Contact Details
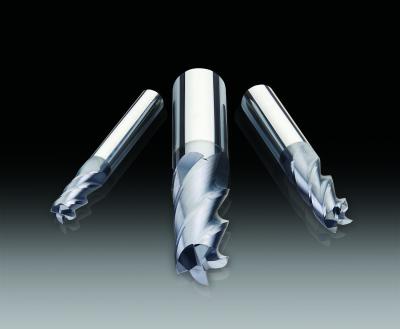
EMUGE-FRANKEN USA, a leading manufacturer of high-performance taps, thread mills, end mills, drills, and other rotary tools, has announced the introduction of a new line of 1:16 Tapered Solid Carbide End Mills designed to prepare a tapered core hole prior to finish tapping or thread milling NPT/ NPTF/ BSPT pipe threads. The new cutters feature an innovative design that reduces the number of tools required for hole preparation over a large range of pipe thread sizes, and they extend the tool life of expensive taps and thread mills.
“Uniquely designed with the proper 1:16 taper angle ground into the conical form for milling the minor diameter of taper pipe threads prior to tapping or thread milling, these new tools provide an enormous advantage over HSS taper reamers, offering substantial time and cost savings,” said Dylan Bowles, Applications Support Specialist at EMUGE-FRANKEN USA. “And these tools do not require a large or 5-Axis machine tool, as smaller 3-axis machines can handle larger threading applications.”
Only three EMUGE-FRANKEN Tapered tool sizes are required to handle a full range of hole sizes from 1/4" up to 4", instead of having to purchase an individual taper reamer for each pipe thread size. They also provide a highly efficient and secure method for optimizing thread milling strategies which incorporate the use of partial-profile insert technology.
EMUGE-FRANKEN 1:16 Tapered Carbide End Mills work well in a full range of materials from aluminum, carbon steels, stainless steels, and exotic nickel alloys. They are made of a premium micro-grain carbide substrate with TIALN-T21 coating which resists heat, edge wear and chipping. Corner radii further prevent wear or chipping while prolonging tool life. Tools are four-fluted, feature standard US length and straight inch shank (h6), and are available in three sizes: 3/8", 1/2" and 3/4".
Related Glossary Terms
- alloys
alloys
Substances having metallic properties and being composed of two or more chemical elements of which at least one is a metal.
- carbon steels
carbon steels
Known as unalloyed steels and plain carbon steels. Contains, in addition to iron and carbon, manganese, phosphorus and sulfur. Characterized as low carbon, medium carbon, high carbon and free machining.
- gang cutting ( milling)
gang cutting ( milling)
Machining with several cutters mounted on a single arbor, generally for simultaneous cutting.
- high-speed steels ( HSS)
high-speed steels ( HSS)
Available in two major types: tungsten high-speed steels (designated by letter T having tungsten as the principal alloying element) and molybdenum high-speed steels (designated by letter M having molybdenum as the principal alloying element). The type T high-speed steels containing cobalt have higher wear resistance and greater red (hot) hardness, withstanding cutting temperature up to 1,100º F (590º C). The type T steels are used to fabricate metalcutting tools (milling cutters, drills, reamers and taps), woodworking tools, various types of punches and dies, ball and roller bearings. The type M steels are used for cutting tools and various types of dies.
- milling
milling
Machining operation in which metal or other material is removed by applying power to a rotating cutter. In vertical milling, the cutting tool is mounted vertically on the spindle. In horizontal milling, the cutting tool is mounted horizontally, either directly on the spindle or on an arbor. Horizontal milling is further broken down into conventional milling, where the cutter rotates opposite the direction of feed, or “up” into the workpiece; and climb milling, where the cutter rotates in the direction of feed, or “down” into the workpiece. Milling operations include plane or surface milling, endmilling, facemilling, angle milling, form milling and profiling.
- reamer
reamer
Rotating cutting tool used to enlarge a drilled hole to size. Normally removes only a small amount of stock. The workpiece supports the multiple-edge cutting tool. Also for contouring an existing hole.
- shank
shank
Main body of a tool; the portion of a drill or similar end-held tool that fits into a collet, chuck or similar mounting device.
- stainless steels
stainless steels
Stainless steels possess high strength, heat resistance, excellent workability and erosion resistance. Four general classes have been developed to cover a range of mechanical and physical properties for particular applications. The four classes are: the austenitic types of the chromium-nickel-manganese 200 series and the chromium-nickel 300 series; the martensitic types of the chromium, hardenable 400 series; the chromium, nonhardenable 400-series ferritic types; and the precipitation-hardening type of chromium-nickel alloys with additional elements that are hardenable by solution treating and aging.
- taper reamer
taper reamer
Reamer designed to produce a reamed hole with a specified taper. Principles of standard reamers apply. See reamer.
- tapping
tapping
Machining operation in which a tap, with teeth on its periphery, cuts internal threads in a predrilled hole having a smaller diameter than the tap diameter. Threads are formed by a combined rotary and axial-relative motion between tap and workpiece. See tap.
- threading
threading
Process of both external (e.g., thread milling) and internal (e.g., tapping, thread milling) cutting, turning and rolling of threads into particular material. Standardized specifications are available to determine the desired results of the threading process. Numerous thread-series designations are written for specific applications. Threading often is performed on a lathe. Specifications such as thread height are critical in determining the strength of the threads. The material used is taken into consideration in determining the expected results of any particular application for that threaded piece. In external threading, a calculated depth is required as well as a particular angle to the cut. To perform internal threading, the exact diameter to bore the hole is critical before threading. The threads are distinguished from one another by the amount of tolerance and/or allowance that is specified. See turning.