Contact Details
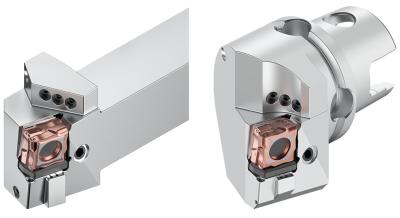
Kennametal has released the FIX8TM heavy-duty turning system, delivering maximum metal removal rates in steel, stainless steel and cast iron. With eight cutting edges per insert, the FIX8 turning system increases productivity of any heavy-duty turning operation, providing the lowest cost per edge while reducing cutting forces up to 15 percent.
FIX8 has eight cutting edges per insert, providing the lowest cost per edge. The tangential design allows it to sustain far higher loads than traditional designs.
“FIX8 is designed to cover a wide range of applications, including turning and facing, smooth surfaces, interrupted, and heavily interrupted cuts. From medium depth-of-cut to roughing in steels, cast iron, and challenging materials like stainless steel, FIX8 handles it all. Even extreme feed rates of up to 1.4mm (0.055") and depths of cut up to 12mm (0.472") are possible with FIX8,” says
The tangential design of the FIX8 insert features a rigid clamping system that pulls the insert securely into the pocket seat, offering superior stability that enables the insert to withstand large cutting forces and vibrations for optimal performance. The insert is also supported by a replaceable carbide shim, protecting the pocket against deformation and damage.
The FIX8 tool holder features precision 3D coolant technology, supplying sufficient coolant precisely where needed. Three coolant nozzles are directed to the rake face, controlling temperature, chip evacuation, and supporting chip formation. Coolant exit holes in two different locations are directed toward the flank of the insert, controlling the heat in the cutting zone and prolonging tool life.
FIX8 tool holder styles featuring precision 3D coolant technology. Delivers coolant sufficiently and precisely to where it is needed.
FIX8 provides excellent chip control for any heavy-duty turning application while increasing tool life. The insert design reduces cutting forces and power consumption, making it ideal for any low horsepower lathe.
Related Glossary Terms
- coolant
coolant
Fluid that reduces temperature buildup at the tool/workpiece interface during machining. Normally takes the form of a liquid such as soluble or chemical mixtures (semisynthetic, synthetic) but can be pressurized air or other gas. Because of water’s ability to absorb great quantities of heat, it is widely used as a coolant and vehicle for various cutting compounds, with the water-to-compound ratio varying with the machining task. See cutting fluid; semisynthetic cutting fluid; soluble-oil cutting fluid; synthetic cutting fluid.
- feed
feed
Rate of change of position of the tool as a whole, relative to the workpiece while cutting.
- lathe
lathe
Turning machine capable of sawing, milling, grinding, gear-cutting, drilling, reaming, boring, threading, facing, chamfering, grooving, knurling, spinning, parting, necking, taper-cutting, and cam- and eccentric-cutting, as well as step- and straight-turning. Comes in a variety of forms, ranging from manual to semiautomatic to fully automatic, with major types being engine lathes, turning and contouring lathes, turret lathes and numerical-control lathes. The engine lathe consists of a headstock and spindle, tailstock, bed, carriage (complete with apron) and cross slides. Features include gear- (speed) and feed-selector levers, toolpost, compound rest, lead screw and reversing lead screw, threading dial and rapid-traverse lever. Special lathe types include through-the-spindle, camshaft and crankshaft, brake drum and rotor, spinning and gun-barrel machines. Toolroom and bench lathes are used for precision work; the former for tool-and-die work and similar tasks, the latter for small workpieces (instruments, watches), normally without a power feed. Models are typically designated according to their “swing,” or the largest-diameter workpiece that can be rotated; bed length, or the distance between centers; and horsepower generated. See turning machine.
- rake
rake
Angle of inclination between the face of the cutting tool and the workpiece. If the face of the tool lies in a plane through the axis of the workpiece, the tool is said to have a neutral, or zero, rake. If the inclination of the tool face makes the cutting edge more acute than when the rake angle is zero, the rake is positive. If the inclination of the tool face makes the cutting edge less acute or more blunt than when the rake angle is zero, the rake is negative.
- turning
turning
Workpiece is held in a chuck, mounted on a face plate or secured between centers and rotated while a cutting tool, normally a single-point tool, is fed into it along its periphery or across its end or face. Takes the form of straight turning (cutting along the periphery of the workpiece); taper turning (creating a taper); step turning (turning different-size diameters on the same work); chamfering (beveling an edge or shoulder); facing (cutting on an end); turning threads (usually external but can be internal); roughing (high-volume metal removal); and finishing (final light cuts). Performed on lathes, turning centers, chucking machines, automatic screw machines and similar machines.