Contact Details
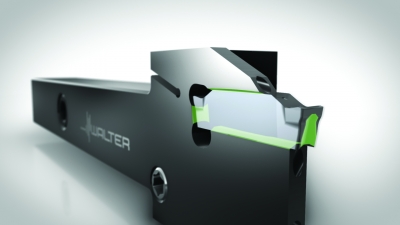
The Walter Cut DX18 double-edged grooving and parting off inserts with insert widths of 0.059-0.157 in. (1.5-4 mm) are the latest addition to Walter’s ever-expanding grooving product range. The patent pending cutting insert is seated in the insert pocket with a unique prismatic design.
This innovative insert seating substantially eliminates the tendency for vibrations, increasing insert life as well as tool holder life. The design also prevents incorrect engagement, especially for narrow insert widths, and enables an extremely high indexing accuracy. Elevated protective edge is an inbuilt feature of these DX18 carbide inserts that protects the clamping finger of the tool holder from chip-wash and acts as an additional chip breaker; further enhancing tool life and process reliability.
New DX18 geometries include the "C" cut off geometries CF6, CF5, and CE4 for cut off (parting off). The new "G" grooving geometries GD6, and GD3 for grooving. The "U" universal geometries UF4, UD4 and UA4 are for groove turning, parting off and grooving. The UD4 acts as a unique trouble shooter to achieve exceptional chip control. The new "R" full-radius geometries for copy turning and radius grooving include the sintered RF7.
The holders for these inserts are made for swiss style machines as well as conventional lathe and bar feeder machines. The holders are offered in both the signature precision-cooling thru-coolant configuration as well as external coolant configuration for economies. The G4014-P holders are uniquely designed for swiss machines, allowing inserts to be indexed while on the machine gang tooling, reducing insert indexing time by as much as 70%. The G4011 holders are offered for conventional lathes in both square shank and Capto style designs, while the G4041 blade style holders are ideal for parting off close to shoulders in a limited space.
Related Glossary Terms
- coolant
coolant
Fluid that reduces temperature buildup at the tool/workpiece interface during machining. Normally takes the form of a liquid such as soluble or chemical mixtures (semisynthetic, synthetic) but can be pressurized air or other gas. Because of water’s ability to absorb great quantities of heat, it is widely used as a coolant and vehicle for various cutting compounds, with the water-to-compound ratio varying with the machining task. See cutting fluid; semisynthetic cutting fluid; soluble-oil cutting fluid; synthetic cutting fluid.
- grooving
grooving
Machining grooves and shallow channels. Example: grooving ball-bearing raceways. Typically performed by tools that are capable of light cuts at high feed rates. Imparts high-quality finish.
- lathe
lathe
Turning machine capable of sawing, milling, grinding, gear-cutting, drilling, reaming, boring, threading, facing, chamfering, grooving, knurling, spinning, parting, necking, taper-cutting, and cam- and eccentric-cutting, as well as step- and straight-turning. Comes in a variety of forms, ranging from manual to semiautomatic to fully automatic, with major types being engine lathes, turning and contouring lathes, turret lathes and numerical-control lathes. The engine lathe consists of a headstock and spindle, tailstock, bed, carriage (complete with apron) and cross slides. Features include gear- (speed) and feed-selector levers, toolpost, compound rest, lead screw and reversing lead screw, threading dial and rapid-traverse lever. Special lathe types include through-the-spindle, camshaft and crankshaft, brake drum and rotor, spinning and gun-barrel machines. Toolroom and bench lathes are used for precision work; the former for tool-and-die work and similar tasks, the latter for small workpieces (instruments, watches), normally without a power feed. Models are typically designated according to their “swing,” or the largest-diameter workpiece that can be rotated; bed length, or the distance between centers; and horsepower generated. See turning machine.
- parting
parting
When used in lathe or screw-machine operations, this process separates a completed part from chuck-held or collet-fed stock by means of a very narrow, flat-end cutting, or parting, tool.
- shank
shank
Main body of a tool; the portion of a drill or similar end-held tool that fits into a collet, chuck or similar mounting device.
- turning
turning
Workpiece is held in a chuck, mounted on a face plate or secured between centers and rotated while a cutting tool, normally a single-point tool, is fed into it along its periphery or across its end or face. Takes the form of straight turning (cutting along the periphery of the workpiece); taper turning (creating a taper); step turning (turning different-size diameters on the same work); chamfering (beveling an edge or shoulder); facing (cutting on an end); turning threads (usually external but can be internal); roughing (high-volume metal removal); and finishing (final light cuts). Performed on lathes, turning centers, chucking machines, automatic screw machines and similar machines.