Contact Details
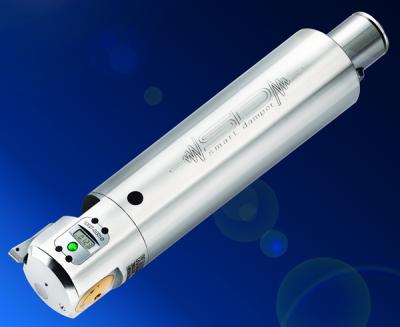
BIG Kaiser Precision Tooling Co., Hoffman Estates, Ill., recently introduced two new precision boring heads with a patented damping system to eliminate vibration in deep-hole finish boring, according to a company news release.
The integral design of the new EWN and EWD Smart Damper boring heads shortens the distance from the damping mechanism to the cutting edge, which is the source of vibration. This design produces higher damping effects to the tool assembly and minimizes the chatter or vibration, which results in better surface finishes and improved metal removal rates, according to BIG Kaiser.
“For precision machining of deep bores, it had previously been necessary to program low cutting parameters in order to prevent vibrations, which unnecessarily increases machining time,” said Jack Burley, BIG Kaiser’s vice president of sales and engineering. “The EWN/EWD Smart Damper overcomes this problem, and enables high cutting parameters to be used. This means that extremely short turnaround times can be achieved, which improves productivity by up to a factor of ten.”
BIG Kaiser tests reportedly have shown that deep holes free of vibration can be bored with an excellent surface finish, and with dramatic time savings. For example, with a projection length of 14.3” working with high-carbon steel at a cutting speed of 1,300 SFM, a feed rate of 11.4 IPM was achieved with the EWN41 Smart Damper.
The newest Smart Damper solution comes equipped with either the tried-and-true EWN analog boring head series or the latest digital technology in the EWD series. The EWN heads feature a dial with Ø.0005”/div setting accuracy (.0001” w/ Vernier). The EWD heads have a large digital screen, which clearly shows adjustments to an accuracy of Ø.00005”, thus helping to minimize operator errors and removing the need for complicated Vernier markings.
Related Glossary Terms
- boring
boring
Enlarging a hole that already has been drilled or cored. Generally, it is an operation of truing the previously drilled hole with a single-point, lathe-type tool. Boring is essentially internal turning, in that usually a single-point cutting tool forms the internal shape. Some tools are available with two cutting edges to balance cutting forces.
- boring head
boring head
Single- or multiple-point precision tool used to bring an existing hole within dimensional tolerance. The head attaches to a standard toolholder and a mechanism permits fine adjustments to be made to the head within a diameter range.
- chatter
chatter
Condition of vibration involving the machine, workpiece and cutting tool. Once this condition arises, it is often self-sustaining until the problem is corrected. Chatter can be identified when lines or grooves appear at regular intervals in the workpiece. These lines or grooves are caused by the teeth of the cutter as they vibrate in and out of the workpiece and their spacing depends on the frequency of vibration.
- cutting speed
cutting speed
Tangential velocity on the surface of the tool or workpiece at the cutting interface. The formula for cutting speed (sfm) is tool diameter 5 0.26 5 spindle speed (rpm). The formula for feed per tooth (fpt) is table feed (ipm)/number of flutes/spindle speed (rpm). The formula for spindle speed (rpm) is cutting speed (sfm) 5 3.82/tool diameter. The formula for table feed (ipm) is feed per tooth (ftp) 5 number of tool flutes 5 spindle speed (rpm).
- feed
feed
Rate of change of position of the tool as a whole, relative to the workpiece while cutting.
- inches per minute ( ipm)
inches per minute ( ipm)
Value that refers to how far the workpiece or cutter advances linearly in 1 minute, defined as: ipm = ipt 5 number of effective teeth 5 rpm. Also known as the table feed or machine feed.
- precision machining ( precision measurement)
precision machining ( precision measurement)
Machining and measuring to exacting standards. Four basic considerations are: dimensions, or geometrical characteristics such as lengths, angles and diameters of which the sizes are numerically specified; limits, or the maximum and minimum sizes permissible for a specified dimension; tolerances, or the total permissible variations in size; and allowances, or the prescribed differences in dimensions between mating parts.