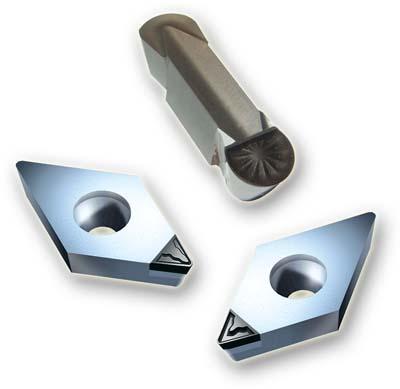
Lovejoy Tool Co. Inc. offers PCD chip control geometry inserts. The inserts break chips, increase production and improve employee safety by eliminating the removal of a nest of stringy chips when machining aluminum and copper alloys, according to the company. They are used in turning and boring, especially on screw machines. PCD Chip Control Geometry inserts are targeted to the customer that requires a chipbreaker at the actual cuttingpoint. Conventional flat face PCD inserts in continuous contact machining, like boring or turning, can experience hard to handle continuous chips, which can cause lost production time or result in poor surface finish. Lovejoy's chip control geometries put the chip control at the cutting point resulting in better control with a short chip. The inserts are offered in two chip breaker geometries: for finishing or general-purpose machining. The inserts reportedly produce less cutting pressures and heat expansion of the parts being machined, allowing a 20 to 30 percent increase in tool life and finer surface finishes.
Contact Details
Related Glossary Terms
- alloys
alloys
Substances having metallic properties and being composed of two or more chemical elements of which at least one is a metal.
- boring
boring
Enlarging a hole that already has been drilled or cored. Generally, it is an operation of truing the previously drilled hole with a single-point, lathe-type tool. Boring is essentially internal turning, in that usually a single-point cutting tool forms the internal shape. Some tools are available with two cutting edges to balance cutting forces.
- chipbreaker
chipbreaker
Groove or other tool geometry that breaks chips into small fragments as they come off the workpiece. Designed to prevent chips from becoming so long that they are difficult to control, catch in turning parts and cause safety problems.
- copper alloys
copper alloys
Copper containing specified quantities of alloying elements added to obtain the necessary mechanical and physical properties. The most common copper alloys are divided into six groups, and each group contains one of the following major alloying elements: brasses—major alloying element is zinc; phosphor bronzes—major alloying element is tin; aluminum bronzes—major alloying element is aluminum; silicon bronzes—major alloying element is silicon; copper-nickels and nickel-silvers—major alloying element is nickel; and dilute-copper or high-copper alloys, which contain small amounts of various elements such as beryllium, cadmium, chromium or iron.
- flat ( screw flat)
flat ( screw flat)
Flat surface machined into the shank of a cutting tool for enhanced holding of the tool.
- polycrystalline diamond ( PCD)
polycrystalline diamond ( PCD)
Cutting tool material consisting of natural or synthetic diamond crystals bonded together under high pressure at elevated temperatures. PCD is available as a tip brazed to a carbide insert carrier. Used for machining nonferrous alloys and nonmetallic materials at high cutting speeds.
- turning
turning
Workpiece is held in a chuck, mounted on a face plate or secured between centers and rotated while a cutting tool, normally a single-point tool, is fed into it along its periphery or across its end or face. Takes the form of straight turning (cutting along the periphery of the workpiece); taper turning (creating a taper); step turning (turning different-size diameters on the same work); chamfering (beveling an edge or shoulder); facing (cutting on an end); turning threads (usually external but can be internal); roughing (high-volume metal removal); and finishing (final light cuts). Performed on lathes, turning centers, chucking machines, automatic screw machines and similar machines.