There are sensations and experiences that must be experienced before they can be appreciated. Believe it or not, machining can provide sensations that only a machinist can truly understand.
For me it is the trepidation that I feel when a tap is about to enter the hole in hard-to-machine materials like nickel alloys. While I have never bungee jumped, I think tapping in difficult materials is probably similar. The tap going in the hole is like taking the first step, you have to push through the fear and let yourself go. The second level of fear is during the fall, hoping the rope will hold and the tap will get to the bottom. And third is the exhilaration of having survived the fall and the tap coming back out of the hole in one piece.
To reduce the anxiety of tapping holes in difficult materials I have developed my own rules of thumb. These are the things I do to give myself the best chance of success and minimize the fear of jumping.
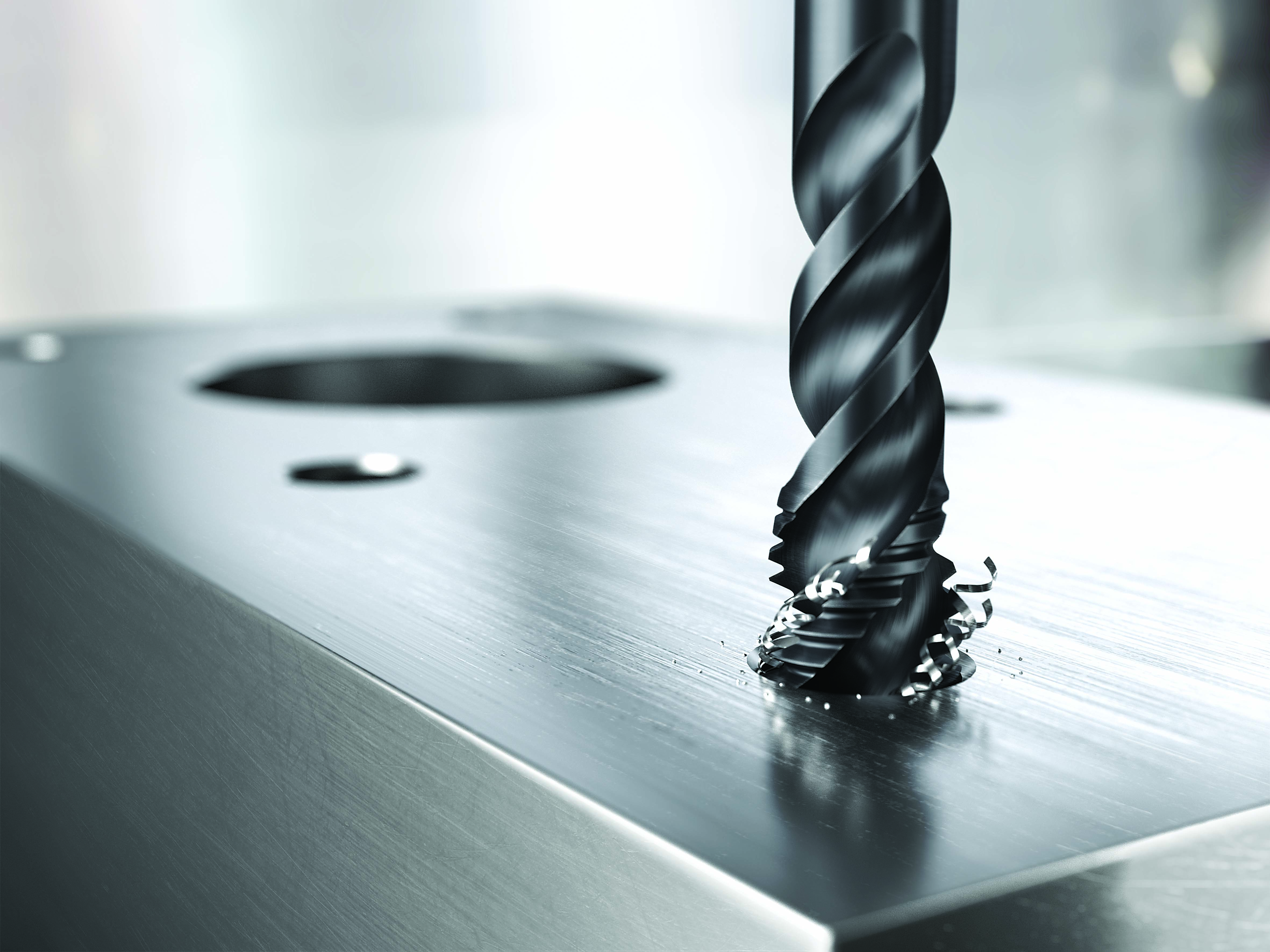
Rule Number One
Get a good tap. You can use almost any kind of tap to thread holes in aluminum, brass, plastics and most soft steels
with little worry of the tap breaking. That’s not the case with stainless steels or high nickel alloys like those used in aerospace applications. If the material is difficult to mill and drill, then tapping it can create nightmare scenarios. Getting a tap with geometry created for the material being machined is paramount to successful tapping of difficult materials. Having the correct geometry for exotic alloy materials will exponentially improve your chances of success.
Rule Number Two
Drill the correct size hole. Sounds like a no-brainer, right? Find the tap drill size on the chart and drill a hole, then tap it. That works fine — until it doesn’t. I suggest you drill the biggest hole you can get away with and still conform to the engineering requirements. It’s simple, a bigger hole creates less stress on the tap, which reduces risk. I will make the tapped hole as large as I can, even resorting to reaming holes when a drill is not available in the size I want.
Rule Number Three
Drill it deep. Through-holes or holes that go all the way through the material are the least risky when tapping because chips are less of a problem. Blind holes, holes that have a bottom, should be drilled as deep as possible and tapped as shallow as possible. This approach creates the maximum amount of clearance between the bottom of the hole and the end of the tap.
Rule Number Four
Lube it up! Tapping dry will cause problems in the easy materials like aluminum. So, tapping materials like stainless without proper lubricant is obviously more difficult. Oils and petroleum-based lubricants are always the best when they can be used. Unfortunately, using oils for production machining in 2024 is not ideal, so we must rely on water-based cutting fluids. Make sure your coolant is mixed correctly and it is not too lean. Coolants not only absorb heat, they lubricate the tool and the part. Most importantly, coolants reduce build up on the edge that would otherwise result in a broken tap. If you are having trouble with taps breaking or tearing threads, then make the coolant richer — 1% to 2% can work miracles.
Also, make sure coolant is getting to the tap. Position the nozzle so that the stream of coolant is going into the hole; sometimes a dedicated nozzle for the tap is needed to ensure the tool is never starved. Through the spindle coolant should also be used if available. Although I haven’t used one yet, I suspect through-coolant taps are effective. If I were making a new machining process for stainless or Hastelloy, I would plan to use through-coolant taps to ensure proper fluid delivery.
Rule Number Five
Use the right toolholder. It is always best to use a toolholder made for tapping. A tap holder allows the tool to move or float, minimizing the stresses and strains that can occur when the tap and machine are not perfectly synchronized. Modern machine tools are far less likely than their predecessors to suffer from these errors, but programmers occasionally make mistakes that a tap holder might correct. One of my previous employers tapped thousands of holes with the wrong pitch programmed, but the tap holder absorbed the error preventing breakage.
Rule Number Six
Tap holes as soon as possible. Taps are more prone to failure than any other tool, and broken taps rarely come out of the hole without additional work. Many times, it results in a scrapped part. By tapping early, you reduce the cost of scrap parts because fewer operations have been completed when the tap goes into the hole.
Rule Number Seven
Don’t use a tap. Thread milling is the best choice whenever possible. Avoid the use of taps at every opportunity. Thread milling is the most accurate way to produce threads in general machining. It is also the least risky as a broken thread mill will be easy to pick out of the hole unlike a broken tap, which is usually only removed after extra work and voluminous profanity. The accuracy and flexibility of modern machine tools makes thread milling easy, and it should be the first choice for threading difficult materials. Some manufacturers are making thread mills that also drill, allowing the user to consolidate machining operations and reduce cycle times.
These tricks do not remove the risk associated with tapping, but they will improve your success rate and may ease some of the anxiety of threading difficult materials.
.
Related Glossary Terms
- alloys
alloys
Substances having metallic properties and being composed of two or more chemical elements of which at least one is a metal.
- clearance
clearance
Space provided behind a tool’s land or relief to prevent rubbing and subsequent premature deterioration of the tool. See land; relief.
- coolant
coolant
Fluid that reduces temperature buildup at the tool/workpiece interface during machining. Normally takes the form of a liquid such as soluble or chemical mixtures (semisynthetic, synthetic) but can be pressurized air or other gas. Because of water’s ability to absorb great quantities of heat, it is widely used as a coolant and vehicle for various cutting compounds, with the water-to-compound ratio varying with the machining task. See cutting fluid; semisynthetic cutting fluid; soluble-oil cutting fluid; synthetic cutting fluid.
- gang cutting ( milling)
gang cutting ( milling)
Machining with several cutters mounted on a single arbor, generally for simultaneous cutting.
- milling
milling
Machining operation in which metal or other material is removed by applying power to a rotating cutter. In vertical milling, the cutting tool is mounted vertically on the spindle. In horizontal milling, the cutting tool is mounted horizontally, either directly on the spindle or on an arbor. Horizontal milling is further broken down into conventional milling, where the cutter rotates opposite the direction of feed, or “up” into the workpiece; and climb milling, where the cutter rotates in the direction of feed, or “down” into the workpiece. Milling operations include plane or surface milling, endmilling, facemilling, angle milling, form milling and profiling.
- milling machine ( mill)
milling machine ( mill)
Runs endmills and arbor-mounted milling cutters. Features include a head with a spindle that drives the cutters; a column, knee and table that provide motion in the three Cartesian axes; and a base that supports the components and houses the cutting-fluid pump and reservoir. The work is mounted on the table and fed into the rotating cutter or endmill to accomplish the milling steps; vertical milling machines also feed endmills into the work by means of a spindle-mounted quill. Models range from small manual machines to big bed-type and duplex mills. All take one of three basic forms: vertical, horizontal or convertible horizontal/vertical. Vertical machines may be knee-type (the table is mounted on a knee that can be elevated) or bed-type (the table is securely supported and only moves horizontally). In general, horizontal machines are bigger and more powerful, while vertical machines are lighter but more versatile and easier to set up and operate.
- pitch
pitch
1. On a saw blade, the number of teeth per inch. 2. In threading, the number of threads per inch.
- stainless steels
stainless steels
Stainless steels possess high strength, heat resistance, excellent workability and erosion resistance. Four general classes have been developed to cover a range of mechanical and physical properties for particular applications. The four classes are: the austenitic types of the chromium-nickel-manganese 200 series and the chromium-nickel 300 series; the martensitic types of the chromium, hardenable 400 series; the chromium, nonhardenable 400-series ferritic types; and the precipitation-hardening type of chromium-nickel alloys with additional elements that are hardenable by solution treating and aging.
- tap
tap
Cylindrical tool that cuts internal threads and has flutes to remove chips and carry tapping fluid to the point of cut. Normally used on a drill press or tapping machine but also may be operated manually. See tapping.
- tapping
tapping
Machining operation in which a tap, with teeth on its periphery, cuts internal threads in a predrilled hole having a smaller diameter than the tap diameter. Threads are formed by a combined rotary and axial-relative motion between tap and workpiece. See tap.
- threading
threading
Process of both external (e.g., thread milling) and internal (e.g., tapping, thread milling) cutting, turning and rolling of threads into particular material. Standardized specifications are available to determine the desired results of the threading process. Numerous thread-series designations are written for specific applications. Threading often is performed on a lathe. Specifications such as thread height are critical in determining the strength of the threads. The material used is taken into consideration in determining the expected results of any particular application for that threaded piece. In external threading, a calculated depth is required as well as a particular angle to the cut. To perform internal threading, the exact diameter to bore the hole is critical before threading. The threads are distinguished from one another by the amount of tolerance and/or allowance that is specified. See turning.
- toolholder
toolholder
Secures a cutting tool during a machining operation. Basic types include block, cartridge, chuck, collet, fixed, modular, quick-change and rotating.