When reduced setup time and increased precision are top tapping priorities, this all-in-one option is designed to fit the bill.
Made by Australia-headquartered ANCA, the TapX CNC tap grinder integrates all the different processes normally required to produce a tap into a single machine. A wide variety of tap types and sizes can be manufactured with only one setup, according to the company.
Typically, four to six different machines are used to grind a tap, each of which produces only one feature, noted ANCA product manager Kaine Mulder. “The factories are huge because they’ll have 20 of one machine down one aisle, 20 of the next machine down the next aisle and so on,” Mulder said. “Whereas with the TapX, you have one machine that does it all.”
This versatility, he explained, stems from the fact that the TapX is a six-axis machine “that can maneuver around and do everything you need to do. With (conventional) machines, the spindle’s generally fixed, and they’ll have fewer axes for maneuvering around the tap.”
With its additional axes, ANCA says the TapX can reduce total setup time from three or four hours to just one, slashing lead times for small to medium-size batch production. In addition, Mulder noted that one-stop grinding improves accuracy because taps are completely manufactured in one setup instead of being moved to multiple machines.
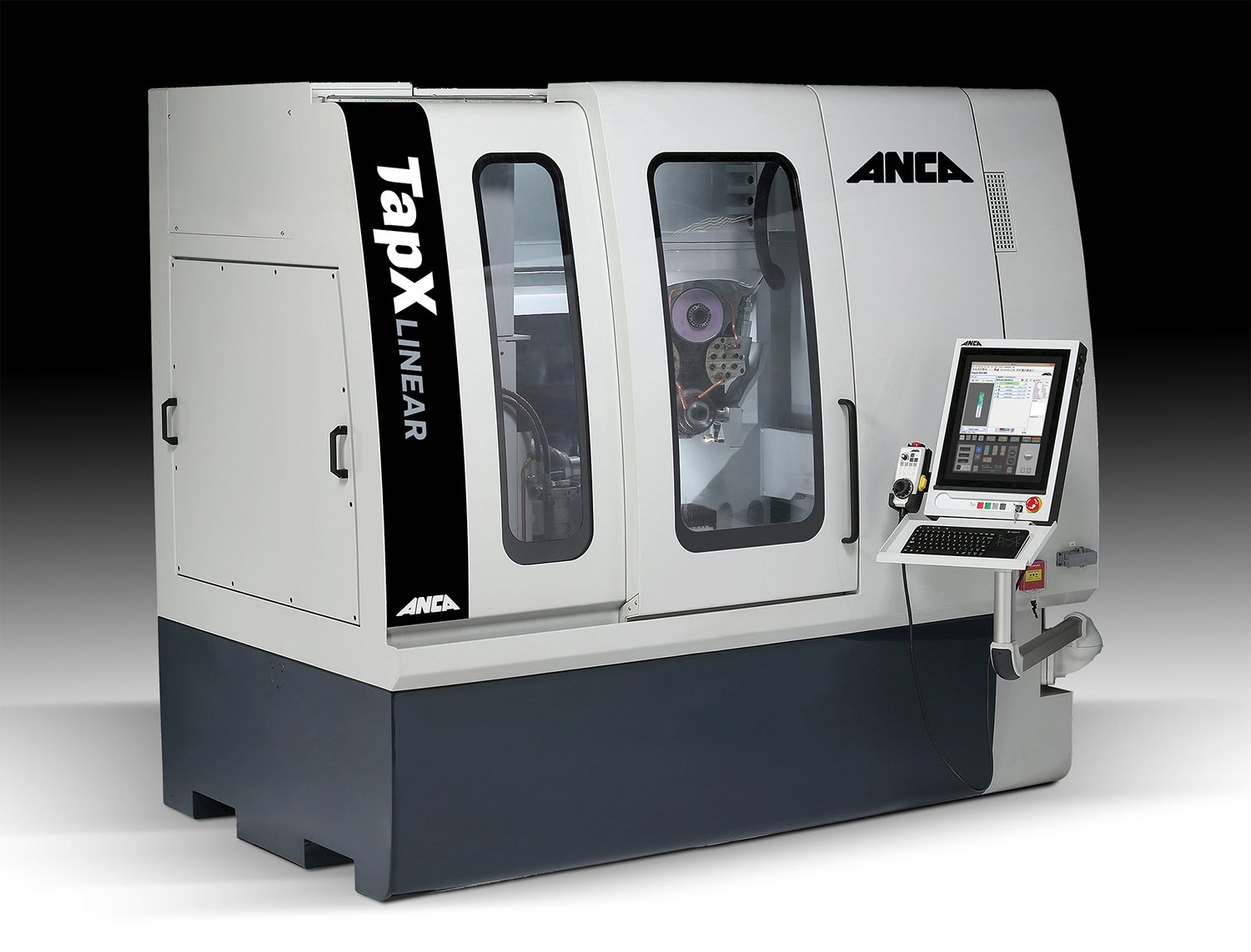
According to ANCA, the TapX also benefits from high rigidity that boosts manufacturing quality and repeatability. In addition, the machine features ANCA’s LinX motors for its linear axes and direct drive technology for the rotary axes. The company points out that the elimination of belts, pulleys and gears improves precision and reliability.
For some users, Mulder said, the TapX is enhanced with ANCA’s Motor Temperature Control (MTC), a patented technology that allows the machine temperature to be controlled during the grinding process. The idea, he explained, is to prevent growth of the spindle – caused by temperature changes – and the resulting machining inaccuracies.
“We’re seeing a lot of good results” with MTC, he reported. “The most important one is a high level of repeatability over a batch. That’s something that you can’t (achieve) with conventional processes.”
At present, Mulder said, customers who want MTC added to the TapX can get it only through a special-order process. But he expects MTC to be a standard option for TapX buyers by the end of the year.
To boost productivity, the TapX is designed to work with automation. “In a conventional process, it’s quite a lot of work to change over the tooling,” Mulder noted. “But with the TapX, you can set up a fully automated process. You can have 10 totally different types of taps set up in a pallet and tell the software what tools are where and what tool file to (use) to grind them. So there’s no big effort in changing over from tool type to tool type.”
On the downside, the TapX comes up short compared to conventional machines when it comes to efficiency in performing each of the individual operations involved in grinding a tap. “The benefit of conventional machines is that they’re highly efficient at doing one operation,” he said. With TapX, therefore, “you sacrifice cycle time to do each operation because it’s doing them all in the one machine but doing (each one) less efficiently.”
This means that, generally speaking, conventional multi-machine tap-grinding processes are more suitable for high-volume production because setup time diminishes in importance as volumes increase. Conversely, “as volumes get lower, setup time becomes a higher percentage of the overall costs,” Mulder noted.
That’s why the TapX is a popular choice for low-volume, high-end work in industries such as automotive and aerospace, he said. “In more advanced markets like the U.S. or Europe, it’s very important to be able to have this sort of flexibility and reduce lead times. That’s where we think the TapX comes into its own.”
Contact Details
Related Glossary Terms
- computer numerical control ( CNC)
computer numerical control ( CNC)
Microprocessor-based controller dedicated to a machine tool that permits the creation or modification of parts. Programmed numerical control activates the machine’s servos and spindle drives and controls the various machining operations. See DNC, direct numerical control; NC, numerical control.
- grinding
grinding
Machining operation in which material is removed from the workpiece by a powered abrasive wheel, stone, belt, paste, sheet, compound, slurry, etc. Takes various forms: surface grinding (creates flat and/or squared surfaces); cylindrical grinding (for external cylindrical and tapered shapes, fillets, undercuts, etc.); centerless grinding; chamfering; thread and form grinding; tool and cutter grinding; offhand grinding; lapping and polishing (grinding with extremely fine grits to create ultrasmooth surfaces); honing; and disc grinding.
- tap
tap
Cylindrical tool that cuts internal threads and has flutes to remove chips and carry tapping fluid to the point of cut. Normally used on a drill press or tapping machine but also may be operated manually. See tapping.
- tapping
tapping
Machining operation in which a tap, with teeth on its periphery, cuts internal threads in a predrilled hole having a smaller diameter than the tap diameter. Threads are formed by a combined rotary and axial-relative motion between tap and workpiece. See tap.