Contact Details
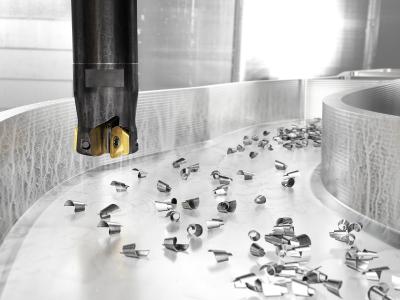
Leader in metal cutting, Sandvik Coromant has launched a new high-feed milling tool. The CoroMill® MH20 is primarily designed for milling cavities, or pockets, in ISO S, M and P materials. Ensuring secure and vibration-free machining, especially at long overhangs, the CoroMill® MH20 delivers best-in-class edge security for a variety of industries and is particularly suited for machining aerospace components.
The CoroMill® MH20 complements existing products in the CoroMill® range, and fills a strategic gap in the high feed indexable milling product line. Designed to deliver reliability with minimal vibration, the CoroMill® MH20 has been adapted for applications where components are notoriously difficult to machine, such as in the oil and gas, mold and die and aerospace sectors.
The tool’s ability to machine at long overhangs makes it especially beneficial to the aerospace sector. This method is an important requirement when machining deep, narrow pockets to produce the components that form an aircraft’s frame, such as its supporting beams found within the sub segment aerospace frame. These beams are often machined from forged titanium and when paired with the requirement for long overhangs, this creates a difficult machining environment with a high risk of vibration.
In contrast to the conventional four-edge concept, the CoroMill® MH20 is designed with a two-edge insert. This is especially beneficial as it means the weakest section of the insert is far away from the main cutting zone, delivering greater reliability and protection against wear. It also means that machining against a corner or wall will not impact the next edge or leading corner, ensuring an equal performance per edge.
Another area of innovation is the CoroMill® MH20’s insert cutting edge geometry. While the sloped edge design delivers a gradual and light-cutting action that requires less power consumption to enable the use of smaller machines, the optimized edge line of main cutting edge and insert corner radius delivers further process security and enables reliable, unmanned machining.
“Machining components for industries like aerospace, oil and gas and mold and die can be challenging,” said Sangram Dash, Application Manager at Sandvik Coromant. “In the aerospace sector alone, manufacturers must handle conditions such as thin floors and walls, deep pockets and tight corners. When designing the CoroMill® MH20, we kept the stringent requirements of all these sectors at the fore. For example, the tool is capable of completing several different operations to reduce the number of tools, changeovers and tool handling required during manufacturing, thus reducing cycle times and improving manufacturing economics. Furthermore, for the first time within high feed concepts, Sandvik Coromant is introducing dedicated insert geometries for different ISO areas to deliver greater optimized process security and productivity.
“In particular, engineers working in aerospace machining cannot afford to make mistakes, especially when the quality control standards for aircraft engine components are so high, so being able to deliver reliable tools with consistent tool life is a top priority for Sandvik Coromant.”
When designing the CoroMill® MH20, extending tool life with higher reliability was of great importance. In fact, when compared to another Sandvik Coromant high feed milling tool, CoroMill® 415, it demonstrated a 32% increase in tool life with a significantly better component quality when machining a titanium aerospace wing support component. In addition, further testing against competing tools has demonstrated superior reliability and a more secure machining performance when machining steel and stainless steel workpieces.
Related Glossary Terms
- feed
feed
Rate of change of position of the tool as a whole, relative to the workpiece while cutting.
- gang cutting ( milling)
gang cutting ( milling)
Machining with several cutters mounted on a single arbor, generally for simultaneous cutting.
- milling
milling
Machining operation in which metal or other material is removed by applying power to a rotating cutter. In vertical milling, the cutting tool is mounted vertically on the spindle. In horizontal milling, the cutting tool is mounted horizontally, either directly on the spindle or on an arbor. Horizontal milling is further broken down into conventional milling, where the cutter rotates opposite the direction of feed, or “up” into the workpiece; and climb milling, where the cutter rotates in the direction of feed, or “down” into the workpiece. Milling operations include plane or surface milling, endmilling, facemilling, angle milling, form milling and profiling.
- quality assurance ( quality control)
quality assurance ( quality control)
Terms denoting a formal program for monitoring product quality. The denotations are the same, but QC typically connotes a more traditional postmachining inspection system, while QA implies a more comprehensive approach, with emphasis on “total quality,” broad quality principles, statistical process control and other statistical methods.