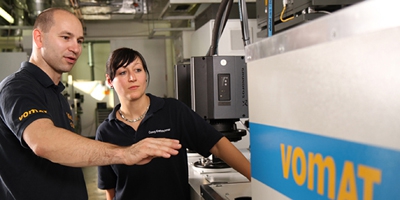
With rising energy costs, new laws and a new environmental conscience, the topic of energy efficiency of production machinery is increasingly being discussed and influences more and more purchasing decisions. The same holds true for filtration systems designed to clean cooling lubricants in the tool manufacturing process. Distributed by oelheld, the filtration specialist VOMAT prides itself to provide systems that filter in an energy efficient way, saving a lot of operating cost, just as its compact design does, by utilizing less expensive production floor space.
The filtration of cooling lubricants is an important part of the overall process in the grinding of carbide and HSS tools. Optimal filtered cooling lubricants protect the grinding wheel, machine components, and help to keep the quality of the finished tool at a high level.
Jens Strebelow, Production Manager at VOMAT: "In many cases, conventional filter systems require a lot of floor space and therefore waste expensive production area. This must not necessarily be the case, since VOMAT offers the FA-series, a compact, powerful and considerably smaller filtration system, which can be are tailored exactly to customer-specific requirements and can easily be integrated into the production process. For example, the company provides VOMAT filter systems with dimensions, as small as 1x1x1,6 meters ( 3.3 x 3.3 x5.3 feet), which is much smaller than comparable systems. Moreover, the compact design simplifies shipping."
But small and compact does not mean being inefficient: Vomat's unique design features guarantee reliable and cost effective operation. Full flow filtration ensures 100 percent separation of dirty and clean oil. The system permanently provides clean oil in NAS 7 Quality (3-5µm) to the grinding machine. Another advantage is the energy efficiency of VOMAT Technology: VOMAT filtration systems filter and backwash only as required. This means that the backwash modus is only activated when the filter elements are contaminated to a degree, where back flushing becomes necessary.
During the backwash cycle there is always enough clean oil available for the production process. The need-based filtering of the oil in conjunction with the need-based filter cleaning offers many advantages: The system adapts automatically to changing production volumes and adjusts itself accordingly. For example, when the grinding machines run at reduced speeds the VOMAT filtration system will only filter the required amount of oil.
If a grinding machine in the connected machine pool is stopped for change over or else, less dirty oil will reach the Vomat system. This does not only save considerable energy but also increases the life of the filter elements and the coolant itself appreciably. At the same time, less heat is transferred to the coolant, which in turn reduces energy costs for cooling the filtration medium. All this combined reduces energy consumption and leads to considerable savings.
Strebelow: "Clean coolant in the carbide and HSS tool grinding is an important factor for achieving high quality of the final product. Saving energy resources is nowadays an important design aspect for Vomat engineers. Vomat filtration systems do not need to run constantly and with maximum output. VOMAT systems reduce due to their compact design and energy-optimized operating mode, the production costs for our customers. This proofs, that the selection of the right filtration system will ultimately influence cost of production."
Contact Details
Related Glossary Terms
- coolant
coolant
Fluid that reduces temperature buildup at the tool/workpiece interface during machining. Normally takes the form of a liquid such as soluble or chemical mixtures (semisynthetic, synthetic) but can be pressurized air or other gas. Because of water’s ability to absorb great quantities of heat, it is widely used as a coolant and vehicle for various cutting compounds, with the water-to-compound ratio varying with the machining task. See cutting fluid; semisynthetic cutting fluid; soluble-oil cutting fluid; synthetic cutting fluid.
- grinding
grinding
Machining operation in which material is removed from the workpiece by a powered abrasive wheel, stone, belt, paste, sheet, compound, slurry, etc. Takes various forms: surface grinding (creates flat and/or squared surfaces); cylindrical grinding (for external cylindrical and tapered shapes, fillets, undercuts, etc.); centerless grinding; chamfering; thread and form grinding; tool and cutter grinding; offhand grinding; lapping and polishing (grinding with extremely fine grits to create ultrasmooth surfaces); honing; and disc grinding.
- grinding machine
grinding machine
Powers a grinding wheel or other abrasive tool for the purpose of removing metal and finishing workpieces to close tolerances. Provides smooth, square, parallel and accurate workpiece surfaces. When ultrasmooth surfaces and finishes on the order of microns are required, lapping and honing machines (precision grinders that run abrasives with extremely fine, uniform grits) are used. In its “finishing” role, the grinder is perhaps the most widely used machine tool. Various styles are available: bench and pedestal grinders for sharpening lathe bits and drills; surface grinders for producing square, parallel, smooth and accurate parts; cylindrical and centerless grinders; center-hole grinders; form grinders; facemill and endmill grinders; gear-cutting grinders; jig grinders; abrasive belt (backstand, swing-frame, belt-roll) grinders; tool and cutter grinders for sharpening and resharpening cutting tools; carbide grinders; hand-held die grinders; and abrasive cutoff saws.
- grinding wheel
grinding wheel
Wheel formed from abrasive material mixed in a suitable matrix. Takes a variety of shapes but falls into two basic categories: one that cuts on its periphery, as in reciprocating grinding, and one that cuts on its side or face, as in tool and cutter grinding.
- high-speed steels ( HSS)
high-speed steels ( HSS)
Available in two major types: tungsten high-speed steels (designated by letter T having tungsten as the principal alloying element) and molybdenum high-speed steels (designated by letter M having molybdenum as the principal alloying element). The type T high-speed steels containing cobalt have higher wear resistance and greater red (hot) hardness, withstanding cutting temperature up to 1,100º F (590º C). The type T steels are used to fabricate metalcutting tools (milling cutters, drills, reamers and taps), woodworking tools, various types of punches and dies, ball and roller bearings. The type M steels are used for cutting tools and various types of dies.