Contact Details
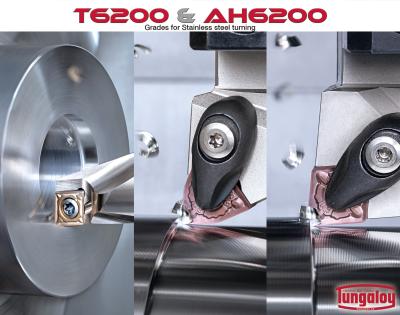
Tungaloy has announced the addition of 348 new inserts to its stainless steel turning grade series of AH6225, AH6235, and T6215. The addition will further enhance these proven insert grade series to guarantee stable machining performance across all stainless steel operations.
AH6225 is a first-choice grade designed to provide excellent machining performance in general stainless steel turning operations, extending from continuous to light interrupted cuts. A thick titanium-rich PVD coating with high thermal stability, combined with a dedicated carbide substrate that ensures better resistance to both fracture and plastic deformation, provides long and predictable tool life.
AH6235 is another PVD-coated grade that boasts exceptional fracture resistance. The grade provides outstanding reliability during interrupted cuts and heavy-duty turning applications with great depth of cut. Its thick thermally-stable coating provides superior cutting performance even when machining materials with poor machinability.
T6215 is a latest CVD-coated grade, designed to ensure superior cutting performance during high speed, continuous cuts of stainless steel. Incorporating a thickness of 1.3 times as thick as existing grades and extremely hard outer layer, the CVD coating offers extraordinary resistance to wear during high speed machining.
Related Glossary Terms
- chemical vapor deposition ( CVD)
chemical vapor deposition ( CVD)
High-temperature (1,000° C or higher), atmosphere-controlled process in which a chemical reaction is induced for the purpose of depositing a coating 2µm to 12µm thick on a tool’s surface. See coated tools; PVD, physical vapor deposition.
- depth of cut
depth of cut
Distance between the bottom of the cut and the uncut surface of the workpiece, measured in a direction at right angles to the machined surface of the workpiece.
- machinability
machinability
The relative ease of machining metals and alloys.
- physical vapor deposition ( PVD)
physical vapor deposition ( PVD)
Tool-coating process performed at low temperature (500° C), compared to chemical vapor deposition (1,000° C). Employs electric field to generate necessary heat for depositing coating on a tool’s surface. See CVD, chemical vapor deposition.
- plastic deformation
plastic deformation
Permanent (inelastic) distortion of metals under applied stresses that strain the material beyond its elastic limit.
- turning
turning
Workpiece is held in a chuck, mounted on a face plate or secured between centers and rotated while a cutting tool, normally a single-point tool, is fed into it along its periphery or across its end or face. Takes the form of straight turning (cutting along the periphery of the workpiece); taper turning (creating a taper); step turning (turning different-size diameters on the same work); chamfering (beveling an edge or shoulder); facing (cutting on an end); turning threads (usually external but can be internal); roughing (high-volume metal removal); and finishing (final light cuts). Performed on lathes, turning centers, chucking machines, automatic screw machines and similar machines.