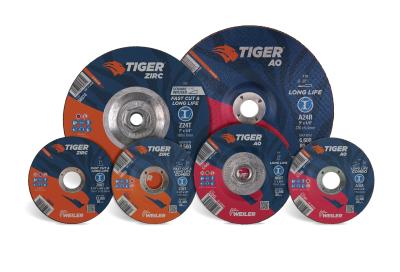
Weiler Abrasives, a leading provider of abrasives, power brushes and maintenance products for surface conditioning, is excited to announce the next evolution of abrasives — Tiger 2.0 zirconia alumina and aluminum oxide cutting, grinding and combo wheels. Designed for demanding metal fabrication industries like shipbuilding, pressure vessel and heavy equipment fabrication, these abrasives help cut through inefficiencies, safety issues and labor shortages that prevent companies from doing their best work.
“We understand that our customers’ production environments are ever-changing and many are challenged with doing more work with less labor. We listened to their feedback to determine what they want and need in their abrasives,” said Tony Hufford, category manager – Metal Fabrication at Weiler Abrasives. “The result is wheels that offer fast cut-rates with extended life that we developed through countless hours of trials and validation to provide the best product to market.”
In addition to offering fast cutting speed, Tiger 2.0 wheels last up to 40% longer to increase efficiency in operations’ cutting and grinding applications. The wheels feature an award-winning blotter design that includes an industry-first, patent-pending Optimum Use Line. The line is a visual indicator that helps the operator use the wheel to its full life. This innovation reduces changeovers, allowing for greater productivity while also reducing waste and abrasive spend. In some cases, users experience three times more efficiency than with their previous abrasives.
Tiger 2.0 grinding wheels feature anti-chipping technology, an advanced bond formulation that reduces uneven edge wear and chipping to improve safety and the user experience and extend wheel life.
All of the wheels deliver smooth, predictable cutting and grinding — making the work safer. The addition of a QR code on the wheels makes it convenient for operators to access crucial safety information where and when they need it.
Weiler Abrasives took today’s labor shortages into consideration when formulating the Tiger 2.0 wheels. The wheels produce consistent results among different users to reduce training time and minimize rework. The wheels also make cutting and grinding easier to lessen operator fatigue and improve employee retention.
Tiger 2.0 wheels are available in Type 1, Type 27 and Type 28 options. These wheels range in size from 4 to 9 inches and are intended for use on portable angle grinders.
Learn more about how Tiger 2.0 can cut through barriers in your operations at weilerabrasives.com/tiger-2.0.
Contact Details
Related Glossary Terms
- abrasive
abrasive
Substance used for grinding, honing, lapping, superfinishing and polishing. Examples include garnet, emery, corundum, silicon carbide, cubic boron nitride and diamond in various grit sizes.
- aluminum oxide
aluminum oxide
Aluminum oxide, also known as corundum, is used in grinding wheels. The chemical formula is Al2O3. Aluminum oxide is the base for ceramics, which are used in cutting tools for high-speed machining with light chip removal. Aluminum oxide is widely used as coating material applied to carbide substrates by chemical vapor deposition. Coated carbide inserts with Al2O3 layers withstand high cutting speeds, as well as abrasive and crater wear.
- cutting speed
cutting speed
Tangential velocity on the surface of the tool or workpiece at the cutting interface. The formula for cutting speed (sfm) is tool diameter 5 0.26 5 spindle speed (rpm). The formula for feed per tooth (fpt) is table feed (ipm)/number of flutes/spindle speed (rpm). The formula for spindle speed (rpm) is cutting speed (sfm) 5 3.82/tool diameter. The formula for table feed (ipm) is feed per tooth (ftp) 5 number of tool flutes 5 spindle speed (rpm).
- fatigue
fatigue
Phenomenon leading to fracture under repeated or fluctuating stresses having a maximum value less than the tensile strength of the material. Fatigue fractures are progressive, beginning as minute cracks that grow under the action of the fluctuating stress.
- grinding
grinding
Machining operation in which material is removed from the workpiece by a powered abrasive wheel, stone, belt, paste, sheet, compound, slurry, etc. Takes various forms: surface grinding (creates flat and/or squared surfaces); cylindrical grinding (for external cylindrical and tapered shapes, fillets, undercuts, etc.); centerless grinding; chamfering; thread and form grinding; tool and cutter grinding; offhand grinding; lapping and polishing (grinding with extremely fine grits to create ultrasmooth surfaces); honing; and disc grinding.