Contact Details
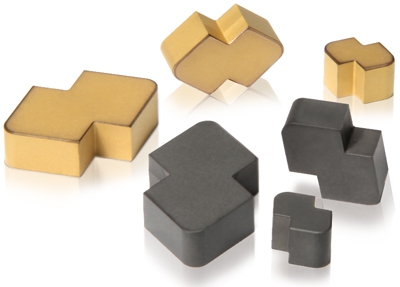
Advanced hard turning, or the use of superhard polycrystalline cubic boron nitride (PCBN) cutting tools for machining hardened ferrous materials like cast irons, is eagerly sought across a number of key manufacturing industries. Hundreds of millions of brakes discs, brake drums, flywheels, and wheel hubs are required annually in motor vehicle, heavy equipment, and other industries, and although superhard tools show promise for turning such tough-to-machine parts, that promise has been stalled due to the tendency of these expensive tools to shatter and break under the extreme forces required. With decades of experience in advanced materials science and tool design, Kennametal is announcing Beyond Shield as the solution (responding to modern challenges in machining cast iron machining) to this situation.
"For customers machining gray cast iron brake disks and brake drums, Kennametal's Beyond Shield PCBN inserts and clamping system provide up to 20 percent reduced tooling cost and up to 30 percent longer tool life compared to conventional systems," says Dr.-Ing. Raouf Ben Amor, senior global product manager. "Beyond Shield provides a robust clamping system that allows smaller IC PCBN inserts to perform well in the same applications as the larger IC insert, and by excellent matchup of wear and toughness in our grade properties proven in field tests."
High-performance cast-iron machining leads to extremely high mechanical and thermal loads. Conventional dimple-style clamps attempt to hold the cutting insert in place with direct point contact, which can break both clamp and insert under high pressure.
Beyond Shield has met the clamping challenge with a three-point clamp design that applies clamping force toward the front of the insert, closer to the cutting edge and significantly reducing vibrations that can lead to cracking and failure.
In addition, cast iron machining is a very aggressive environment where constant chip bombardment also cuts down clamp life. Beyond Shield provides a carbide-clad clamp through a unique Kennametal technology that improves clamp wear resistance from chip flow. Beyond Shield is also adaptable on standard toolholders, which can help control costs.
In addition to being tough by nature, cast irons present a number of machining challenges for cutting tools. Casting quality can be unpredictable. Low sulfur content can lead to tool life decreases by up to 60 percent, and increased ferrite content can lead to high chemical wear, also substantially decreasing tool life.
With a unique "multi-modal" PCBN structure, Kennametal's KBK35 grade has increased cubic boron nitride content that ensures increased wear resistance and longer insert life in both roughing and finishing operations. A chemical vapor deposition (CVD) coating protects against chemical wear resistance, and post-coat treatments improve cutting-edge toughness. "Field tests have shown double the tool life for KBK35 in aged and unaged cast iron, and in specific cases such as brake drums, up to 10 times (compared to ceramic-based solutions) the number of parts completed per insert."
For parts involving aged cast iron, Kennametal is also introducing grade KB1340 to the Beyond Shield family. In brake disk field tests versus standard PCBN inserts, KB1340 increased performance to 1,700 pieces versus 1,500 for the PCBN insert. In the same test versus ceramic inserts, tool life increases from 120 pieces to 4,200.
"For customers facing the need to increase cutting parameters and yet improve process reliability and control costs, Beyond Shield is the way to high-performance cast iron machining," Ben Amor says.
Related Glossary Terms
- cast irons
cast irons
Cast ferrous alloys containing carbon in excess of solubility in austenite that exists in the alloy at the eutectic temperature. Cast irons include gray cast iron, white cast iron, malleable cast iron and ductile, or nodular, cast iron. The word “cast” is often left out.
- chemical vapor deposition ( CVD)
chemical vapor deposition ( CVD)
High-temperature (1,000° C or higher), atmosphere-controlled process in which a chemical reaction is induced for the purpose of depositing a coating 2µm to 12µm thick on a tool’s surface. See coated tools; PVD, physical vapor deposition.
- cubic boron nitride ( CBN)
cubic boron nitride ( CBN)
Crystal manufactured from boron nitride under high pressure and temperature. Used to cut hard-to-machine ferrous and nickel-base materials up to 70 HRC. Second hardest material after diamond. See superabrasive tools.
- ferrite
ferrite
Solid solution of one or more elements in body-centered cubic iron. Unless otherwise designated, for instance, as chromium ferrite, the solute is generally assumed to be carbon. On an equilibrium diagram, there are two ferrite regions separated by an austenite area. The lower area is alpha ferrite and the upper area is delta ferrite. If there is no designation, alpha ferrite is assumed. Not more than 0.04 percent carbon can be dissolved in alpha iron. Ferrite is stable below 1,670º F (910º C); it is soft, highly ductile, and magnetic. Ferrite loses its magnetic property above 1,414º F (768º C).
- hard turning
hard turning
Single-point cutting of a workpiece that has a hardness value higher than 45 HRC.
- inscribed circle ( IC)
inscribed circle ( IC)
Imaginary circle that touches all sides of an insert. Used to establish size. Measurements are in fractions of an inch and describe the diameter of the circle.
- polycrystalline cubic boron nitride ( PCBN)
polycrystalline cubic boron nitride ( PCBN)
Cutting tool material consisting of polycrystalline cubic boron nitride with a metallic or ceramic binder. PCBN is available either as a tip brazed to a carbide insert carrier or as a solid insert. Primarily used for cutting hardened ferrous alloys.
- polycrystalline cubic boron nitride ( PCBN)2
polycrystalline cubic boron nitride ( PCBN)
Cutting tool material consisting of polycrystalline cubic boron nitride with a metallic or ceramic binder. PCBN is available either as a tip brazed to a carbide insert carrier or as a solid insert. Primarily used for cutting hardened ferrous alloys.
- turning
turning
Workpiece is held in a chuck, mounted on a face plate or secured between centers and rotated while a cutting tool, normally a single-point tool, is fed into it along its periphery or across its end or face. Takes the form of straight turning (cutting along the periphery of the workpiece); taper turning (creating a taper); step turning (turning different-size diameters on the same work); chamfering (beveling an edge or shoulder); facing (cutting on an end); turning threads (usually external but can be internal); roughing (high-volume metal removal); and finishing (final light cuts). Performed on lathes, turning centers, chucking machines, automatic screw machines and similar machines.
- wear resistance
wear resistance
Ability of the tool to withstand stresses that cause it to wear during cutting; an attribute linked to alloy composition, base material, thermal conditions, type of tooling and operation and other variables.
Additional Products from Kennametal Inc.
Pagination
- First page
- Previous page
- 1
- 2
- 3
- 4
- 5
- 6
- 7
- 8
- 9