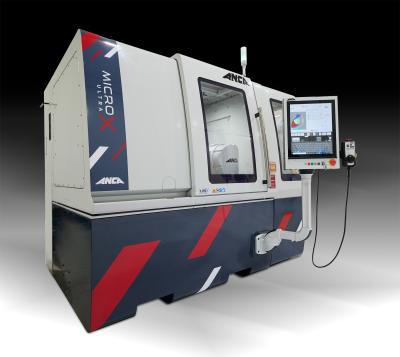
ANCA CNC Machines, a leading manufacturer of precision grinding machines, have launched the highly anticipated MicroX ULTRA.
This innovative six-axes grinding machine is meticulously designed for volume production of nano and micro cutting tools down to D0.03mm. Offering a superior solution for manufacturing high-quality, high-performance micro cutting tools, the MicroX ULTRA introduces groundbreaking technologies exclusive to the cutting tool industry.
The brain behind the machine is Pat McCluskey, a passionate machine tool designer, who is this year celebrating the 50th anniversary of ANCA, the company he co-founded with Pat Boland in 1974.
Pat McCluskey remarked, “I have been designing ANCA machines for 50 years – always with the goal of making machines better, more efficient, and user-friendly. It is a trademark of ANCA that you just have to do it differently, and the latest machine, the MicroX ULTRA, is the only micro tool grinder with nanometer resolution. This nano-level precision is a significant advancement in the field, utilizing the very best of ANCA's technology developed over five decades to offer superior micro tool production.”
Key features of the MicroX ULTRA:
- Nanometer resolution and nanometer control on all axes
With nanometer resolution and control over the tool grinding path, the MicroX ULTRA delivers a high level of surface and edge quality. This achievement is made possible through intelligent algorithms that operate collaboratively and in synchrony.
- Optimized axes travel to grind tools to micrometer sizes
The C-axis refers to the wheel swivel axis centerline, which is aligned with the wheel’s 9 o’clock grind point. This specific design is critical in the grinding of ballnose, corner radius and profile tools. In the case of a ballnose tool, the X and Y interpolations during the grinding process will be nearly equal to the radius of the ballnose tool.
- ANCA Machine Intelligence
Advanced algorithms ensure precise nanometer-level control of tool grinding paths, guaranteeing superior surface and edge quality. These algorithms collaborate and synchronize to reject disturbances swiftly, enhancing axis stiffness and robustness. They actively mitigate disturbances from spindle speed variations caused by imbalanced or runout grinding wheels. Encoder subdivision error compensation automatically detects and corrects inherent encoder errors on both linear and rotary encoders.
- In-process measurement in volume production
The LaserUltra takes process stability to an even higher level by closely controlling tolerances and incorporating in-process compensation mechanisms. This advanced system adapts to factors like wheel wear, resulting in superior precision and reliability.
- AIMS ready
Seamless integration with ANCA Integrated Manufacturing System (AIMS) facilitates effortless transition to automated, lights-out production, enhancing operational efficiency and productivity.
Contact Details
Related Glossary Terms
- computer numerical control ( CNC)
computer numerical control ( CNC)
Microprocessor-based controller dedicated to a machine tool that permits the creation or modification of parts. Programmed numerical control activates the machine’s servos and spindle drives and controls the various machining operations. See DNC, direct numerical control; NC, numerical control.
- grinding
grinding
Machining operation in which material is removed from the workpiece by a powered abrasive wheel, stone, belt, paste, sheet, compound, slurry, etc. Takes various forms: surface grinding (creates flat and/or squared surfaces); cylindrical grinding (for external cylindrical and tapered shapes, fillets, undercuts, etc.); centerless grinding; chamfering; thread and form grinding; tool and cutter grinding; offhand grinding; lapping and polishing (grinding with extremely fine grits to create ultrasmooth surfaces); honing; and disc grinding.
- grinding machine
grinding machine
Powers a grinding wheel or other abrasive tool for the purpose of removing metal and finishing workpieces to close tolerances. Provides smooth, square, parallel and accurate workpiece surfaces. When ultrasmooth surfaces and finishes on the order of microns are required, lapping and honing machines (precision grinders that run abrasives with extremely fine, uniform grits) are used. In its “finishing” role, the grinder is perhaps the most widely used machine tool. Various styles are available: bench and pedestal grinders for sharpening lathe bits and drills; surface grinders for producing square, parallel, smooth and accurate parts; cylindrical and centerless grinders; center-hole grinders; form grinders; facemill and endmill grinders; gear-cutting grinders; jig grinders; abrasive belt (backstand, swing-frame, belt-roll) grinders; tool and cutter grinders for sharpening and resharpening cutting tools; carbide grinders; hand-held die grinders; and abrasive cutoff saws.
- micrometer
micrometer
A precision instrument with a spindle moved by a finely threaded screw that is used for measuring thickness and short lengths.
- stiffness
stiffness
1. Ability of a material or part to resist elastic deflection. 2. The rate of stress with respect to strain; the greater the stress required to produce a given strain, the stiffer the material is said to be. See dynamic stiffness; static stiffness.