As a machinist, the toolholders you use can have a major impact on your machining operations. From component quality to performance and tool life, having the right toolholder is crucial for success. When evaluating toolholders, there are several key factors to consider.
Rigidity, stability and accuracy
The rigidity and stability of a toolholder is critical for achieving precision and accuracy in your machining operations. Toolholders that are not rigid enough can allow tools to move during cutting, leading to vibration, chatter, poor surface finishes and reduced tool life. Look for toolholders made from high-quality steel or carbides that resist flexing and deformation under load. The interface between the toolholder and the machine should also be optimized to maximize stability.
When evaluating the features of a toolholder more closely, there are some key technical specifications to analyze. Runout tolerance provides an indication of potential deviations to expect in the holder’s alignment. This is measured in microns (μm) — lower runout translates to less deflection and higher stability. Static stiffness refers to the holder’s resistance to deflection under load when the tool is not rotating. This is measured in N/mm, with higher values indicating greater rigidity. Dynamic stiffness accounts for deflection when the holder and tool are rotating and cutting. Damping properties are also important, as damped toolholders can dissipate vibration and stabilize chatter. By comparing factors like runout tolerance, static/dynamic stiffness and damping properties, you can better analyze the rigidity and stability different toolholders can provide for your application.
Clamping and grip
The strength of the clamping mechanism is equally important. Insufficient clamping force can allow movement or pull-out of the cutting tool during operation. This leads to poor maintenance of tolerances and potentially dangerous run-out conditions. Choose tooling systems with robust clamping bolts, screws and wedges to keep tools locked in position under high loads and vibration. Hydraulic clamping systems offer very strong clamping capabilities, and automation is possible.
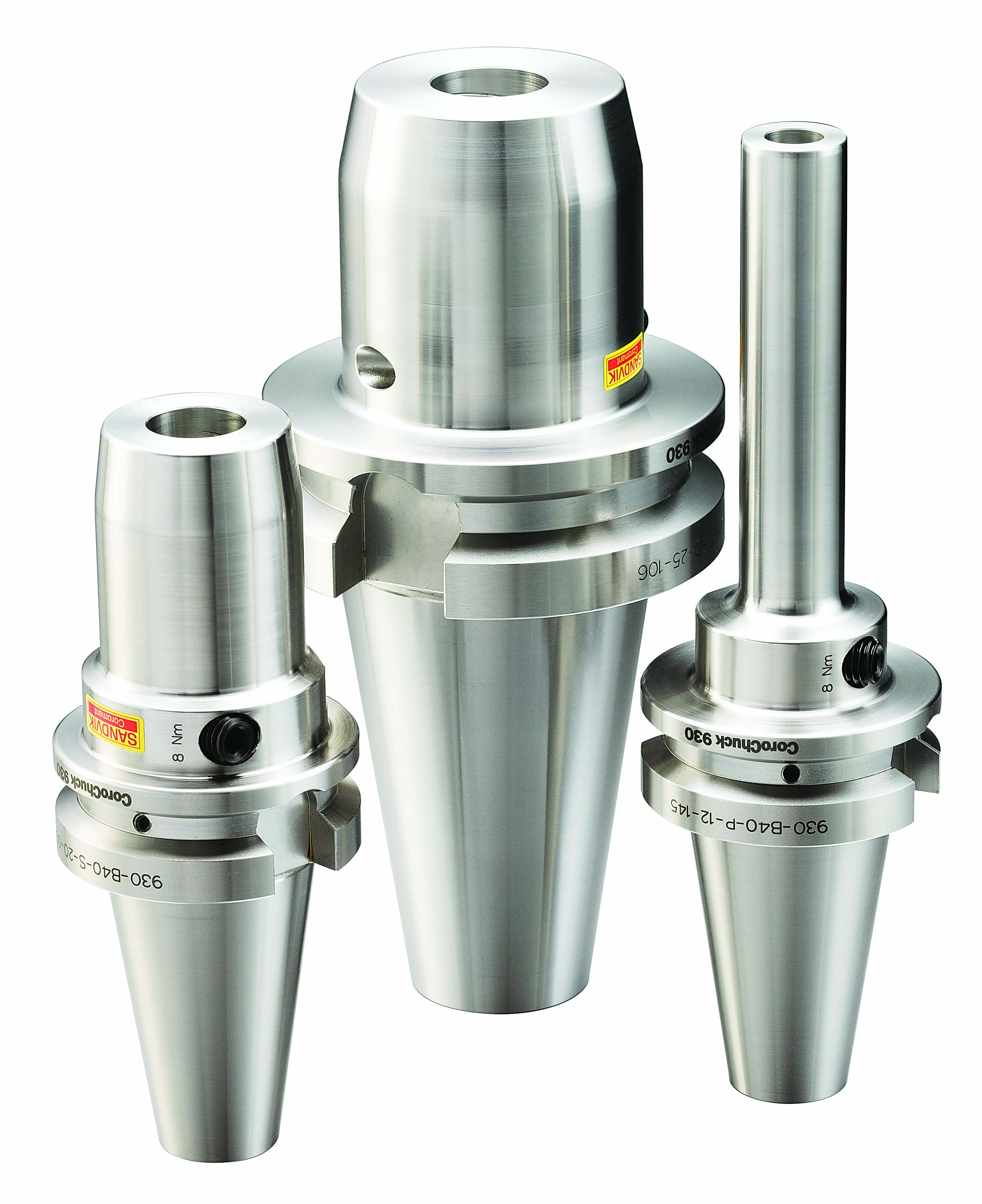
When reviewing the clamping and grip qualities of a toolholder, key metrics to analyze include clamping force, interface pressure and torque capacity. Clamping force is measured in N or lbf and indicates the amount of force applied to secure the tool. Higher values minimize pull-out. Interface pressure in N/mm2 or psi indicates the uniformity and strength of grip at the contact between holder and tool. Torque capacity measured in Nm or ft-lbs defines the maximum torque the clamping mechanism can withstand before loss of contact. Comparing these specifications between different toolholders gives a clearer technical picture of expected clamping and gripping performance. Materials used in the interface, as well as heat treatment and surface finishes, also impact grip. Technical data sheets and testing clamping force and torque capacity can optimize toolholder selection.
Accuracy and repeatability
Top-performing toolholders offer high accuracy and repeatability to achieve consistent results over time. Look for designs that incorporate precision mating surfaces and close tolerance dimensions. Toolholders with hydraulic clamping or heat shrink often outperform traditional mechanical setscrew types when it comes to accuracy and repeatability. This prevents deviations in tool positioning.
Other factors and key technical specifications to look for include runout, eccentricity and indexing repeatability. Runout refers to deviations in the tool’s rotational axis and can be measured in microns. Eccentricity refers to the alignment between the tool’s rotating axis and the center axis of the holder, also measured in microns. Lower runout and eccentricity equate to higher accuracy. Indexing repeatability quantifies the ability to repeatedly index tools to the same position. Spindle interfaces also impact accuracy — interfaces with dual face and taper contact offer highly precise mating for minimal runout. Stiff materials used in the holder body along with heat treatment further enhance dimensional stability and temperature resistance. Using these specifications to compare toolholders enables proper technical analysis of the accuracy and repeatability of different holders.
Accessibility and ease of use
The best toolholders balance performance with practical accessibility and ease of use. Quick-change systems that allow fast indexing of different tools help optimize changeover times. Ergonomic levers, screws and clamps make accessing and securing tools easier for operators. Well-designed interfaces that are intuitive to use also prevent improper setups that can fail in the machine.
When reviewing the accessibility and ease of use of toolholders, some important technical specifications relate to changing times, ergonomics and interface design. For quick-change toolholders, change times are measured in seconds and indicate how rapidly tools can be indexed. Ergonomic factors like the sizes of knobs, levers and gripping surfaces impact accessibility. Optimal interface designs prevent improper tool orientation and enable clear visual confirmation of proper fit. Technical features like taper interface types, torque transmission, thermal expansion properties and standard tool shanks also affect ease of use. Tool weight can affect balancing and should be considered. Analyzing specifications like changeover time, ergonomic design elements and foolproof technical features allows better evaluation of the accessibility and ease of use of different toolholder options.
Tool compatibility
Toolholders must properly accommodate the component to be machined. The shank type, diameter, length and special geometries may be needed. Ensure the toolholder offers full compatibility with the cutting tools to prevent improper fits and tool inaccuracy. This may require using special adapters or tool modifications. Consult your tooling supplier to help with tool selection.
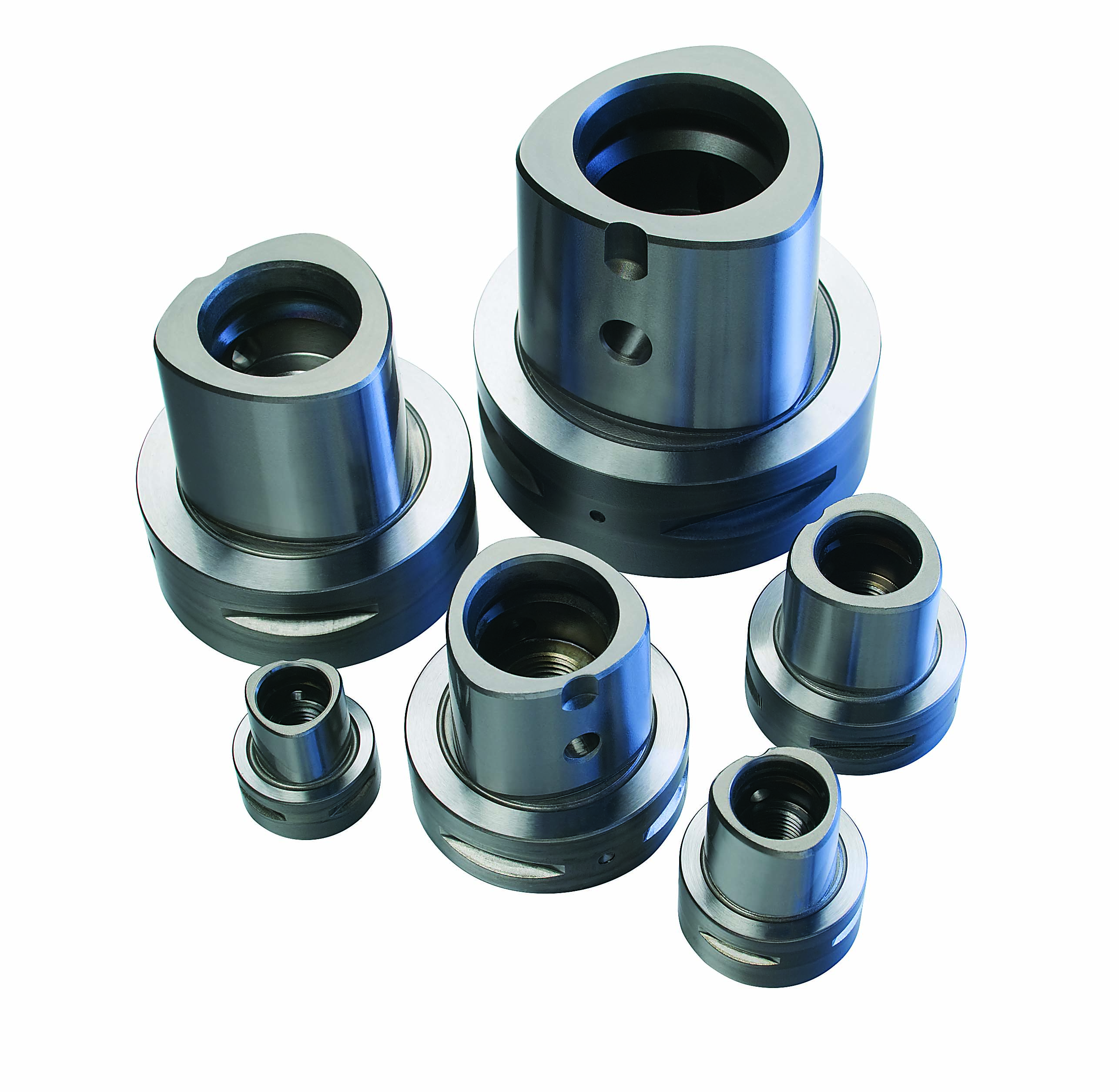
When evaluating toolholder compatibility, key technical specifications to look for include the range of acceptable tool shank diameters, tool shank types, maximum tool length and recommended geometries. The diameter range specifies the minimum and maximum tool diameters that can be effectively clamped. Supported tool shank types indicate compatibility with options like ISO, HSK, Coromant Capto® and others. Maximum tool length defines the longest tools the machine can hold. Tool design is also critical — holders optimized for drills, mills, boring bars, etc. Technical details like the collet style, machine interface, flange dimensions and availability of reducers or adapters also impact which tools can be effectively used. By comparing these factors, you can ensure a given toolholder provides full technical support for your specific cutting tools and processes. This prevents incompatibility and ensures stability.
Coolant delivery
Delivering adequate coolant to the cutting interface is vital for temperature control and chip evacuation. Look for toolholders designed to facilitate coolant delivery through optimal channels and outlets. Through coolant and high-pressure coolant options pair best depending on your tooling and operations. Minimum-quantity lubrication can impact sustainability.
Some additional details about coolant and key technical specifications to analyze include coolant inlet size, maximum coolant pressure, flow rate and coolant routing options. The inlet size (ID) and maximum pressure control the volume and pressure of coolant that can be handled. Flow rate measured in liters or gallons per minute indicates the amount of coolant that can be delivered to the holder and tool. Optimized routing looks at the direction, orientation and location of coolant channels and outlets in relation to the tool tip, material and machining interface. Seals and O-rings help prevent coolant leakage. Comparing these coolant delivery specifications allows proper technical evaluation of internal coolant capabilities and how they align with your machining parameters, tooling and operations. These are important factors to help control heat and chips.
Cost considerations
Toolholders range widely in terms of cost depending on design, material composition and level of precision. While expensive premium holders offer exceptional performance, inexpensive options may provide sufficient capabilities for many general applications.
It’s good to consider a balance between price and performance. Look at tool life and performance gains of higher-cost holders versus lower-cost alternatives to help make the best choice based on your needs and budget constraints.
When evaluating the cost of different toolholders, some key technical specifications to analyze in relation to price include toolholder material composition, precision rating, interface type and design complexity. More expensive, high-performance materials like carbide and ceramics typically cost more than old-fashioned tool steel. Tighter runout tolerances and close precision ratings can also increase cost. Advanced taper interfaces like HSK and Coromant Capto may be more expensive than traditional tapers like 7/24" but they provide added benefits. Additionally, quick-change, hydraulic and shrink-fit holders carry higher price tags than basic collet or endmill holders, but they can be a good investment. Weighing these technical specifications against quoted pricing allows you to better gauge the value of different holders. A more sophisticated holder may warrant a higher price if it delivers significant gains in precision, accuracy and rigidity for your specific application. Consider both budget constraints and performance benefits when assessing cost.
With so many toolholder types and options on the market, it can be challenging to determine what is ideal for your machining operations. Focus on rigid, stable designs with strong clamping mechanisms and high accuracy and repeatability for reliable performance. Tool compatibility, coolant delivery and ease of use are also key considerations depending on your needs. Analyze your specific tools, materials, tolerances and production volumes to strike the right balance between performance and cost when investing in toolholders. With the right holder matched to your tools and application, you can achieve high precision, longer tool life and optimized machining results.
Contact Details
Related Glossary Terms
- boring
boring
Enlarging a hole that already has been drilled or cored. Generally, it is an operation of truing the previously drilled hole with a single-point, lathe-type tool. Boring is essentially internal turning, in that usually a single-point cutting tool forms the internal shape. Some tools are available with two cutting edges to balance cutting forces.
- ceramics
ceramics
Cutting tool materials based on aluminum oxide and silicon nitride. Ceramic tools can withstand higher cutting speeds than cemented carbide tools when machining hardened steels, cast irons and high-temperature alloys.
- chatter
chatter
Condition of vibration involving the machine, workpiece and cutting tool. Once this condition arises, it is often self-sustaining until the problem is corrected. Chatter can be identified when lines or grooves appear at regular intervals in the workpiece. These lines or grooves are caused by the teeth of the cutter as they vibrate in and out of the workpiece and their spacing depends on the frequency of vibration.
- collet
collet
Flexible-sided device that secures a tool or workpiece. Similar in function to a chuck, but can accommodate only a narrow size range. Typically provides greater gripping force and precision than a chuck. See chuck.
- coolant
coolant
Fluid that reduces temperature buildup at the tool/workpiece interface during machining. Normally takes the form of a liquid such as soluble or chemical mixtures (semisynthetic, synthetic) but can be pressurized air or other gas. Because of water’s ability to absorb great quantities of heat, it is widely used as a coolant and vehicle for various cutting compounds, with the water-to-compound ratio varying with the machining task. See cutting fluid; semisynthetic cutting fluid; soluble-oil cutting fluid; synthetic cutting fluid.
- dynamic stiffness
dynamic stiffness
Measure of a machining system’s ability to dampen vibration from a forced input. If the dynamic stiffness of a system is not sufficient to dampen vibration, chatter occurs. See static stiffness; stiffness.
- endmill
endmill
Milling cutter held by its shank that cuts on its periphery and, if so configured, on its free end. Takes a variety of shapes (single- and double-end, roughing, ballnose and cup-end) and sizes (stub, medium, long and extra-long). Also comes with differing numbers of flutes.
- minimum-quantity lubrication
minimum-quantity lubrication
Use of cutting fluids of only a minute amount—typically at a flow rate of 50 to 500 ml/hr.—which is about three to four orders of magnitude lower than the amount commonly used in flood cooling. The concept addresses the issues of environmental intrusiveness and occupational hazards associated with the airborne cutting fluid particles on factory shop floors. The minimization of cutting fluid also saves lubricant costs and the cleaning cycle time for workpieces, tooling and machines. Sometimes referred to as “near-dry lubrication” or “microlubrication.”
- shank
shank
Main body of a tool; the portion of a drill or similar end-held tool that fits into a collet, chuck or similar mounting device.
- static stiffness
static stiffness
Relates to the machine tool and is measured in pounds per inch. Static stiffness indicates how many pounds of force it takes to deflect the spindle a linear distance of 1" in a given direction. See dynamic stiffness; stiffness.
- stiffness
stiffness
1. Ability of a material or part to resist elastic deflection. 2. The rate of stress with respect to strain; the greater the stress required to produce a given strain, the stiffer the material is said to be. See dynamic stiffness; static stiffness.
- tolerance
tolerance
Minimum and maximum amount a workpiece dimension is allowed to vary from a set standard and still be acceptable.
- toolholder
toolholder
Secures a cutting tool during a machining operation. Basic types include block, cartridge, chuck, collet, fixed, modular, quick-change and rotating.