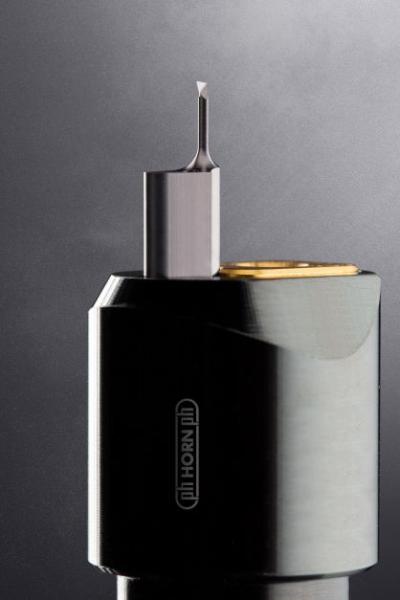
At EMO 2023 in Hannover, Horn presented an innovative extension for the Supermini system in the field of ultra-fine machining. The precision tool manufacturer has added a variant with a precision-ground rake face to the Supermini system especially for ultra-fine machining of bores.
Due to precision grinding of the cutting edge, it is free from notches when magnified approximately 200 times. The tool system can be used from an inside diameter of 0.3 mm (0.012"). The sharp insert geometry enables process reliability even with very small infeed and cutting feed rates. The specially developed coating is suitable for stainless steels, non-ferrous metals and other metallic materials.
The insert of the Supermini Type 105 system requires only one tool holder for well over 1,000 insert variants. This applies equally to left-hand and right-hand versions. The carbide inserts are available in coated and uncoated versions in different grades for every application including hard machining up to 66 HRC. The patented droplet shape of the cross-section has a vibration-damping effect and delivers excellent repeatability when changing the insert. Internal coolant supply to the insert increases tool life, enhances cutting performance and improves chip removal. Horn offers the tools with elements for face clamping. This allows, for example, the insert to be changed easily without having to remove the holder from the machine.
History Horn Supermini:
In 1989, HORN launched the technically superior Supermini system at the world's largest metalworking trade show, EMO in Hannover, Germany. After considerable technical development, it was possible to successfully manufacture precision internal grooving tools for bores down to 5 mm (0.197") in diameter. The Supermini system was born and over time became one of Horn's most successful products. In addition, the Supermini system was the first precision tool to benefit from Horn's own in-house coatings.
Contact Details
Related Glossary Terms
- coolant
coolant
Fluid that reduces temperature buildup at the tool/workpiece interface during machining. Normally takes the form of a liquid such as soluble or chemical mixtures (semisynthetic, synthetic) but can be pressurized air or other gas. Because of water’s ability to absorb great quantities of heat, it is widely used as a coolant and vehicle for various cutting compounds, with the water-to-compound ratio varying with the machining task. See cutting fluid; semisynthetic cutting fluid; soluble-oil cutting fluid; synthetic cutting fluid.
- feed
feed
Rate of change of position of the tool as a whole, relative to the workpiece while cutting.
- grinding
grinding
Machining operation in which material is removed from the workpiece by a powered abrasive wheel, stone, belt, paste, sheet, compound, slurry, etc. Takes various forms: surface grinding (creates flat and/or squared surfaces); cylindrical grinding (for external cylindrical and tapered shapes, fillets, undercuts, etc.); centerless grinding; chamfering; thread and form grinding; tool and cutter grinding; offhand grinding; lapping and polishing (grinding with extremely fine grits to create ultrasmooth surfaces); honing; and disc grinding.
- grooving
grooving
Machining grooves and shallow channels. Example: grooving ball-bearing raceways. Typically performed by tools that are capable of light cuts at high feed rates. Imparts high-quality finish.
- metalworking
metalworking
Any manufacturing process in which metal is processed or machined such that the workpiece is given a new shape. Broadly defined, the term includes processes such as design and layout, heat-treating, material handling and inspection.
- rake
rake
Angle of inclination between the face of the cutting tool and the workpiece. If the face of the tool lies in a plane through the axis of the workpiece, the tool is said to have a neutral, or zero, rake. If the inclination of the tool face makes the cutting edge more acute than when the rake angle is zero, the rake is positive. If the inclination of the tool face makes the cutting edge less acute or more blunt than when the rake angle is zero, the rake is negative.
- stainless steels
stainless steels
Stainless steels possess high strength, heat resistance, excellent workability and erosion resistance. Four general classes have been developed to cover a range of mechanical and physical properties for particular applications. The four classes are: the austenitic types of the chromium-nickel-manganese 200 series and the chromium-nickel 300 series; the martensitic types of the chromium, hardenable 400 series; the chromium, nonhardenable 400-series ferritic types; and the precipitation-hardening type of chromium-nickel alloys with additional elements that are hardenable by solution treating and aging.