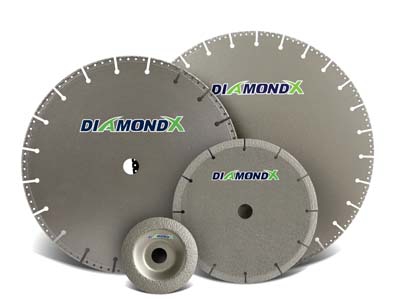
CGW-Camel Grinding Wheels has introduced a line of diamond wheels engineered for demanding metal applications.
Utilizing a high concentration of diamond grit, a solid steel body and an advanced brazing process, CGW's new diamond wheels are reportedly made to last at least 50 times longer than traditional, bonded abrasives. Longer-lasting life spans allow for increased production times and lower grinding and cutting cost ratios. The new diamond wheels also produce fewer sparks, no odor and less material debris since they do not wear down like traditional abrasives. Because the CGW diamond wheels are made from solid steel and will not fracture during use like resin bonded wheels, they are safer to use.
CGW's diamond wheel line consists of type 29 depressed center grinding wheels, type 1 notching/grinding wheels and 16 to 20 inch combination cutting wheels for chop saws, stationary saws, gas saws and rail cutting machines. The new depressed center grinding wheels are made to last 50 times longer than conventional abrasives and are ideal for weld removal, pipe beveling and stock removal on all ferrous and nonferrous metals. The notching/grinding wheels are engineered to last 50 times longer than conventional abrasives and are designed for foundry gate/riser removal, sectional tubing and hard face metal alloys. The new 16 to 20 inch combination cutting wheels will last 70 times longer than conventional abrasives and are used for rail track, ductile iron and carbon/mild steel applications.
"CGW's new diamond wheels are made from a process that is a technological breakthrough, which will provide great solutions for tough metal cutting and grinding jobs," said Joe O'Mera CGW-Camel Grinding Wheels president.
Contact Details
Related Glossary Terms
- alloys
alloys
Substances having metallic properties and being composed of two or more chemical elements of which at least one is a metal.
- grinding
grinding
Machining operation in which material is removed from the workpiece by a powered abrasive wheel, stone, belt, paste, sheet, compound, slurry, etc. Takes various forms: surface grinding (creates flat and/or squared surfaces); cylindrical grinding (for external cylindrical and tapered shapes, fillets, undercuts, etc.); centerless grinding; chamfering; thread and form grinding; tool and cutter grinding; offhand grinding; lapping and polishing (grinding with extremely fine grits to create ultrasmooth surfaces); honing; and disc grinding.