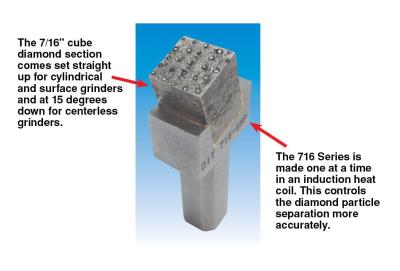
Many years ago, the Super 716 Series diamond tool was made for dressing large and wide precision grinding wheels on centerless, cylindrical and surface precision grinding machines. They were made to minimize glazing and the closing up of the wheel surface. They were also made to carry the large wheel without taper or the crushing of the bond. It worked better than any other grit or impregnated dressing tool.
Unlike any grit or impregnated dressing tool the Super 716 Series is made one at a time in an induction heat coil. This controls the diamond particle separation more accurately so they don’t flow or clump. The hot-pressed bond retains the diamond mesh more consistently for better dressing control.
The 7/16” cube diamond section comes set straight up for cylindrical and surface grinders and at 15 degrees down for centerless grinders.
It is available in different diamond mesh sizes for the many grinding wheel grit sizes. The new current generation uses blocky natural diamond mesh, which has gone through a new sorting process. This has shown additional new improvements for dressing ceramic abrasive grit wheels.
Contact Details
Related Glossary Terms
- abrasive
abrasive
Substance used for grinding, honing, lapping, superfinishing and polishing. Examples include garnet, emery, corundum, silicon carbide, cubic boron nitride and diamond in various grit sizes.
- dressing
dressing
Removal of undesirable materials from “loaded” grinding wheels using a single- or multi-point diamond or other tool. The process also exposes unused, sharp abrasive points. See loading; truing.
- grinding
grinding
Machining operation in which material is removed from the workpiece by a powered abrasive wheel, stone, belt, paste, sheet, compound, slurry, etc. Takes various forms: surface grinding (creates flat and/or squared surfaces); cylindrical grinding (for external cylindrical and tapered shapes, fillets, undercuts, etc.); centerless grinding; chamfering; thread and form grinding; tool and cutter grinding; offhand grinding; lapping and polishing (grinding with extremely fine grits to create ultrasmooth surfaces); honing; and disc grinding.
- grinding wheel
grinding wheel
Wheel formed from abrasive material mixed in a suitable matrix. Takes a variety of shapes but falls into two basic categories: one that cuts on its periphery, as in reciprocating grinding, and one that cuts on its side or face, as in tool and cutter grinding.