Contact Details
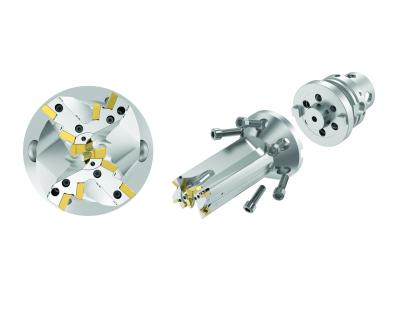
Kennametal has introduced the FBX drill for flat-bottom drilling of structural aerospace parts. The patented FBX drill delivers superior stability and up to 200 percent higher metal removal rates when machining high temperature alloys, stainless steel, and other materials. The new modular drill is the critical first step in a three-part tooling concept—including the HARVI™ Ultra 8X and the HARVI™ end mill series—specifically designed by Kennametal to decrease cycle time for these types of applications.
The FBX drill is part of a tooling concept specifically developed to maximize metal removal rates and decrease cycle times when machining aerospace structural components.
Quickly removing large amounts of material remains a challenge for these types of components. Traditionally, the first process step is to enter the material by using ramping techniques. This is a time-consuming process and low metal removal rates are the norm.
"The FBX drill dramatically speeds up the machining process by combining the advantages of a flat bottom drill and a z-axis plunge mill. The flat bottom design eliminates radial forces while four effective cutting edges provide increased feed and speed rates, leading to up to 200 percent higher metal removal rates than traditional ramping techniques and freeing up capacity for aerospace manufacturers," says Georg Roth, Product Manager, Kennametal.
Once the drill has shaped the basic structure of the component, roughing and finishing with indexable and solid end mills are the next process steps.
Unique Design Features
Four effective cutting edges provide stability in challenging applications like chain hole drilling, while large chip flutes ensure a hassle-free chip evacuation. Supported by a series of exchangeable coolant nozzles to help eliminate heat buildup, the drill point is characterized by a center insert with two effective cutting edges and chip splitters for maximum feed capabilities. The drill bodies are available in diameters 60, 75, and 90mm, and come in a long and short version (150mm and 95mm). This modular drill connects to Kennametal´s bolt taper flange (BTF) mount adapters, available in various spindle connection styles.
The unique design of the FBX flat bottom drill directs cutting forces into the machine spindle, minimizing deflection while increasing tool life and metal removal rates.
Versatility and Performance in One Tool
The FBX is ideally suited for drilling into solid, chain hole drilling and plunging in a variety of materials such as high temperature alloys, stainless steel, and steels and cast irons. It is equally as versatile and high performing in similar applications for the general engineering and power generation markets
Related Glossary Terms
- alloys
alloys
Substances having metallic properties and being composed of two or more chemical elements of which at least one is a metal.
- cast irons
cast irons
Cast ferrous alloys containing carbon in excess of solubility in austenite that exists in the alloy at the eutectic temperature. Cast irons include gray cast iron, white cast iron, malleable cast iron and ductile, or nodular, cast iron. The word “cast” is often left out.
- coolant
coolant
Fluid that reduces temperature buildup at the tool/workpiece interface during machining. Normally takes the form of a liquid such as soluble or chemical mixtures (semisynthetic, synthetic) but can be pressurized air or other gas. Because of water’s ability to absorb great quantities of heat, it is widely used as a coolant and vehicle for various cutting compounds, with the water-to-compound ratio varying with the machining task. See cutting fluid; semisynthetic cutting fluid; soluble-oil cutting fluid; synthetic cutting fluid.
- feed
feed
Rate of change of position of the tool as a whole, relative to the workpiece while cutting.
- flat ( screw flat)
flat ( screw flat)
Flat surface machined into the shank of a cutting tool for enhanced holding of the tool.
- flutes
flutes
Grooves and spaces in the body of a tool that permit chip removal from, and cutting-fluid application to, the point of cut.
- milling machine ( mill)
milling machine ( mill)
Runs endmills and arbor-mounted milling cutters. Features include a head with a spindle that drives the cutters; a column, knee and table that provide motion in the three Cartesian axes; and a base that supports the components and houses the cutting-fluid pump and reservoir. The work is mounted on the table and fed into the rotating cutter or endmill to accomplish the milling steps; vertical milling machines also feed endmills into the work by means of a spindle-mounted quill. Models range from small manual machines to big bed-type and duplex mills. All take one of three basic forms: vertical, horizontal or convertible horizontal/vertical. Vertical machines may be knee-type (the table is mounted on a knee that can be elevated) or bed-type (the table is securely supported and only moves horizontally). In general, horizontal machines are bigger and more powerful, while vertical machines are lighter but more versatile and easier to set up and operate.