Contact Details
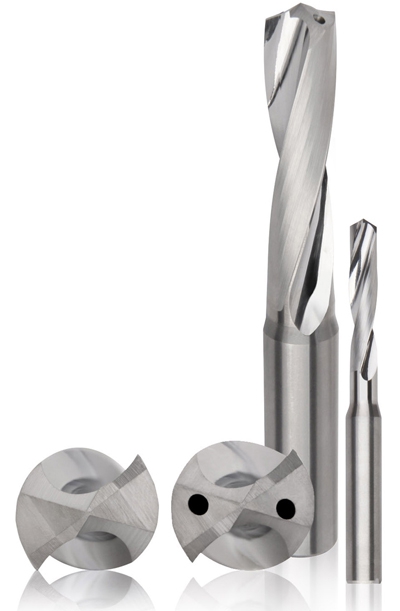
New stack drill from Kennametal for aerospace composite/titanium stacks can operate with through-coolant or without for superior chip evacuation. Kennametal is introducing its all-new B55_DAL Drill for drilling CFRP-metal stacks in hole diameter ranges of 3/16" to 5⁄8" (4.763mm to 15.875mm). The drill can be applied in all combinations of stacks: CFRP-Ti-Al as well as CFRP-Ti, CFRP-Al, and also straight Ti or Al. These drills can operate with standard through coolant, MQL, or even dry.
New materials are demanding new solutions. To maximize strength and minimize weight, the aerospace industry continues to research using stacks of composite fiber-reinforced polymers (CFRP) sandwiched between titanium or other materials. This provides essential performance at reduced weight for wings, fuselages, cockpits, and many other components. Due to the substantially different mechanical properties of carbon fibers and metals, drilling fastener holes efficiently challenges cutting tools by requiring high wear resistance and optimum tool geometries. Keeping holes high-quality and burr-free is critical.
The new B55_DAL drill's double-angle point design provides excellent centering capability and the sharp edge to cleanly cut CFRPs in the top layer of stacks and cleanly exit the titanium or aluminum side without burrs. The fine-grain solid-carbide Beyond KN15 grade is highly polished for superior chip evacuation even with MQL or dry operation.
A broad range of diameters and length variations are available to accommodate all holemaking operations, even those using robots or automated drilling units. In addition, the new stack drills can be reground to original process specifications, making these new tools even more cost-efficient.
Related Glossary Terms
- centering
centering
1. Process of locating the center of a workpiece to be mounted on centers. 2. Process of mounting the workpiece concentric to the machine spindle. See centers.
- coolant
coolant
Fluid that reduces temperature buildup at the tool/workpiece interface during machining. Normally takes the form of a liquid such as soluble or chemical mixtures (semisynthetic, synthetic) but can be pressurized air or other gas. Because of water’s ability to absorb great quantities of heat, it is widely used as a coolant and vehicle for various cutting compounds, with the water-to-compound ratio varying with the machining task. See cutting fluid; semisynthetic cutting fluid; soluble-oil cutting fluid; synthetic cutting fluid.
- mechanical properties
mechanical properties
Properties of a material that reveal its elastic and inelastic behavior when force is applied, thereby indicating its suitability for mechanical applications; for example, modulus of elasticity, tensile strength, elongation, hardness and fatigue limit.
- wear resistance
wear resistance
Ability of the tool to withstand stresses that cause it to wear during cutting; an attribute linked to alloy composition, base material, thermal conditions, type of tooling and operation and other variables.