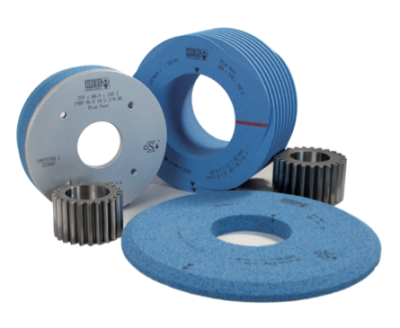
The Blue Moon TZ is an innovation developed by the R&D department of Krebs & Riedel. The Blue Moon TZ extends the Blue Moon product family. It is characterized by high cutting performance and high metal removal rates. The abrasive grain used in the Blue Moon TZ is very sharp-edged, microcrystalline and has an elongated trapezoidal rod shape. Blue Moon TZ grinding wheels are particularly impressive due to their very low thermal load in the contact zone. The high profile retention of our grit combination leads to extended dressing intervals at high stock removal rates and increases economic efficiency.
Your advantages at a glance
The advantages are particularly evident when processing long contact lengths. Typical applications include full cut grinding, raceway grinding and profile grinding of gears with large modules.
• Very low risk of overheating while grinding
• High removal rate
• Self-sharpening abrasive grain
• Short grinding times
• Reduced cost per unit
• Extended dressing intervals • Long tool life
Features
-
Individual specifications to your process by adjusting the grain concentration
-
Homogeneous, controllable pore space design
-
High friability during the dressing process
Applications
• Deep grinding
• Raceway grinding / Centerless grinding
• Applications with huge contact zones
• Gear grinding: Profile grinding for large modules
Industry sectors
- Aerospace
- Agricultural engineering
- Automotive
- Conveying technology
- Commercial vehicles
- Hydraulics
- Rolling bearings
- Wind energy
Contact Details
Related Glossary Terms
- abrasive
abrasive
Substance used for grinding, honing, lapping, superfinishing and polishing. Examples include garnet, emery, corundum, silicon carbide, cubic boron nitride and diamond in various grit sizes.
- centerless grinding
centerless grinding
Grinding operation in which the workpiece rests on a knife-edge support, rotates through contact with a regulating or feed wheel and is ground by a grinding wheel. This method allows grinding long, thin parts without steady rests; also lessens taper problems. Opposite of cylindrical grinding. See cylindrical grinding; grinding.
- dressing
dressing
Removal of undesirable materials from “loaded” grinding wheels using a single- or multi-point diamond or other tool. The process also exposes unused, sharp abrasive points. See loading; truing.
- friability
friability
Characteristic of abrasive grains that describes their tendency to fracture or break apart when hit or placed under pressure. Highly friable abrasives cut more easily, but wear faster than other abrasives. Friable abrasives are usually used on soft, gummy materials or where heat produced by worn grits must be carefully controlled. Friability is usually related to the levels of impurities in the manufactured abrasive mineral.
- grinding
grinding
Machining operation in which material is removed from the workpiece by a powered abrasive wheel, stone, belt, paste, sheet, compound, slurry, etc. Takes various forms: surface grinding (creates flat and/or squared surfaces); cylindrical grinding (for external cylindrical and tapered shapes, fillets, undercuts, etc.); centerless grinding; chamfering; thread and form grinding; tool and cutter grinding; offhand grinding; lapping and polishing (grinding with extremely fine grits to create ultrasmooth surfaces); honing; and disc grinding.