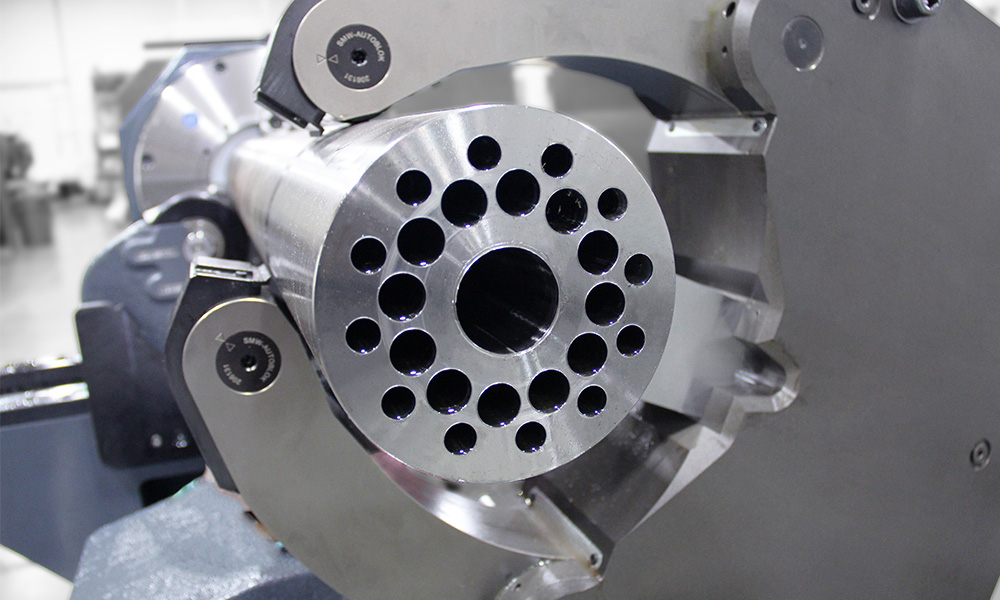
In a routine drilling operation on a milling machine or drill press, a drill’s cutting edges rotate against a stationary workpiece. The opposite is true in holemaking on a turning machine where a stationary drill advances into a rotating workpiece. Either of these drilling methods produce sufficient reliability and hole quality for a wide range of applications. However, other tactics are necessary to produce more exacting tolerances and larger depth-to-diameter ratios.
Drill and workpiece rotation has a major influence on a hole’s concentricity – a key measure of drilling accuracy. When the drill alone rotates in a horizontal setup common for deep hole drilling, accuracy will vary as gravity acts on the drilling tool. A rotating drill can produce sufficient concentricity in relatively shallow holes, but performance will suffer as holes become deeper and less forgiving tolerance wise.
On the other hand, because the direction of gravitational forces relative to the workpiece constantly changes when the drill is stationary and the workpiece rotates, that arrangement can produce holes approximately twice as concentric as the rotating drill approach. While shops can perform rotating-workpiece deep hole drilling on a turning machine, a dedicated deep hole drilling machine using what’s known as counter-rotation will net much better results.
Benefits of counter-rotation
A drilling setup that involves both the drill and workpiece rotating in opposite directions will balance out drilling forces, which are never static in a constant net direction. The balanced forces keep the drill from drifting for a much more concentric hole. With the right equipment and setup, counter-rotation is possible for smaller gundrilled holes as well as larger holes drilled with BTA tooling.
In counter-rotation testing, UNISIG drilled a ¼"-dia. hole in a 30"-long, ¾"-dia. OD, 4140HT steel workpiece. This 120:1 depth-to-diameter application is one typically found in the production of power transmission shafts or aerospace linkages.
Drill drift at the 30" hole depth was measured via ultrasound. With a rotating drill and stationary workpiece, drill drift was 0.026"; a stationary drill and rotating workpiece exhibited 0.015" drift; and when both the drill and the workpiece were rotating, drill drift was only 0.009". It should be noted that results will vary due to many factors, including material, depth-to-diameter ratio and the specific tooling involved.
Dedicated deep hole drilling machines
Even with careful application of drill and workpiece counter-rotation techniques, typical machining centers – if equipped for counter rotation – usually do not have the alignment capabilities needed to consistently produce high-quality holes of 20:1 or greater depth-to-diameter ratio. Superior alignment is critical in maintaining concentricity.
In dedicated deep-hole drilling equipment, the machine base, rotating bearing groups and spindles as well as tool and workpiece supports are all designed with alignment as a first priority. Deep-hole drilling machines also emphasize control of other machining and environmental factors such as consistent temperature maintenance.
Some machines not originally engineered for counter-rotation operation can be retrofitted with a secondary counter-rotating group, but the alignment processes needed to make the arrangement work will be challenging and expensive. Additionally, a machine originally designed to employ counter-rotation will be manageable for nearly any operator. Dedicated deep hole drilling machines, for instance, include operator interfaces that provide detailed process information and maximize control over drilling parameters to enable accurate, efficient and repeatable production.
Basic application guidelines
Every deep-hole drilling application is essentially unique. However, general application guidance for counter-rotating operations includes allowing one-third of the total drilling speed to come from workpiece rotation and two-thirds from the drill. Operating parameters can then be adjusted to maximize drilling speeds and accuracy.
Such counter-rotation techniques provide a way to achieve accuracy and production requirements in deep-hole drilling and are especially effective when drilling holes of 40:1 depth to diameter ratios or more. Counter-rotation generates higher levels of concentricity that enable use of optimal feed rates while also extending tool life. The result is production of more parts per hour with fewer tool changes.
Learn more about counter-rotation and what it can do for you at www.UNISIG.com.
Contact Details
Related Glossary Terms
- centers
centers
Cone-shaped pins that support a workpiece by one or two ends during machining. The centers fit into holes drilled in the workpiece ends. Centers that turn with the workpiece are called “live” centers; those that do not are called “dead” centers.
- depth-to-diameter ratio
depth-to-diameter ratio
Ratio of the depth of a hole compared to the diameter of the tool used to make the hole.
- drilling machine ( drill press)
drilling machine ( drill press)
Machine designed to rotate end-cutting tools. Can also be used for reaming, tapping, countersinking, counterboring, spotfacing and boring.
- drilling machine ( drill press)2
drilling machine ( drill press)
Machine designed to rotate end-cutting tools. Can also be used for reaming, tapping, countersinking, counterboring, spotfacing and boring.
- drilling tool ( drill or drill bit)
drilling tool ( drill or drill bit)
End-cutting tool for drilling. Tool has shank, body and angled face with cutting edges that drill the hole. Drills range in size from “microdrills” a few thousandths of an inch in diameter up to spade drills, which may cut holes several inches in diameter. Drills may have tapered shanks with a driving tang and fit directly into a spindle or adapter, or they may have straight shanks and be chuck-mounted. The rake angle varies with the material drilled. Styles include twist drills, straight-flute drills, half-round and flat drills, oil-hole drills, indexable drills and specials.
- feed
feed
Rate of change of position of the tool as a whole, relative to the workpiece while cutting.
- gang cutting ( milling)
gang cutting ( milling)
Machining with several cutters mounted on a single arbor, generally for simultaneous cutting.
- milling
milling
Machining operation in which metal or other material is removed by applying power to a rotating cutter. In vertical milling, the cutting tool is mounted vertically on the spindle. In horizontal milling, the cutting tool is mounted horizontally, either directly on the spindle or on an arbor. Horizontal milling is further broken down into conventional milling, where the cutter rotates opposite the direction of feed, or “up” into the workpiece; and climb milling, where the cutter rotates in the direction of feed, or “down” into the workpiece. Milling operations include plane or surface milling, endmilling, facemilling, angle milling, form milling and profiling.
- milling machine ( mill)
milling machine ( mill)
Runs endmills and arbor-mounted milling cutters. Features include a head with a spindle that drives the cutters; a column, knee and table that provide motion in the three Cartesian axes; and a base that supports the components and houses the cutting-fluid pump and reservoir. The work is mounted on the table and fed into the rotating cutter or endmill to accomplish the milling steps; vertical milling machines also feed endmills into the work by means of a spindle-mounted quill. Models range from small manual machines to big bed-type and duplex mills. All take one of three basic forms: vertical, horizontal or convertible horizontal/vertical. Vertical machines may be knee-type (the table is mounted on a knee that can be elevated) or bed-type (the table is securely supported and only moves horizontally). In general, horizontal machines are bigger and more powerful, while vertical machines are lighter but more versatile and easier to set up and operate.
- outer diameter ( OD)
outer diameter ( OD)
Dimension that defines the exterior diameter of a cylindrical or round part. See ID, inner diameter.
- tolerance
tolerance
Minimum and maximum amount a workpiece dimension is allowed to vary from a set standard and still be acceptable.
- turning
turning
Workpiece is held in a chuck, mounted on a face plate or secured between centers and rotated while a cutting tool, normally a single-point tool, is fed into it along its periphery or across its end or face. Takes the form of straight turning (cutting along the periphery of the workpiece); taper turning (creating a taper); step turning (turning different-size diameters on the same work); chamfering (beveling an edge or shoulder); facing (cutting on an end); turning threads (usually external but can be internal); roughing (high-volume metal removal); and finishing (final light cuts). Performed on lathes, turning centers, chucking machines, automatic screw machines and similar machines.
- turning machine
turning machine
Any machine that rotates a workpiece while feeding a cutting tool into it. See lathe.