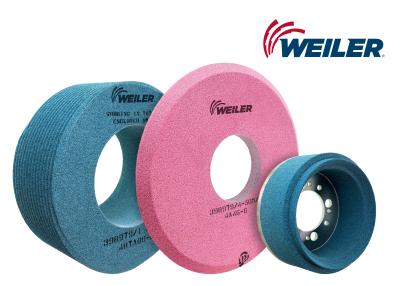
Weiler Abrasives, a leading provider of abrasives, power brushes and maintenance products for surface conditioning, has launched its new Precision Express program that cuts lead times for gear grinding wheels from months to days. The program is designed to help gear manufacturers in industries such as automotive, energy and aerospace improve quality, increase consistency and deliver on time to their customers — for added peace of mind.
“We know not having the right gear grinding wheel can lead to extensive lead times, quality issues and idle machines. Precision Express is our answer to the industry challenge of customers waiting months for a gear grinding wheel,” says Kyle Thompson, sector manager for Industrial Production Americas, Weiler Abrasives. “We prioritize on-time delivery of our precision gear grinding wheels so our customers no longer have to wait months for a grinding wheel, which could delay their operations.”
Precision Express matches an in-house profiling cell with a broad range of on-hand stock, cutting wheel manufacturing and delivery lead times from months to days. Even when gear manufacturers see a spike in demand or need a custom profile at a moment's notice, Weiler Abrasives can provide consistent availability and delivery.
In addition, Weiler Abrasives’ high performance gear grinding wheels feature industry-leading, proprietary V59 bond technology that ensures exceptional results and addresses customers’ unique needs with flexibility and precision. The advanced formulation of V59 bond technology provides superior grain retention, improving wheel life and grinding efficiency. Dynamic porosity lowers grinding temperatures through increased coolant efficiency and greatly reduces part surface damage from heat distortion while aiding in exceptional material removal rates — allowing for a reduction in grinding cycle times. The extended wheel life delivered with V59 bond technology also improves profile retention and reduces dressing frequency. The V59-MAX performance bond combines high-performance ceramic and aluminum oxide abrasive grains with superior V59 bond technology to deliver the maximum cut rate, longest wheel life and superior form holding ability.
With a sizable stock inventory of over 120 wheel blank sizes and specifications at Weiler Abrasives’ North American headquarters in Pennsylvania, custom wheels can be produced within two weeks. Available sizes range from as small as 6 inches up to 24 inches in diameter and from 1/2 inch to 9 and 1/2 inches thick. These are among the most common wheel styles and sizes used in the industry. The state-of-the-art Precision Express wheel profiling cell allows for wheel speed testing to ANSI B7.1 safety standards, which is 1.5 times the maximum operating speed labeled on the wheels, ensuring the ultimate safety of the product for the consumer. Elevating industry standards, Weiler’s premium manufacturing quality of precision grinding wheels feature tighter dimensional and imbalance tolerances, resulting in less vibration and very little dressing required when they are mounted on a customer’s machine.
The combination of industry-leading product technology, technical expertise and customer service makes Weiler Abrasives an ideal partner to help customers realize continuous improvement in gear grinding operations now and in the future.
Contact Details
Related Glossary Terms
- abrasive
abrasive
Substance used for grinding, honing, lapping, superfinishing and polishing. Examples include garnet, emery, corundum, silicon carbide, cubic boron nitride and diamond in various grit sizes.
- aluminum oxide
aluminum oxide
Aluminum oxide, also known as corundum, is used in grinding wheels. The chemical formula is Al2O3. Aluminum oxide is the base for ceramics, which are used in cutting tools for high-speed machining with light chip removal. Aluminum oxide is widely used as coating material applied to carbide substrates by chemical vapor deposition. Coated carbide inserts with Al2O3 layers withstand high cutting speeds, as well as abrasive and crater wear.
- coolant
coolant
Fluid that reduces temperature buildup at the tool/workpiece interface during machining. Normally takes the form of a liquid such as soluble or chemical mixtures (semisynthetic, synthetic) but can be pressurized air or other gas. Because of water’s ability to absorb great quantities of heat, it is widely used as a coolant and vehicle for various cutting compounds, with the water-to-compound ratio varying with the machining task. See cutting fluid; semisynthetic cutting fluid; soluble-oil cutting fluid; synthetic cutting fluid.
- dressing
dressing
Removal of undesirable materials from “loaded” grinding wheels using a single- or multi-point diamond or other tool. The process also exposes unused, sharp abrasive points. See loading; truing.
- grinding
grinding
Machining operation in which material is removed from the workpiece by a powered abrasive wheel, stone, belt, paste, sheet, compound, slurry, etc. Takes various forms: surface grinding (creates flat and/or squared surfaces); cylindrical grinding (for external cylindrical and tapered shapes, fillets, undercuts, etc.); centerless grinding; chamfering; thread and form grinding; tool and cutter grinding; offhand grinding; lapping and polishing (grinding with extremely fine grits to create ultrasmooth surfaces); honing; and disc grinding.
- grinding wheel
grinding wheel
Wheel formed from abrasive material mixed in a suitable matrix. Takes a variety of shapes but falls into two basic categories: one that cuts on its periphery, as in reciprocating grinding, and one that cuts on its side or face, as in tool and cutter grinding.
- profiling
profiling
Machining vertical edges of workpieces having irregular contours; normally performed with an endmill in a vertical spindle on a milling machine or with a profiler, following a pattern. See mill, milling machine.