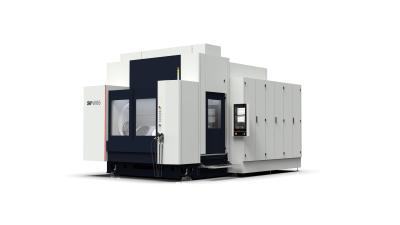
Schwäbische Werkzeugmaschinen GmbH (SW) is a global machine, automation and system solutions provider. Recently, the company released a new version of their BA W06 machining center. Optional enhancements fundamentally increase the power, speed and dynamic while improving user experience. The new version rollout was motivated by the desire to adapt the machine to better accommodate the needs of the e-mobility market.
The BA W06 was first introduced to the market over 15 years ago and quickly became known for its speed and reliability. With thousands of units installed globally, this 4- to 5- axis horizonal machining center continues to be one of SW’s most popular offerings on one specific issue. It is perfectly suited for the high-volume machining of large nonferrous components, such as aluminum gearbox housings and shock towers, for example. As is true for all SW machines, the BA W06 is highly customizable and each unit is as unique as the needs of the production into which it’s integrated. There new version is available with a wide range of new enhancements in dynamics, dimensioning, the drive and automation technologies and a new HMI.
Higher dynamic for higher productivity
As a linear motor machine, the BA W06 is one of SW’s fastest machines, which places it among the fastest machines worldwide. The rapid traverse can reach up to 120 m/min on the X-, Y- and Z-axes. The chip-to-chip time in the new version of the machine has been reduced by 10%. The BA W06 is built in SW’s signature Monoblock construction. This means that the machine is built like a cube and is therefore rigid and stable – enabling not only fast machining, but excellent repeat accuracy as well.
Expanded technical performance and Improved dimensional accuracy
The new version of the machine offers a more flexible and therefore more precise machining process. The BA W06 features variable spindle distance of 590.00 mm – 651.00 mm. Travel in the Y- and Z- axes 630 mm and 510 mm, respectively. The independent Z-axis enables machining coupled with compensation value. Fine adjustment of the spindle height is possible in the Y-axis with position correction. Straightness has been improved in the Z-axis due to increased guide ratio. There is also now higher positioning accuracy (Tp = 0.006 mm) in the in the X-, Y-, and Z-axes (verified by ISO 230-2) available.
Even under a range of production conditions, dimensional accuracy has been improved. The “jerk” in the G1 and G0 (the feed drives of the Y-axis) is an instrumental factor in positioning time for small traverse paths. High jerk values cause overshooting in positioning. Typically, the larger the machine, the greater the risk for high levels of jerk. In the BA W06, the jerk values are mapped to a maximum overshoot value of 0.004 mm in both the G1 and G0.
Product variants adapted for e-mobility
Previously, the machine was exclusively available with HSK 63 or HSK 80 spindles. Now, customers can choose to have their units fitted with HSK 100 spindles, which are larger and will accommodate larger tools (the tool belt can also now be affixed to the side of the machine; rather than the top). The dynamic of synchronous motor spindles compliments the tool magazine capable of holding especially large tools. This is useful, for example, in the machining of stator housing bores in drive units for electric vehicles.
The machine now supports more travel in the X- and Y-axes. Spindle distance can also be corrected in the X-axis. The Independent axes are also available with corrective capabilities. This results in a remarkable amount of flexibility and dynamic, rarely seen in the machining of such large components needed for e-mobility.
New drive and automation technologies
SW has implemented some new drive technology for improved positioning accuracy in the spindles, even with off-center loading. The linear-drive spindles feature direct positioning and a drive controller, which are electronically coupled on the control side.
Optimal positioning accuracy is ensured by two physically separated feed drives (Y1 and Y2), which each consist of a linear motor, a direct absolute position measuring system and a drive controller – electronically coupled on the control side. This is effective in guaranteeing positional accuracy, even with off-center loading.
The new BA W06 is available with a 99% increase in drive torque in the A-/U-axis for more dynamics or load. Permissible device weight has increased from 600 kg to 720 kg, which is a 20% increase. For especially big parts that usually require long cycle times and two spindles, the BA W06 only needs one table, which saves costs.
Gantry mounted automation above and in front of the machine in SW’s signature “Portal Solution” has optimal access to the machine. The BA W06 is available with up to 4 spindles; however, the updated drive and automation technologies included in the new version are best applied to the single and twin spindle variants with one to two tables.
Simplified user-experience with the new C|one Control Panel
Another option now available for implementation is the 24-inch SW C|one Control Panel. Haptic feedback on the multitouch screen will reduce errors due to dirt or contaminations on the screen. The C|one control panel offers operators a quicker, deeper insight into the machine performance data while offering an intuitive user-experience somewhat like a smartphone thanks to the multi-touch screen, which allows multiple points of simultaneous input. Used in conjunction with the SW CloudPlatform Services (which enable condition monitoring) it contributes to enhancing uptime and reducing maintenance costs.
Perhaps one of the most exciting aspects of the new C|one panel is the fact that alarms are traceable to the root cause. When, for example, a fuse is blown and numerous alarms are simultaneously triggered, operators won’t have to dig to know which issue to address first.
Additionally, the enhanced version features a portable tablet, docked at the tool loading station, replacing the optional secondary control panel. This tablet is a 10.1-inch and a multi-touch screen as well.
Security and Industry 4.0
The C|one also boasts simplified program management and the secure Windows 10 IO Enterprise operating system (which is commonly used for ATMs and point-of-sale devices). This new Control Panel is Industry 4.0 friendly and simplifies the digitization of productions while supporting traceability.
The new IO link will provide access to all process data, diagnostic data and device information. Users will also have access to machine-specific data such as: temperature, switching cycles, contamination and signal strength. This results in a reduction in downtime. It also helps support device replacement without the need to train personnel or add additional tools. This also mitigates incorrect settings.
EMC problems with analog signals are reduced, leading to a stronger interference immunity for the machine.
The bottom line:
Manufacturers across all industries are concerned with lowering their costs per part. SW is keenly aware of this and is continually developing solutions to accommodate this. Many in the automotive supply chain could be intimidated by machining large, thin-walled components as machining can be tricky and time-consuming resulting in lower profitability. Adaptable, fast machines like the BA W06 simplify these processes and allows manufacturers to take advantage of its speed and reliability for their own profit.
Adaptability will ultimately help ensure lasting, reliable success for manufacturers. The right variant for the customer is always determined by the needs of their production. SW works closely with their customers to ensure that their perfect solution will benefit them well into the future.
Contact Details
Related Glossary Terms
- feed
feed
Rate of change of position of the tool as a whole, relative to the workpiece while cutting.
- linear motor
linear motor
Functionally the same as a rotary motor in a machine tool, a linear motor can be thought of as a standard permanent-magnet, rotary-style motor slit axially to the center and then peeled back and laid flat. The major advantage of using a linear motor to drive the axis motion is that it eliminates the inefficiency and mechanical variance caused by the ballscrew assembly system used in most CNC machines.
- machining center
machining center
CNC machine tool capable of drilling, reaming, tapping, milling and boring. Normally comes with an automatic toolchanger. See automatic toolchanger.
- overshoot
overshoot
Deviation from nominal path caused by momentum carried over from previous step, as when a tool is rapidly traversed a considerable distance to begin a cut. Usually applies to CNC machining and is prevented if the control has the appropriate look-ahead capability. See look-ahead; undershoot.
- rapid traverse
rapid traverse
Movement on a CNC mill or lathe that is from point to point at full speed but, usually, without linear interpolation.