Dear Doc: We grind brittle materials (carbide, cermets, ceramics) and are trying to reduce edge-chipping. Any advice?
The Doc replies: Here are three things you can do:
1. Try a smaller grit size. (Example: Switching from 280-mesh to 400-mesh.)
2. Try a lower grit penetration depth (or aggressiveness, chip thickness, chip load, etc.). Depending on the geometry, this is usually accomplished with a slower feed rate, faster wheel speed and/or smaller depth of cut.
3. Try a sharper wheel. For carbide, this typically means a wheel that isn’t loaded. For cermets and ceramics, this typically means a wheel that isn’t loaded and a wheel that doesn’t contain diamond grits that have become dull.
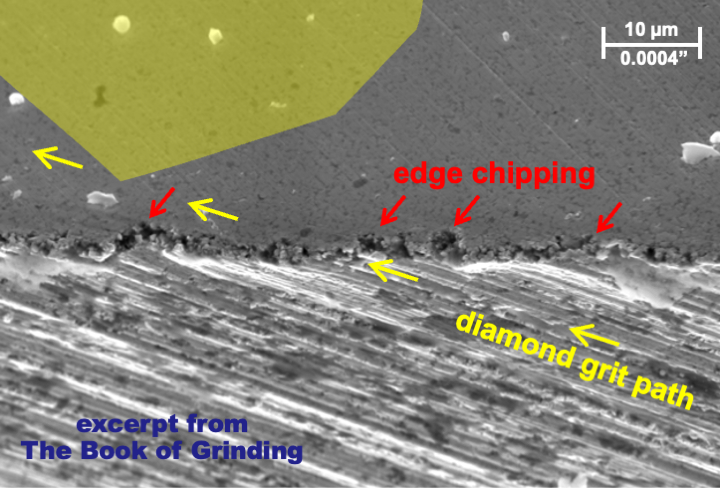
Remember, you will never eliminate edge chipping in brittle materials. All you can do is reduce it.
These suggestions should reduce chipping.
Or they might not help at all. Why? Because your excessive edge-chipping is caused by chatter or vibration. If the wheel is chattering, that means it’s bouncing up and down on the workpiece, causing surges in the forces and grit penetration depth, which in turn increases chipping. Get rid of that chatter and you’ll reduce chipping.
How to reduce chatter? Here are some common solutions to chatter: a stiffer spindle; in surface grinding, slow and deep cuts (instead of fast and shallow cuts); in cylindrical-plunge grinding, slower workpiece RPMs; in cylindrical-traverse grinding, an overlap ratio closer to 1.0.
The excessive edge-chipping may be caused by intermittent wheel-workpiece contact from an imbalanced or eccentric wheel, which causes surges in forces and grit penetration depth. Balancing your wheel or making it concentric with the spindle will help. But here’s something you can do to practically eliminate that intermittent contact: true your wheel—on the same machine and spindle you grind on (without removing the adaptor), at the same wheel speed you use for grinding, and at the same point at which you grind. (If you’re using a resin or metal-bonded wheel, follow up with a wheel sticking.) This doesn’t have to be fancy. Just a few passes to make sure the wheel is running concentric with the spindle.
Finally, you can change the direction of the grits so they are entering and not exiting. This is rarely feasible because of geometric limitations. But occasionally it can be done. Also, putting a dummy workpiece at the exit also helps. Again, it’s usually not feasible.
Related Glossary Terms
- ceramics
ceramics
Cutting tool materials based on aluminum oxide and silicon nitride. Ceramic tools can withstand higher cutting speeds than cemented carbide tools when machining hardened steels, cast irons and high-temperature alloys.
- cermets
cermets
Cutting tool materials based mostly on titanium carbonitride with nickel and/or cobalt binder. Cermets are characterized by high wear resistance due to their chemical and thermal stability. Cermets are able to hold a sharp edge at high cutting speeds and temperatures, which results in exceptional surface finish when machining most types of steels.
- chatter
chatter
Condition of vibration involving the machine, workpiece and cutting tool. Once this condition arises, it is often self-sustaining until the problem is corrected. Chatter can be identified when lines or grooves appear at regular intervals in the workpiece. These lines or grooves are caused by the teeth of the cutter as they vibrate in and out of the workpiece and their spacing depends on the frequency of vibration.
- depth of cut
depth of cut
Distance between the bottom of the cut and the uncut surface of the workpiece, measured in a direction at right angles to the machined surface of the workpiece.
- feed
feed
Rate of change of position of the tool as a whole, relative to the workpiece while cutting.
- grinding
grinding
Machining operation in which material is removed from the workpiece by a powered abrasive wheel, stone, belt, paste, sheet, compound, slurry, etc. Takes various forms: surface grinding (creates flat and/or squared surfaces); cylindrical grinding (for external cylindrical and tapered shapes, fillets, undercuts, etc.); centerless grinding; chamfering; thread and form grinding; tool and cutter grinding; offhand grinding; lapping and polishing (grinding with extremely fine grits to create ultrasmooth surfaces); honing; and disc grinding.
- grit size
grit size
Specified size of the abrasive particles in grinding wheels and other abrasive tools. Determines metal-removal capability and quality of finish.
- surface grinding
surface grinding
Machining of a flat, angled or contoured surface by passing a workpiece beneath a grinding wheel in a plane parallel to the grinding wheel spindle. See grinding.