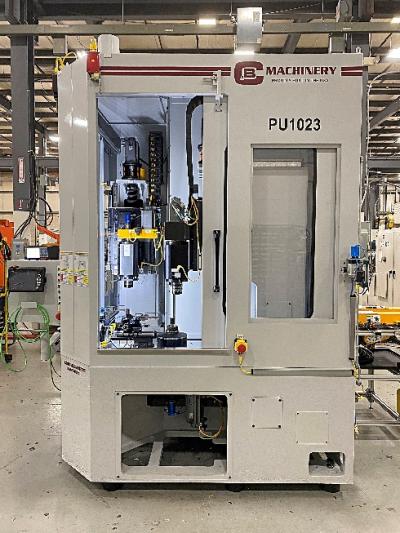
C&B Machinery (C&B) announced the completion of their newly redesigned Clamp Bore Face Grinding Machines. After months of planning, redesigning, and building the machines, C&B is excited to announce the latest CBVR-2F-2S model Clamp Bore Grinders.
Clamp bore face grinding machines are specifically designed for generating tighter squareness/perpendicularity tolerances for high-precision face grinding applications.
After numerous discussions, brainstorming sessions, and conversations with our customers, C&B embarked on the challenge of updating the design of their Clamp Bore Face Grinding Machine. The process took about a year with multiple redesigns throughout the process. Collaboration between Sales, Engineering, and Service Engineers helped achieve the final design.
When asked about redesigning the C&B Clamp Bore Face Grinding Machine, President of C&B Machinery, Bill Tulpa, said the following:
Listening to our customers was the main push for us, but we also listened to our Service Engineers. We consider our customers our partners. We want honest feedback from them. They live with our machinery every day. We asked them what improvements would help them the most with uptime, maintenance, and overall production. We took the feedback from our customers and our Service Engineers and made the necessary improvements. I don't think our newly designed Clamp Bore could have turned out better. It was truly a team effort!
Jeff Allen, Vice President of Operations, added: The idea of implementing a robot into the clamp bore grinding machine has been getting bounced around for years. We facilitated numerous brainstorming sessions and discussions. The kind of brainstorming where you wake up in the middle of the night with an idea. That was the excitement around this redesign.
We also put a lot of weight on specific customer feedback and requests based on existing customers using older model clamp bore face grinding machines. There were specific requests on what design changes they would like to see on the new model.
Standard clamp bore face grinding machine design included a gantry system that required a large number of parts. All of these parts were located within the interior of the machine, making servicing the machines difficult, as the space to work was very tight. The C&B Engineering Team worked to improve our work holding tooling and remove the gantry to achieve the desired upgrades. Allen provided details about the design:
The core components of the machine stayed the same. We repositioned the spindle columns to replace the gantry mechanism. This one change allowed for several previous components to be removed, making the machine more open and maintenance-friendly. The main change is that we have incorporated a Fanuc robot within the machine for the movement of parts.
The part handling area of the machine is simpler than in previous models. This is an area where many of our service calls occurred. The new design fixes the issue before it happens.
After testing multiple design concepts, the new design will be put into production in the very near future and multiple machines are being manufactured. This machine design allows users easier access to the spindles, gauges, and work holding than previous models. It also provides better coolant flow and minimizes areas for swarf buildup.
Contact Details
Related Glossary Terms
- coolant
coolant
Fluid that reduces temperature buildup at the tool/workpiece interface during machining. Normally takes the form of a liquid such as soluble or chemical mixtures (semisynthetic, synthetic) but can be pressurized air or other gas. Because of water’s ability to absorb great quantities of heat, it is widely used as a coolant and vehicle for various cutting compounds, with the water-to-compound ratio varying with the machining task. See cutting fluid; semisynthetic cutting fluid; soluble-oil cutting fluid; synthetic cutting fluid.
- grinding
grinding
Machining operation in which material is removed from the workpiece by a powered abrasive wheel, stone, belt, paste, sheet, compound, slurry, etc. Takes various forms: surface grinding (creates flat and/or squared surfaces); cylindrical grinding (for external cylindrical and tapered shapes, fillets, undercuts, etc.); centerless grinding; chamfering; thread and form grinding; tool and cutter grinding; offhand grinding; lapping and polishing (grinding with extremely fine grits to create ultrasmooth surfaces); honing; and disc grinding.
- grinding machine
grinding machine
Powers a grinding wheel or other abrasive tool for the purpose of removing metal and finishing workpieces to close tolerances. Provides smooth, square, parallel and accurate workpiece surfaces. When ultrasmooth surfaces and finishes on the order of microns are required, lapping and honing machines (precision grinders that run abrasives with extremely fine, uniform grits) are used. In its “finishing” role, the grinder is perhaps the most widely used machine tool. Various styles are available: bench and pedestal grinders for sharpening lathe bits and drills; surface grinders for producing square, parallel, smooth and accurate parts; cylindrical and centerless grinders; center-hole grinders; form grinders; facemill and endmill grinders; gear-cutting grinders; jig grinders; abrasive belt (backstand, swing-frame, belt-roll) grinders; tool and cutter grinders for sharpening and resharpening cutting tools; carbide grinders; hand-held die grinders; and abrasive cutoff saws.
- swarf
swarf
Metal fines and grinding wheel particles generated during grinding.