Automation and digitalization are critical to modern manufacturing. Manufacturers are looking to improve efficiency, reduce costs and enhance part quality. Also, finding and retaining skilled labor is an ongoing challenge for most manufacturers, job shops, and other metal working companies.
How do you solve these problems and make quality and efficiency improvements? One solution, says Doug Lieurance, application engineer for GROB Systems in Bluffton, Ohio, is to utilize fast, close tolerance, and flexible machine tools such as the GROB G550T 5-Axis Mill/ Turn Universal Machining Center that, he explained, is built for highly demanding manufacturing environs.
GROB machining centers, which are compatible with Industry 4.0 principles, are made in the U.S.A. at the GROB Systems full production facility in Ohio and often include advanced automation solutions for dramatically increased productivity. Having the machining center and automation come from the same builder offers customers streamlined service and support to keep the entire cell running at long-term high efficiency. GROB machines feature a unique machine concept including a horizontal spindle position that permits the longest possible Z-travel path and optimum chip fall.
At the recent International Manufacturing Technology Show (IMTS) in Chicago, Lieurance showed Cutting Tool Engineering magazine how the G550T machine handles complex parts. Machining demonstrations were held throughout the day, and not only did visitors to the booth learn about complex machining with 5-axis equipment, some were awarded a belt buckle machined live at the show.
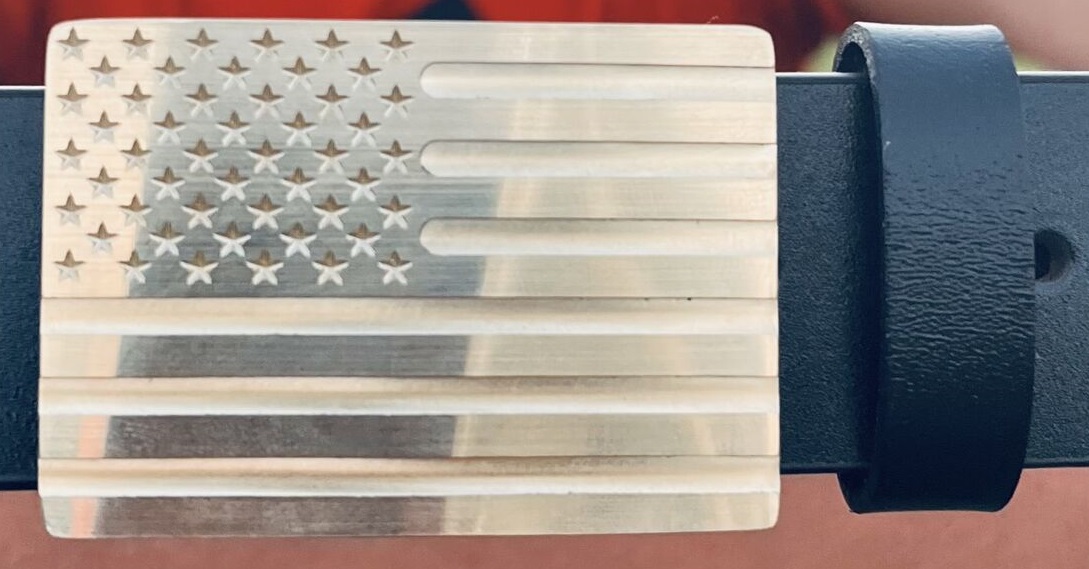
The G550T, he said, dramatically reduces downtime compared to previous 5-axis machines. It can be operated unattended, which saves on man-hours for manufacturing; and features unparalleled accuracy and consistency that has reduced the need for frequent accuracy measurements.
It can machine a part by milling and turning in a single setup, saving time, costs and floor space. The machine was equipped with a Siemens 840D SL control, 14,500 rpm spindle, and an HSK-T100 tool interface. For maximum stability and machining performance, the G550T featured a powerful mill-turn table with t-slots arranged in a star shape. Three linear and two rotary axes permitted 5-sided machining, as well as 5-axis simultaneous interpolation, with a swivel range of 230 degrees in the A-axis and 360 degrees in the B-axis. The drive design is based on two symmetrically located ball screws, weight compensation in the Y-axis, and wear-free torque motors in the A and B axes.
"Here, we are machining upside down so all the chips from the workpiece that we are cutting are falling right into the chip conveyor, so we have no build up on the pallet or anything like that," he said in describing the machining operation at the show. "Tool change happens completely outside of the work area, so we don't have to worry about the interference with the workpiece, the max size tool, max workpiece, zero collision, anything like that."
At the show, GROB was utilizing sophisticated programming from the Six Digma software development company, Lieurance said. "We connect CAD/CAM and CNC to solve the toughest manufacturing problems," said Edwin Gasparraj, Founder and Principal Consultant, SixDigma.
The demonstration at the Allied booth wasn't the only prominent booth at which GROB was displaying its products. At the YG-1 Tool Co. booth GROB showcased its G150 5-Axis Universal Machining Center integrated with the GRC-R12 Robot Cell, which were both under power. Multiple machining demonstrations were held throughout each day.
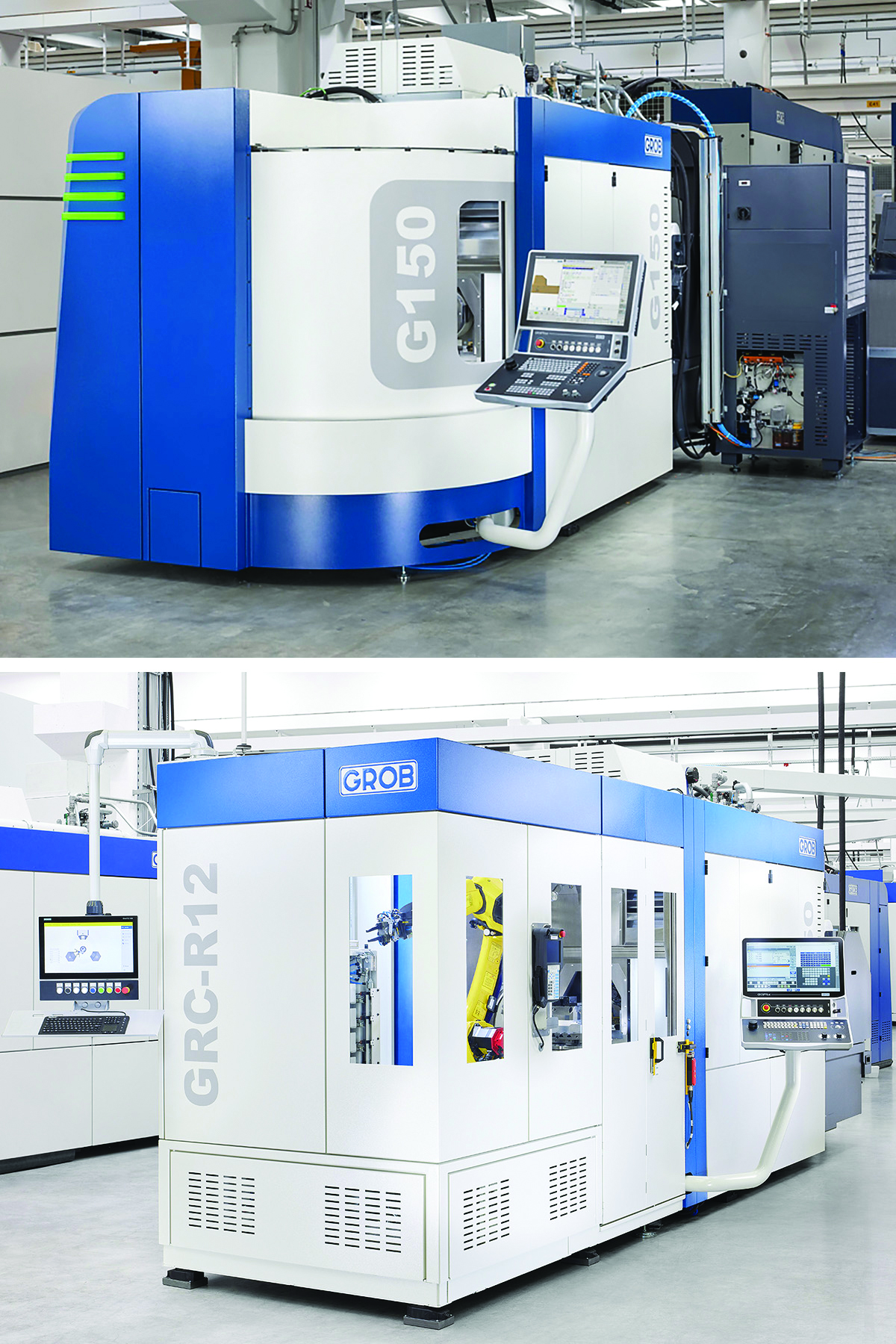
The G150 provides high precision, complex machining in a compact size with a smaller work envelope and features direct and absolute position encoders in all axes. Paired with the compact GRC-R12 Robot Cell, productivity was increased even further by offering a flexible, customizable, and affordable automation solution. The cell utilized a 6-Axis FANUC M-10iD/12 Robot with 4.7' (1,441 mm) reach, capable of handling a maximum load of 26.5 lbs (12 kg). The GRC-R12 featured a pneumatic single-or double-gripper system. The drawer feed system can hold up to six drawers that can be unloaded and reloaded while the robot cell and machining center are in operation.
Attendees also got to see demonstrations including an aerospace hydraulic manifold milled from 4140 steel supported by hyperMILL CAM programming from OPEN MIND Technologies.
Contact Details
Related Glossary Terms
- centers
centers
Cone-shaped pins that support a workpiece by one or two ends during machining. The centers fit into holes drilled in the workpiece ends. Centers that turn with the workpiece are called “live” centers; those that do not are called “dead” centers.
- computer numerical control ( CNC)
computer numerical control ( CNC)
Microprocessor-based controller dedicated to a machine tool that permits the creation or modification of parts. Programmed numerical control activates the machine’s servos and spindle drives and controls the various machining operations. See DNC, direct numerical control; NC, numerical control.
- computer-aided manufacturing ( CAM)
computer-aided manufacturing ( CAM)
Use of computers to control machining and manufacturing processes.
- feed
feed
Rate of change of position of the tool as a whole, relative to the workpiece while cutting.
- gang cutting ( milling)
gang cutting ( milling)
Machining with several cutters mounted on a single arbor, generally for simultaneous cutting.
- interpolation
interpolation
Process of generating a sufficient number of positioning commands for the servomotors driving the machine tool so the path of the tool closely approximates the ideal path. See CNC, computer numerical control; NC, numerical control.
- machining center
machining center
CNC machine tool capable of drilling, reaming, tapping, milling and boring. Normally comes with an automatic toolchanger. See automatic toolchanger.
- milling
milling
Machining operation in which metal or other material is removed by applying power to a rotating cutter. In vertical milling, the cutting tool is mounted vertically on the spindle. In horizontal milling, the cutting tool is mounted horizontally, either directly on the spindle or on an arbor. Horizontal milling is further broken down into conventional milling, where the cutter rotates opposite the direction of feed, or “up” into the workpiece; and climb milling, where the cutter rotates in the direction of feed, or “down” into the workpiece. Milling operations include plane or surface milling, endmilling, facemilling, angle milling, form milling and profiling.
- tolerance
tolerance
Minimum and maximum amount a workpiece dimension is allowed to vary from a set standard and still be acceptable.
- turning
turning
Workpiece is held in a chuck, mounted on a face plate or secured between centers and rotated while a cutting tool, normally a single-point tool, is fed into it along its periphery or across its end or face. Takes the form of straight turning (cutting along the periphery of the workpiece); taper turning (creating a taper); step turning (turning different-size diameters on the same work); chamfering (beveling an edge or shoulder); facing (cutting on an end); turning threads (usually external but can be internal); roughing (high-volume metal removal); and finishing (final light cuts). Performed on lathes, turning centers, chucking machines, automatic screw machines and similar machines.
- work envelope
work envelope
Cube, sphere, cylinder or other physical space within which the cutting tool is capable of reaching.