Contact Details
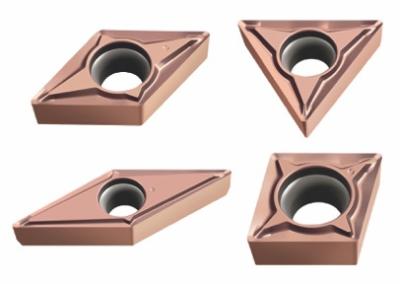
The new indexable turning inserts from Walter are designed for applications where a soft cut and high precision is required. This is achieved thru the FP2 geometry, which is a high positive (18°) rake angle geometry with soft hone that insures reduced cutting forces and vibration tendency. High tool life is achieved thru WEP10C coated cermet grade with multilayer TiCN TiAlN PVD coating and fine cermet micro grain. The combination of edge preparation and grade also ensures dimensional stability over long periods of time, which boosts productivity in mass production
The new FP2 geometry also uses “minus tolerance” or “maximum corner radius” tolerance. This allows for a stronger corner radius to be presented than a standard ISO/ANSI corner radius. For example, to machine a shoulder with 0.0157" corner radius, usually ANSI-0.5 corner radius (0.0078") is required. However, with the FP2 geometry, a 1M tolerance (equivalent of ANSI 0.0157" but 0.0146"+/-0.0008" tolerance corner radius) can be used. The advantage is that a much stronger corner radius boosts tool life and also surface finish to machine the same feature. These new inserts are well suited for finishing thin-walled components, components with small diameters, long components, and components with unstable clamping as well as fine boring applications.
Related Glossary Terms
- boring
boring
Enlarging a hole that already has been drilled or cored. Generally, it is an operation of truing the previously drilled hole with a single-point, lathe-type tool. Boring is essentially internal turning, in that usually a single-point cutting tool forms the internal shape. Some tools are available with two cutting edges to balance cutting forces.
- edge preparation
edge preparation
Conditioning of the cutting edge, such as a honing or chamfering, to make it stronger and less susceptible to chipping. A chamfer is a bevel on the tool’s cutting edge; the angle is measured from the cutting face downward and generally varies from 25° to 45°. Honing is the process of rounding or blunting the cutting edge with abrasives, either manually or mechanically.
- physical vapor deposition ( PVD)
physical vapor deposition ( PVD)
Tool-coating process performed at low temperature (500° C), compared to chemical vapor deposition (1,000° C). Employs electric field to generate necessary heat for depositing coating on a tool’s surface. See CVD, chemical vapor deposition.
- rake
rake
Angle of inclination between the face of the cutting tool and the workpiece. If the face of the tool lies in a plane through the axis of the workpiece, the tool is said to have a neutral, or zero, rake. If the inclination of the tool face makes the cutting edge more acute than when the rake angle is zero, the rake is positive. If the inclination of the tool face makes the cutting edge less acute or more blunt than when the rake angle is zero, the rake is negative.
- titanium aluminum nitride ( TiAlN)
titanium aluminum nitride ( TiAlN)
Often used as a tool coating. AlTiN indicates the aluminum content is greater than the titanium. See coated tools.
- titanium carbonitride ( TiCN)
titanium carbonitride ( TiCN)
Often used as a tool coating. See coated tools.
- tolerance
tolerance
Minimum and maximum amount a workpiece dimension is allowed to vary from a set standard and still be acceptable.
- turning
turning
Workpiece is held in a chuck, mounted on a face plate or secured between centers and rotated while a cutting tool, normally a single-point tool, is fed into it along its periphery or across its end or face. Takes the form of straight turning (cutting along the periphery of the workpiece); taper turning (creating a taper); step turning (turning different-size diameters on the same work); chamfering (beveling an edge or shoulder); facing (cutting on an end); turning threads (usually external but can be internal); roughing (high-volume metal removal); and finishing (final light cuts). Performed on lathes, turning centers, chucking machines, automatic screw machines and similar machines.