Contact Details
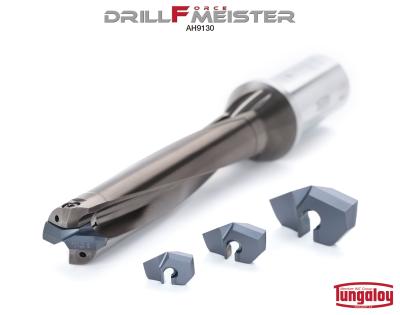
Tungaloy has added AH9130 insert grade to its DrillForce-Meister line of exchangeable-head drills designed for hole diameters ranging from 20.0 mm to 41.0 mm (.787″ to 1.614″).
AH9130, consisting of a PVD coating layer optimized for drilling applications with a dedicated carbide substrate, is the latest insert grade specifically developed to provide significant tool life improvements and more predictable wear patterns in hole making applications of ISO P (steel), ISO M (stainless steel), and ISO K (cast iron). 17 SMP-style inserts have been released in the latest grade, covering diameters from 20.0 mm to 35.0 mm (.787″ to 1.378″). In addition to Tungaloy’s versatile grade AH725 which covers most ISO materials, AH9130 provides DrillForce-Meister with added process security and tool life improvements in ISO P, M, and K applications.
DrillForce-Meister incorporates a unique exchangeable drill head designed to efficiently open large diameter holes ranging from 20.0 mm to 41.0 mm (.787″ to 1.614″) at a lower cost. The unique drill head features an asymmetric V bottom which is fully supported in a matching pocket of the drill body, providing accurate edge position repeatability and secure insert retention. Additionally, large contact surfaces of the drill head and pocket provides strong support helping the drill head to withstand heavy cutting loads in aggressive drilling operations. The drill body also features welldesigned flutes providing smooth chip control and evacuation in various materials.
DrillForce-Meister eliminates the need for regrinding and recoating, reducing the amount of tool float inventory kept to avoid machine downtime, thus minimizing the overall cost per hole in high volume production lines. A simple exchange of a new drill head guarantees the drill's dimensional stability and tool life predictability meeting the required finished dimensions of the workpiece.
Related Glossary Terms
- flutes
flutes
Grooves and spaces in the body of a tool that permit chip removal from, and cutting-fluid application to, the point of cut.
- physical vapor deposition ( PVD)
physical vapor deposition ( PVD)
Tool-coating process performed at low temperature (500° C), compared to chemical vapor deposition (1,000° C). Employs electric field to generate necessary heat for depositing coating on a tool’s surface. See CVD, chemical vapor deposition.