Contact Details
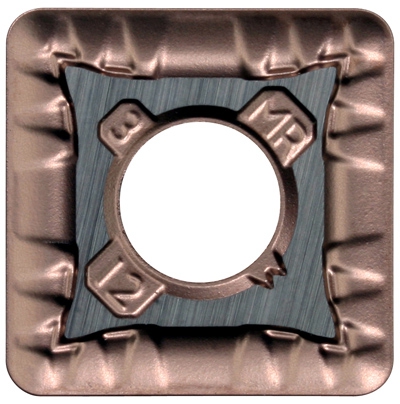
New Beyond MR (medium roughing) inserts from Kennametal a synergy of geometry and grade, with smooth cutting action and higher wear resistance among the results. Tools, it is said, are extensions of man's ability to work, therefore those that create tools extend the benefits of mankind. With 75-plus years of history making, creating, and further refining tools, Kennametal again adds to the ability of manufacturing customers around the world to further their productivity with the new Beyond Medium Roughing (MR) geometry for turning.
Turning more parts per shift or extending tool life is a common either-or tradeoff throughout the world's shop floors. Suitable for a wide range of workpiece materials, but ideal for stainless steels, Kennametal's new Beyond MR inserts are a product of ongoing design leadership, engineering, materials science, and manufacturing that delivers a perfect combination of smooth cutting action and stable edge performance. Faster cycle times and long tool life are the results.
"It's a synergy of geometry and grade that results in higher wear resistance and smoother chip flow," says Dr. Igor Kaufmann, senior manager, product engineering, RD&E at Kennametal. Double-sided indexable inserts commonly feature four cutting edges per side with cutting edges facing away from each other. A chip step consisting of an inlet region and an outlet region usually separates each cutting edge. While these chip steps help to control chip flow and cutting action, the commonly fluted design of incremental inlet and outlet regions tend to be an area of concentrated stresses during cutting, shortening tool life.
The uniqueness of Beyond MR is based in part on designing the geometry of the chip step in a continuous curve so that alternating stresses are reduced. The radius of curvature of the chip step surface is initially very large, becoming appreciably smaller, constituting the inlet region of the chip step, Kaufmann explains. From the lowest point of the chip step, the small radius of curvature grows larger, constituting the outlet region. As the surface of the chip step always has a curve, uniform chip forming occurs. Chips tend to deform continuously within the chip step, minimizing the friction of the chip on the tool face.
Rake angle, the incline of the top surface of the cutting edge that makes contact with the chip, also helps control the degree of cutting forces and cutting edge strength. The Beyond MR insert has a high positive rake angle that works with the smoothly curved cutting edge to reduce cutting forces and extend tool life. "In terms of chip flow, it's like nothing ever seen before," says Jan Andersson, senior product manager, turning products. Indexable double sided inserts, though, subject as they are to high cutting forces, are commonly seen as less stable. Beyond MR's rake profile without the points of load concentration results in an extremely stable insert body, despite the high positive rake. Even with high depth-of-cut applications, turning processes are safer and more stable, ensuring lower load on the machine tool and workpiece.
Additionally, Beyond MR inserts also feature formed-in coolant channels that deliver flood coolant efficiently to the cutting edge. Improved heat control translates into smoother cutting and extended tool life. "It's truly been a question for generations of shops, more parts per hour or more parts per tool," says Manuel Sedan, senior product manager, turning products at Kennametal. "Running faster may mean process problems with chip wrapping or longer setup times due to clearing chips from the machine. Plus the days of one man-one machine are long in the past. With one operator running a cell or any number of machines, greater predictability and performance with tools is an increasingly crucial component for success. Beyond MR is a truly exciting development that promises higher operating speeds, more pieces per shift, excellent chip control, and long tool life."
Beyond MR is available in six grades, covering a complete range of applications for turning stainless. Grades are also available for steels and cast irons as well.
Related Glossary Terms
- cast irons
cast irons
Cast ferrous alloys containing carbon in excess of solubility in austenite that exists in the alloy at the eutectic temperature. Cast irons include gray cast iron, white cast iron, malleable cast iron and ductile, or nodular, cast iron. The word “cast” is often left out.
- coolant
coolant
Fluid that reduces temperature buildup at the tool/workpiece interface during machining. Normally takes the form of a liquid such as soluble or chemical mixtures (semisynthetic, synthetic) but can be pressurized air or other gas. Because of water’s ability to absorb great quantities of heat, it is widely used as a coolant and vehicle for various cutting compounds, with the water-to-compound ratio varying with the machining task. See cutting fluid; semisynthetic cutting fluid; soluble-oil cutting fluid; synthetic cutting fluid.
- rake
rake
Angle of inclination between the face of the cutting tool and the workpiece. If the face of the tool lies in a plane through the axis of the workpiece, the tool is said to have a neutral, or zero, rake. If the inclination of the tool face makes the cutting edge more acute than when the rake angle is zero, the rake is positive. If the inclination of the tool face makes the cutting edge less acute or more blunt than when the rake angle is zero, the rake is negative.
- stainless steels
stainless steels
Stainless steels possess high strength, heat resistance, excellent workability and erosion resistance. Four general classes have been developed to cover a range of mechanical and physical properties for particular applications. The four classes are: the austenitic types of the chromium-nickel-manganese 200 series and the chromium-nickel 300 series; the martensitic types of the chromium, hardenable 400 series; the chromium, nonhardenable 400-series ferritic types; and the precipitation-hardening type of chromium-nickel alloys with additional elements that are hardenable by solution treating and aging.
- turning
turning
Workpiece is held in a chuck, mounted on a face plate or secured between centers and rotated while a cutting tool, normally a single-point tool, is fed into it along its periphery or across its end or face. Takes the form of straight turning (cutting along the periphery of the workpiece); taper turning (creating a taper); step turning (turning different-size diameters on the same work); chamfering (beveling an edge or shoulder); facing (cutting on an end); turning threads (usually external but can be internal); roughing (high-volume metal removal); and finishing (final light cuts). Performed on lathes, turning centers, chucking machines, automatic screw machines and similar machines.
- wear resistance
wear resistance
Ability of the tool to withstand stresses that cause it to wear during cutting; an attribute linked to alloy composition, base material, thermal conditions, type of tooling and operation and other variables.