Contact Details
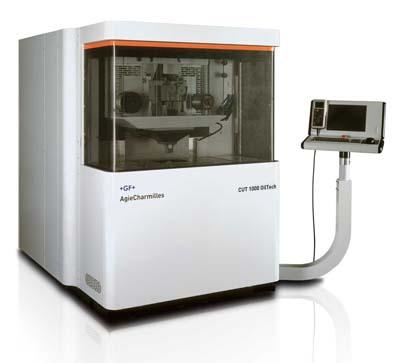
GF AgieCharmilles' new CUT 1000 OilTech wire EDM makes surface protection a priority. Designed specifically for micromachining and ultraprecision applications, the CUT 1000 OilTech uses wires as small as 0.02mm in diameter and SF technology to achieve surface finishes down to Ra 0.05µm in continuous operation. CUT 1000 OilTech uses oil as an inert dielectric. The oil eliminates the effects of corrosion due to long periods of immersion in the workpiece. As a result, multiple workpieces can remain immersed in the dielectric for overnight or weekend machining needs. The oil also enables smaller distances between the wire and workpiece to produce smaller internal radii when compared to water-based machining. Equipped with a high-performance generator and the AC Duo wire system, the machine is able to work with two wire spools, each with a different wire type, and switch between wires of different diameters automatically. Programmable via the machine control, the forward feed of the wires, just like the threading, takes place automatically and is monitored by patented sensors. GF AgieCharmilles constructed the CUT 1000 OilTech with a table design that separates the X and Y axes on a patented monobloc, eliminating mutual interference and tripping errors. A traveling table on the machine bed carries the work tank and moves the workpiece in the X direction exclusively. A second axis slide, also movable in the horizontal plane on the machine frame, accommodates the upper part of the C-frame and moves the wire in the Y direction. This configuration delivers ideal travels, positioning accuracy and taper cutting capability for machining complex, high precision parts. Cut 1000 OilTech accommodates workpieces up to 77 lbs. and has X-, Y- and Z-axis travels of 8.66"x6.29"x3.93". Additionally, CUT 1000 OilTech is equipped with Vision 5, an intuitive control system developed specifically for wire cut EDM that enables flexible data input in accordance with workshop environment.
Related Glossary Terms
- electrical-discharge machining ( EDM)
electrical-discharge machining ( EDM)
Process that vaporizes conductive materials by controlled application of pulsed electrical current that flows between a workpiece and electrode (tool) in a dielectric fluid. Permits machining shapes to tight accuracies without the internal stresses conventional machining often generates. Useful in diemaking.
- feed
feed
Rate of change of position of the tool as a whole, relative to the workpiece while cutting.
- threading
threading
Process of both external (e.g., thread milling) and internal (e.g., tapping, thread milling) cutting, turning and rolling of threads into particular material. Standardized specifications are available to determine the desired results of the threading process. Numerous thread-series designations are written for specific applications. Threading often is performed on a lathe. Specifications such as thread height are critical in determining the strength of the threads. The material used is taken into consideration in determining the expected results of any particular application for that threaded piece. In external threading, a calculated depth is required as well as a particular angle to the cut. To perform internal threading, the exact diameter to bore the hole is critical before threading. The threads are distinguished from one another by the amount of tolerance and/or allowance that is specified. See turning.
- wire EDM
wire EDM
Process similar to ram electrical-discharge machining except a small-diameter copper or brass wire is used as a traveling electrode. Usually used in conjunction with a CNC and only works when a part is to be cut completely through. A common analogy is wire electrical-discharge machining is like an ultraprecise, electrical, contour-sawing operation.
Additional Products from GF Machining Solutions
Pagination
- First page
- Previous page
- 1
- 2
- 3
- 4
- 5
- 6