywhere from 1 (million) to 3 million inserts a week,” Varghese said.
He said it is challenging to produce via additive manufacturing the vast array of grades that are available.
“And each of those grades (has) very specific properties,” Varghese said. “We are continually working to expand the portfolio of grades that can be 3D-printed. In the next couple of years, we will be in a much better position than previously to produce a wide variety of grades using this technology.”
In addition, he said many inserts have complex geometries that require tight tolerances that toolmakers can achieve only with current commercially available technology.
“We are not there today,” Varghese said.
Nonetheless, he said his company can take advantage of additive manufacturing capabilities to print carbide rod preforms with radically changing channels to ensure that coolant is directed precisely to the cutting zone and delivered with as little turbulence as possible directly at the targeted location. Printing unique channel profiles, such as a peanut-shaped one, are also possible.
Developing the process for 3D printing carbide required four part steps and one modeling step to predict shrinkage during sintering, which might be symmetrical or asymmetrical based on part features, Varghese explained. The first part was developing the powder and making sure that it could flow correctly through the nozzle to form the green body and be sintered into a dense body without porosity.
“After a couple years of intense work,” he said, “we can replicate very faithfully the properties and material quality of what we get from the pressing and sintering.”
Varghese said the second step was developing the printing technology itself. In general, the binder jetting system builds a carbide part layer by layer, with a binder holding together the powder for the desired part while the unbound bed of powder is left behind.
The third step involved handling and cleaning the printed parts, he said, so no remnant powder granules remain in complex internal cavities. A granule measures from 20 to 70 µm (0.0008" to 0.0028").
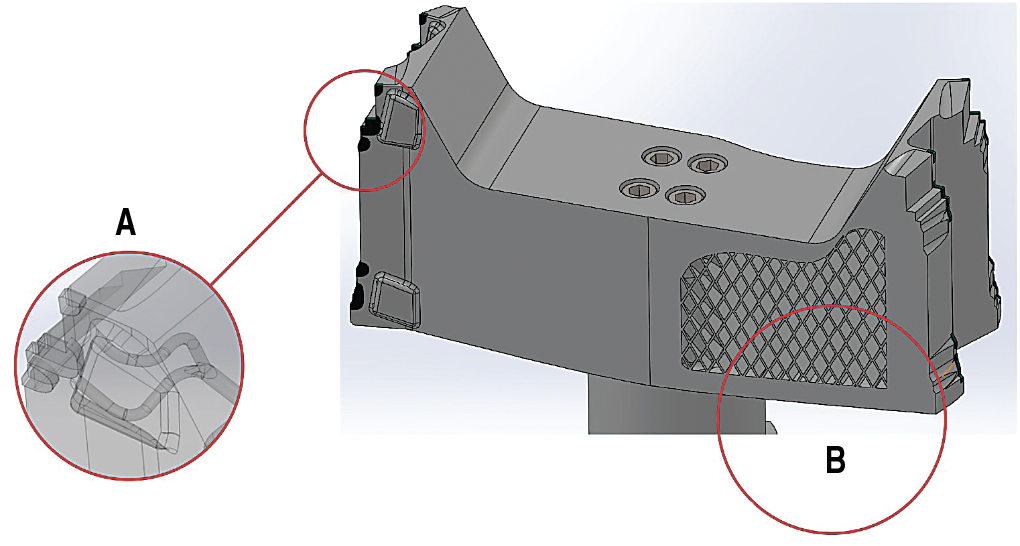
“Even one little granule that sticks on there and gets sintered totally alters what you want to do,” Varghese said.
The final part step was sintering the green body.
“We had to develop a proprietary sintering technology to get properties equivalent to those as the present compacting technology,” Varghese said.
Unlike the conventional pressing and sintering process in which hollow-sphere granules break and compact effectively, he explained that no mechanical force is applied to 3D-printed granules in the green body state. Therefore, Hyperion Materials & Technologies needed a method to fill in those pores, or voids, and achieved that by altering the sintering cycle in terms of temperature, time and some of the pressures exerted.
The company established an R&D and manufacturing center in Barcelona, Spain, six years ago to work on advanced materials and 3D printing carbide. Varghese said wear resistance and hardness of the 3D-printed carbide was only about 60% and 60% to 70%, respectively, of conventional carbide when the project started.
“Right now,” he said, “we can make carbide with the same properties as conventional carbide.”
Varghese said Hyperion Materials & Technologies has launched 3D-printed carbide components to the market and is working with customers to develop novel solutions. In addition, the company still is deciding whether to release the proprietary 3D-printable carbide powder to the market.
“It’s beyond the beta testing point,” he said, “so it might be something we release in a few years.”
Regardless, Varghese said 3D printing has a place in the spectrum of process technologies to produce cutting tools.
“It definitely offers an opportunity to take some of the cutting tool and wear component performance to the next level,” he said. “It allows you to engineer cutting tools with much more complex designs.”
Contact Details
Contact Details
Contact Details
Related Glossary Terms
- coolant
coolant
Fluid that reduces temperature buildup at the tool/workpiece interface during machining. Normally takes the form of a liquid such as soluble or chemical mixtures (semisynthetic, synthetic) but can be pressurized air or other gas. Because of water’s ability to absorb great quantities of heat, it is widely used as a coolant and vehicle for various cutting compounds, with the water-to-compound ratio varying with the machining task. See cutting fluid; semisynthetic cutting fluid; soluble-oil cutting fluid; synthetic cutting fluid.
- cutting tool materials
cutting tool materials
Cutting tool materials include cemented carbides, ceramics, cermets, polycrystalline diamond, polycrystalline cubic boron nitride, some grades of tool steels and high-speed steels. See HSS, high-speed steels; PCBN, polycrystalline cubic boron nitride; PCD, polycrystalline diamond.
- gang cutting ( milling)
gang cutting ( milling)
Machining with several cutters mounted on a single arbor, generally for simultaneous cutting.
- hardness
hardness
Hardness is a measure of the resistance of a material to surface indentation or abrasion. There is no absolute scale for hardness. In order to express hardness quantitatively, each type of test has its own scale, which defines hardness. Indentation hardness obtained through static methods is measured by Brinell, Rockwell, Vickers and Knoop tests. Hardness without indentation is measured by a dynamic method, known as the Scleroscope test.
- lapping compound( powder)
lapping compound( powder)
Light, abrasive material used for finishing a surface.
- machining center
machining center
CNC machine tool capable of drilling, reaming, tapping, milling and boring. Normally comes with an automatic toolchanger. See automatic toolchanger.
- milling
milling
Machining operation in which metal or other material is removed by applying power to a rotating cutter. In vertical milling, the cutting tool is mounted vertically on the spindle. In horizontal milling, the cutting tool is mounted horizontally, either directly on the spindle or on an arbor. Horizontal milling is further broken down into conventional milling, where the cutter rotates opposite the direction of feed, or “up” into the workpiece; and climb milling, where the cutter rotates in the direction of feed, or “down” into the workpiece. Milling operations include plane or surface milling, endmilling, facemilling, angle milling, form milling and profiling.
- sintering
sintering
Bonding of adjacent surfaces in a mass of particles by molecular or atomic attraction on heating at high temperatures below the melting temperature of any constituent in the material. Sintering strengthens and increases the density of a powder mass and recrystallizes powder metals.
- stiffness
stiffness
1. Ability of a material or part to resist elastic deflection. 2. The rate of stress with respect to strain; the greater the stress required to produce a given strain, the stiffer the material is said to be. See dynamic stiffness; static stiffness.
- toolchanger
toolchanger
Carriage or drum attached to a machining center that holds tools until needed; when a tool is needed, the toolchanger inserts the tool into the machine spindle. See automatic toolchanger.
- wear resistance
wear resistance
Ability of the tool to withstand stresses that cause it to wear during cutting; an attribute linked to alloy composition, base material, thermal conditions, type of tooling and operation and other variables.
Contributors
Hyperion Materials & Technologies
800-343-0636
www.hyperionmt.com
Kennametal Inc.
800-835-3668
www.kennametal.com
Stanley X
860-225-5111
www.stanleyx.com
Star Cutter Co.
248-474-8200
www.starcutter.com