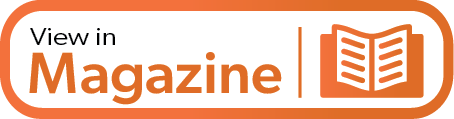
Michael Eneberg, vice president global sales and marketing for Sweden-based AB Sandvik Coromant, started his career at the Sandvik Group in Sandviken, Sweden, in 2003. He then went to work at Sandvik Tooling and Sandvik Coromant Japan, later becoming head of Sandvik Coromant Indonesia and managing director for Sandvik Indonesia. Prior to his most recent position as CEO for Diamond Tools Group, Eneberg was the general manager for Sandvik Coromant’s sales area South Asia, where he held responsibility for India, Japan and Southeast Asia. He was also managing director for Sandvik Japan during this time.
In an interview with CTE Editor-at-Large Alan Richter at IMTS 2024, Eneberg spoke about “sensorized” cutting tools, the habits that lead to manufacturing wellness, sustainability and the North American cutting tool market.
The conversation was edited for length, clarity and style guidelines.
Cutting Tool Engineering: What are the benefits of cutting tools with sensors?
Eneberg: We’ve always been trying to help our customers get more parts out the door, and sensorized tooling, which is now selling and moving fast, is a natural progression of our productivity message. An example is the internal boring bar. What that sensorized tool is doing is telling you inside a deep borehole, often in a difficult-to-machine material what’s going on with vibration, chip breaking and tool condition. That helps you to basically increase your feeds, but sometimes you dial back on the feed just to have secure machining. This information can give you the security to go a little bit more aggressive, especially in difficult-to-machine materials where usually you have low feeds and speeds. Now we talk about shaping the future together, very much in that direction.
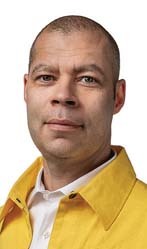
Cutting Tool Engineering: What does manufacturing wellness encompass?
Eneberg: What I really like about manufacturing wellness — a little bit similar to sensorized tooling — is it’s a natural progression of our productivity message. Manufacturing wellness is partially a summary of all the values we try to bring to the customer. Kind of their perfect state of being. We talk about many habits, take a holistic approach, embrace new technology, choose a sustainable path and eliminate waste. We have clearer messaging around it, a clear purpose around it. Then, of course, we have to choose a sustainable path. You have eliminated waste, which is an area where we are getting much clearer around. We talk about the different scopes of the Science Based Targets Initiative (SBT). Scope one is our own operation, and then we have scope two and scope three, which is downstream with the customer and upstream with the supplier for control and alignment on emissions. For us it’s an important part of our support activities. We also have this in the manufacturing wellness. We feel that we are well aligned with many major customers, especially in Europe. They have sustainability activity targets as a kind of supplier qualification because they are also trying to secure emissions upstream in their separation. It’s a nice mix of what we’ve been trying to do for quite some time.
Cutting Tool Engineering: What is Sandvik Coromant doing to enhance sustainability?
Eneberg: We’re looking at recycling solutions past the cemented carbide, e.g. the product packaging. Part of the technology is also material based. How do we produce new products from the beginning that are made with the purpose of being able to be broken down and recycled and made into new products? We’re in an ecosystem where everybody’s working hard to reduce their emissions. We took the productivity analyzer tool that we have had for quite some time and added some features, so we’ll have a sustainability analyzer. This was launched on the market earlier this year, and it will help customers to calculate how much emissions they can reduce by improving their machining methods. It doesn’t solve the whole footprint for them, usually because they have other processes as well. It’s a really big approach and contribution from our side.
Cutting Tool Engineering: How do North American cutting tool sales compare to other global regions?
Eneberg: We’ve seen North America growing faster than the global average ever since the pandemic. This year is no exception. North America is growing slightly better than the global average. Also, as a European with a lot of industry legacy, I always admire that North America comes up with new industries. North America was fundamental in bringing about the aerospace industry. Now, of course, we have European and Asian aerospace manufacturers. Then the U.S. has moved on to space in such quantities that the sector is becoming one of our fastest growing customers. It’s not just one. It’s a cluster of them. I think that’s enabling us to constantly outperform the average market within North America as long as we keep our customers here.
Cutting Tool Engineering: How does Sandvik Coromant continue to grow?
Eneberg: We’re (Sandvik Machining Solutions) buying at least one company per year in North America, and globally probably two to three a year. We also announced the acquisition of a Chinese company in the metalcutting space that should be part of the business area. I think that’s very important. Then, of course, there is the organic part, and the main reason we’re back at IMTS now in a booth is to promote something with engineering projects and probably the easiest way to understand that is what we call turnkey concepts, i.e. complete tool-up of new machines for a component. We see a lot of, especially in North America and aerospace related, new parts to be produced. Usually there’s a short time frame. The company that can make it first usually wins it because there might be several companies bidding for it, so time is an issue.
—Alan Richter
Related Glossary Terms
- boring
boring
Enlarging a hole that already has been drilled or cored. Generally, it is an operation of truing the previously drilled hole with a single-point, lathe-type tool. Boring is essentially internal turning, in that usually a single-point cutting tool forms the internal shape. Some tools are available with two cutting edges to balance cutting forces.
- boring bar
boring bar
Essentially a cantilever beam that holds one or more cutting tools in position during a boring operation. Can be held stationary and moved axially while the workpiece revolves around it, or revolved and moved axially while the workpiece is held stationary, or a combination of these actions. Installed on milling, drilling and boring machines, as well as lathes and machining centers.
- feed
feed
Rate of change of position of the tool as a whole, relative to the workpiece while cutting.
- metalcutting ( material cutting)
metalcutting ( material cutting)
Any machining process used to part metal or other material or give a workpiece a new configuration. Conventionally applies to machining operations in which a cutting tool mechanically removes material in the form of chips; applies to any process in which metal or material is removed to create new shapes. See metalforming.
- shaping
shaping
Using a shaper primarily to produce flat surfaces in horizontal, vertical or angular planes. It can also include the machining of curved surfaces, helixes, serrations and special work involving odd and irregular shapes. Often used for prototype or short-run manufacturing to eliminate the need for expensive special tooling or processes.