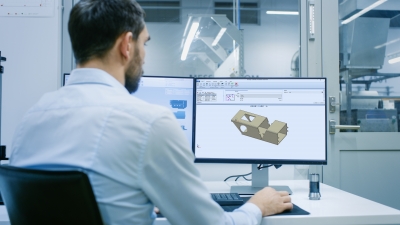
Responding to the complexity and growing demand in the sheet metal sector for increasingly heterogeneous tube designs and different formats, Lantek, a multinational pioneer in the digital transformation occurring in sheet metal manufacturing, presents its latest software developments specific to this area.
The company has designed new applications for Lantek Flex3D which provide easy solutions when designing and machining complete or partial bevels anywhere in the tube. Further, the latest generation software makes it possible to include perforations of various types (round, rectangular, triangular, etc.), and resolve the multiple possibilities that require a comprehensive library of connections and intersections to later assemble complete sets.
"One of the most highly technologically-developed fields in the metal and sheet metal sector is the manufacturing of tubes, both in terms of the development of machine operations and software solutions that address the variety of issues raised by customers,” explains Francisco Pérez, Lantek OEM Channel Director. "For over 35 years, Lantek has been analysing and providing solutions in response to the complexity surrounding the manufacturing of tubes and profiles in the sheet metal sector, taking into account the diversity of cases in sheet metal and tube cutting and the difficulty that lies in controlling the machine and its processes.”
New markets and formats, different types of profiles
The ability to address and resolve the variety of possible cases, especially considering the series of fundamental variables in this field, is key when it comes to responding to the growing demand in this market. For example, each type of profile can be cut in different ways. It depends on the structure of the machine (dimensions of the head/nozzle, axis, etc.) and the customer’s preferences. In the past, tube-cutting machines revolved mainly around cutting circular and rectangular tubes. These machines were extremely expensive, and still are today. However, with the introduction of fibre laser, manufacturing costs, as well as those of the machines themselves, decreased, allowing more companies to purchase them for their plants. The machines have evolved to meet the needs of this new client/market which has, in turn, triggered the emergence of new needs for cutting more complex profiles.
The typical solution provided by the machine manufacturer was based on predefined machining for each type of profile/format, but when a new type appears adding it to the standard library is very time consuming, especially considering that the number of possible formats has multiplied exponentially. The result is that the client must accept whatever predefined machining method the machine supplier offers, which may not be ideal.
Aware of this situation and the need to offer solutions for a wide range of machines, Lantek has developed a new machining concept with its tube-cutting product Lantek Flex3D. This new solution is a tool able to define a tailor-made cutting trajectory for any profile. This includes a customised cutting sequence defined by both the OEM and the machine user to meet their production requirements. The result is the creation of a "knowledge database" where the OEM's machine experience is combined with the end user's cutting experience.
This new development has allowed Lantek to get ahead of the market, anticipating the future and adapting to manufacturer’ needs. This new Lantek Flex3d tool is available in version V41 of the Global Release 2021.
Resolving a variety of issues
In situations with highly variable manufacturing requirements, Lantek Flex3D considers the type of tube to be manufactured and the type of cutting machine used. For example, large tubes for structural applications, with sizeable thickness and dimensions, are usually cut with plasma and oxycut machines, whereas narrower tubes with reduced dimensions are generally cut with laser cutting technology. The software fundamentals are the same for the tubes themselves, but there is a significant difference in the control of the machine itself and its processes.
The types of machines are multiplying and the complexity of driving them is not so much because of the cutting technology itself (plasma, laser) but because of the head: the issues to be resolved multiply due to machines with various types of fixed heads, and machines with different types of moving heads. Equally, there are specific tube-cutting machines, but there are also combined machines for 2D cutting, which meet specific needs for subcontractors that don't specialize in tubes.
Lantek Flex3D has been designed to resolve these complexities and is fully integrated with the rest of Lantek’s planning (MES), management (ERP), analytics and monitoring solutions. With Lantek Flex3D, Lantek offers a specific software program for manufacturing tubes and profiles that has a whole family of applications covering almost all scenarios encountered by manufacturers. From the simple to the complex, it manages any type of machine or cutting technology, integrates with the most popular design programs, and provides a solution for all types of tubes or assemblies with the aim of providing software to meet the specific needs of each customer.