A parts manufacturer never wants to tell its biggest customer that it cannot deliver parts on time because the manufacturer cannot get a cutting tool. That was the potential scenario for Concept Metals Group Inc.’s machining division in Comstock Park, Michigan, said Engineer/Supervisor Chad Schwierking.
He said Concept Metals Group produces about 50,000 of those shafts per year, which require 5/16"-8 threads on the ends of them. The manufacturer threads them on a manual Brown & Sharpe cam- and gear-driven screw machine. The parts are made with 12L14 or 1215 steel.
Schwierking said the thread chasers that Concept Metals Group was using had unacceptably long lead times and an inflated price tag. The company needed a better option.
“I just started to try and find other companies that were making chasers that could be delivered in a reasonable time, not 16 to 18 weeks, and they weren’t going to charge us three to four times normal pricing,” he said.
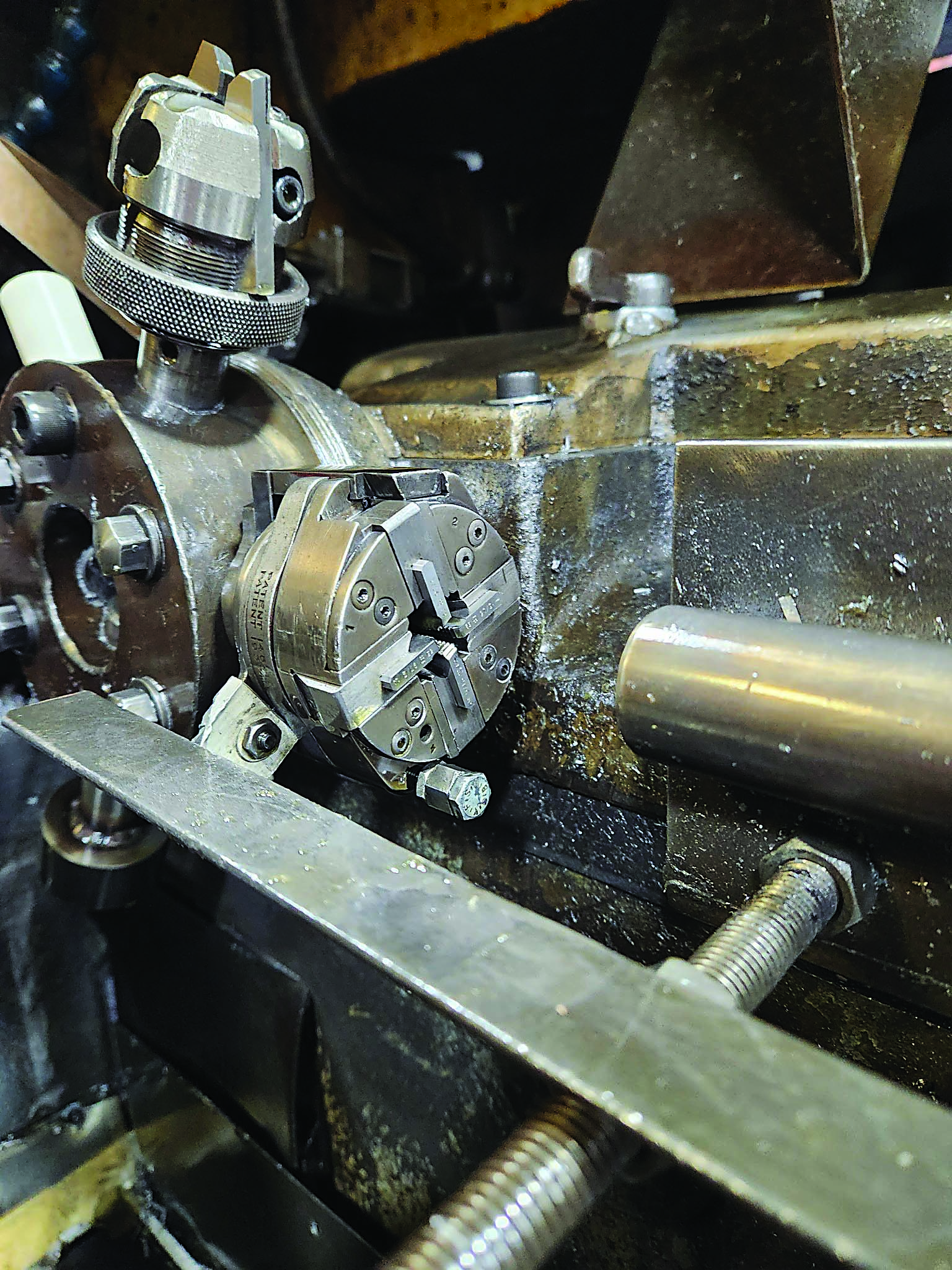
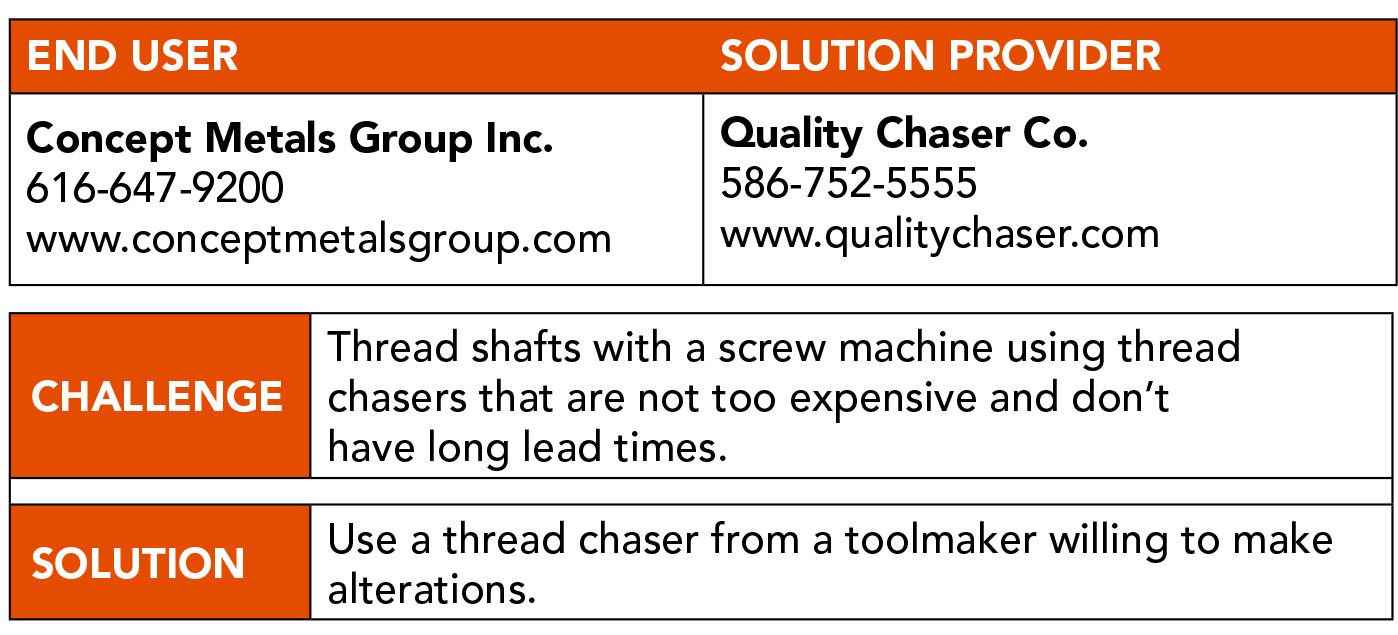
Schwierking tried to obtain the thread chasers from at least three other companies but determined they were distributors of the chaser that Concept Metals Group already was purchasing. He eventually found Quality Chaser Co. in Romeo, Michigan.
“Quality Chaser was the first one I had run across that was actually making the chaser,” he said.
Schwierking requested and received chasers to test. He tried the first style on the Brown & Sharpe machine and said he noticed go/no-go inspection gauge issues in which either the “go” wouldn’t go on or the no-go would. In addition, there were finish problems, such as thread tearing and “hairs” on the threads.
“Your inserts need to be cutting freely and accurately in order for the gauging to work,” he said.
It might seem logical for an end user to continue searching for another tool manufacturer to find a solution, but based on his 25-plus years in the machining industry, Schwierking said he can tell when a toolmaker is willing to make the changes needed to get a tool functioning properly.
“They either will tell you right off the bat that they’re into making the changes to whatever you need,” he said, “or they just say that they can’t do that. There was never a time that they said, ‘We don’t think we’re going to be able to figure this out.’”
While not an off-the-shelf product, Quality Chaser reports that it often makes custom chasers for customers to maximize performance and customer satisfaction.
“With expert engineering and tenacity, this toolmaker came through for us and has become our go-to source for threading chasers,” Schwierking said. “It also didn’t hurt Quality Chaser’s position as the leading candidate because its lead times were at least a third quicker and its prices at least half compared to the previous chaser supplier.”
Confident that Quality Chaser wouldn’t give up, he worked with the toolmaker to suggest modifications to cutting geometry, such as the relief angle, clearance angle, chipbreaker and hone. He said Denny Kubczak, sales and service specialist, is his main contact there.
“We just (kept) working with him and giving him feedback for what was going on with the insert so that they could make some adjustments and then give us another iteration to try,” Schwierking said.
A week or so after providing feedback, he said a new iteration would arrive.
“They were responding pretty quickly considering, I’m assuming, they had a schedule that they needed to meet, and I didn’t expect them to cut in all the time,” Schwierking said.
After a little more than two months and testing four or five iterations, he said Concept Metals Group had the thread chaser that it needed with no gauging or surface finish issues.
The threading cycle time is the same as when applying the original chaser, and tool life is comparable — “maybe even better,” Schwierking said.
He conceded that Concept Metals Group would not have lost the job if it had failed to find a replacement thread chaser.
“But I don’t know how profitable it would have been considering how expensive the chasers were getting and also the lead time,” Schwierking said.
He said the shorter lead time allows Concept Metals Group to avoid keeping as much inventory of the chasers as the company maintained previously.
Although it took some back and forth, Schwierking said Concept Metals Group has thread chasers that meet its cost and lead time requirements and perform effectively.
“Probably better than they would like because I haven’t had to order many of them,” he said.
Contact Details
Related Glossary Terms
- chipbreaker
chipbreaker
Groove or other tool geometry that breaks chips into small fragments as they come off the workpiece. Designed to prevent chips from becoming so long that they are difficult to control, catch in turning parts and cause safety problems.
- clearance
clearance
Space provided behind a tool’s land or relief to prevent rubbing and subsequent premature deterioration of the tool. See land; relief.
- relief
relief
Space provided behind the cutting edges to prevent rubbing. Sometimes called primary relief. Secondary relief provides additional space behind primary relief. Relief on end teeth is axial relief; relief on side teeth is peripheral relief.
- thread chaser
thread chaser
Die-type external threading tool. Makes final threading pass.
- threading
threading
Process of both external (e.g., thread milling) and internal (e.g., tapping, thread milling) cutting, turning and rolling of threads into particular material. Standardized specifications are available to determine the desired results of the threading process. Numerous thread-series designations are written for specific applications. Threading often is performed on a lathe. Specifications such as thread height are critical in determining the strength of the threads. The material used is taken into consideration in determining the expected results of any particular application for that threaded piece. In external threading, a calculated depth is required as well as a particular angle to the cut. To perform internal threading, the exact diameter to bore the hole is critical before threading. The threads are distinguished from one another by the amount of tolerance and/or allowance that is specified. See turning.