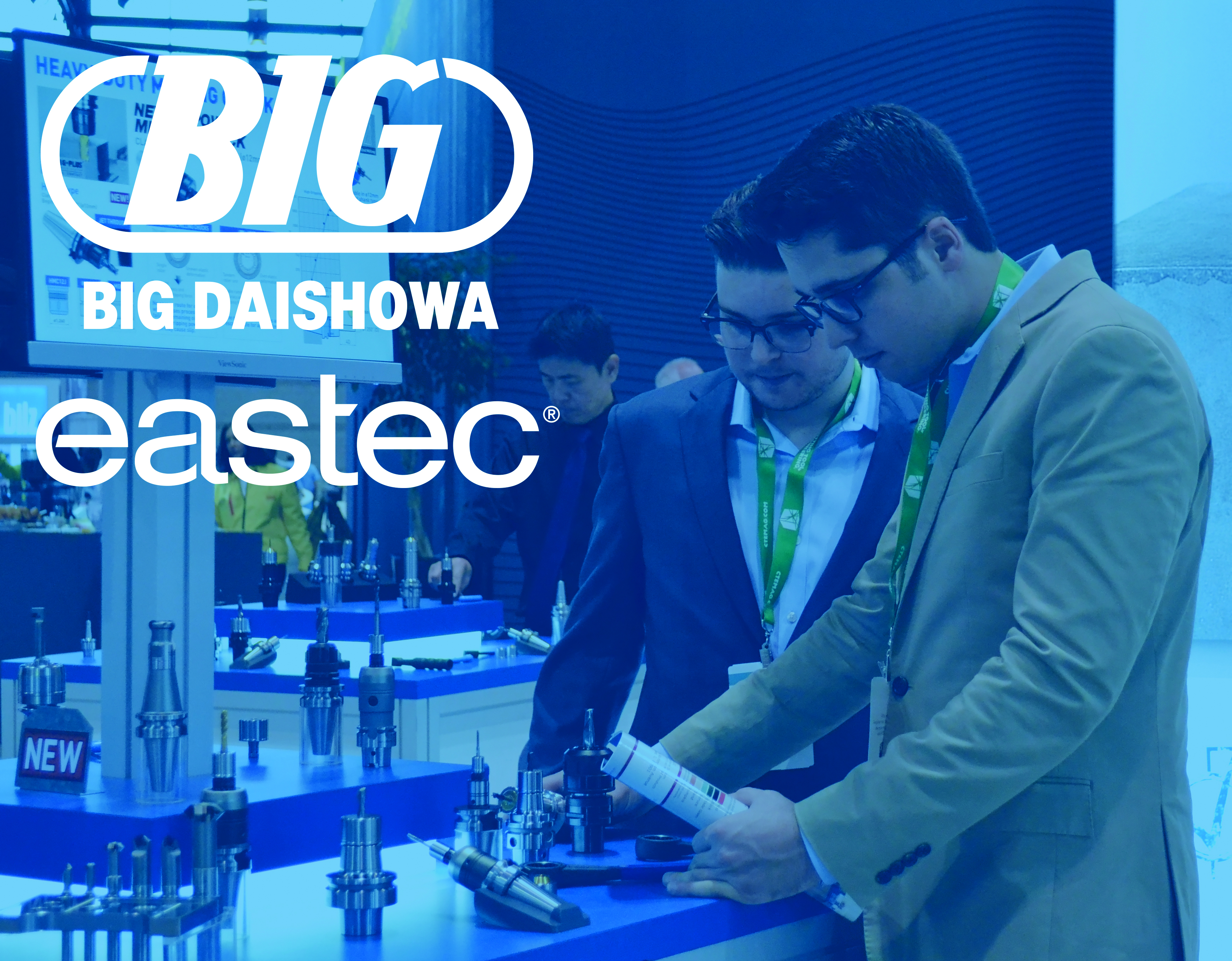
Big Daishowa will exhibit at Eastec at the Eastern States Exposition (Booth 5252) in West Springfield, Mass., May 16-18.
Big Daishowa will have several products and technologies on display, including tool holders; a wide array of boring solutions; and several new products, including:
- SMART DAMPER—Dynamic Damper eliminates chatter in heavy workloads; new additions include the smallest boring head and longest mill holders to date
- C3 PROGRAM—Additions include mono-block holders with a tough and reliable insert clamp that enables highly efficient cutting; square tool holders in 90° and 180° types; and round tool holders with an ultra-slim design
- MEGA 12DS—A new chuck for trochoidal milling with anti-vibration end mills; high rigidity and gripping strength are available in BBT30/40, HSK-A, C for metric, and BCV40 for inch
- EWA—Automatic fine boring system performs boring operations without a human operator; the adjustment range allows for the handling of multiple bore sizes with the same tool and ensures a repeatable boring process
- ESM 168—UNILOCK modular workholding chuck that can be used on the face of 4th- and 5th-axis rotary tables, lathes, or mills where the center of rotation provides a through-hole to bury the workpiece
“We’re excited to return to Eastec and interface with current customers and new prospects,” said Michael Herman, vice president, sales. “Staying ahead of the competition is more important than ever in today’s manufacturing industry, and our premium tooling is designed to give that edge. At Eastec, you can see it all in one visit.”
For more information about Big Daishowa’s presence at the show, and to add the booth to your exhibitor list, click here.
Contact Details
Related Glossary Terms
- boring
boring
Enlarging a hole that already has been drilled or cored. Generally, it is an operation of truing the previously drilled hole with a single-point, lathe-type tool. Boring is essentially internal turning, in that usually a single-point cutting tool forms the internal shape. Some tools are available with two cutting edges to balance cutting forces.
- boring head
boring head
Single- or multiple-point precision tool used to bring an existing hole within dimensional tolerance. The head attaches to a standard toolholder and a mechanism permits fine adjustments to be made to the head within a diameter range.
- chatter
chatter
Condition of vibration involving the machine, workpiece and cutting tool. Once this condition arises, it is often self-sustaining until the problem is corrected. Chatter can be identified when lines or grooves appear at regular intervals in the workpiece. These lines or grooves are caused by the teeth of the cutter as they vibrate in and out of the workpiece and their spacing depends on the frequency of vibration.
- chuck
chuck
Workholding device that affixes to a mill, lathe or drill-press spindle. It holds a tool or workpiece by one end, allowing it to be rotated. May also be fitted to the machine table to hold a workpiece. Two or more adjustable jaws actually hold the tool or part. May be actuated manually, pneumatically, hydraulically or electrically. See collet.
- gang cutting ( milling)
gang cutting ( milling)
Machining with several cutters mounted on a single arbor, generally for simultaneous cutting.
- milling
milling
Machining operation in which metal or other material is removed by applying power to a rotating cutter. In vertical milling, the cutting tool is mounted vertically on the spindle. In horizontal milling, the cutting tool is mounted horizontally, either directly on the spindle or on an arbor. Horizontal milling is further broken down into conventional milling, where the cutter rotates opposite the direction of feed, or “up” into the workpiece; and climb milling, where the cutter rotates in the direction of feed, or “down” into the workpiece. Milling operations include plane or surface milling, endmilling, facemilling, angle milling, form milling and profiling.
- milling machine ( mill)
milling machine ( mill)
Runs endmills and arbor-mounted milling cutters. Features include a head with a spindle that drives the cutters; a column, knee and table that provide motion in the three Cartesian axes; and a base that supports the components and houses the cutting-fluid pump and reservoir. The work is mounted on the table and fed into the rotating cutter or endmill to accomplish the milling steps; vertical milling machines also feed endmills into the work by means of a spindle-mounted quill. Models range from small manual machines to big bed-type and duplex mills. All take one of three basic forms: vertical, horizontal or convertible horizontal/vertical. Vertical machines may be knee-type (the table is mounted on a knee that can be elevated) or bed-type (the table is securely supported and only moves horizontally). In general, horizontal machines are bigger and more powerful, while vertical machines are lighter but more versatile and easier to set up and operate.
- through-hole
through-hole
Hole or cavity cut in a solid shape that connects with other holes or extends all the way through the workpiece.