Contact Details
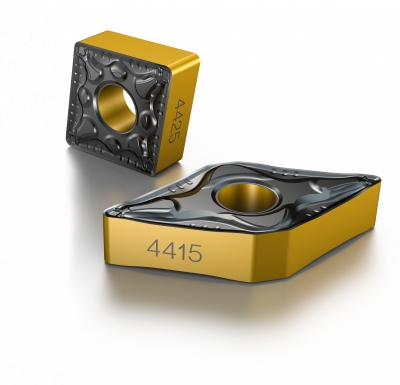
Enhance steel turning productivity with new carbide grades
Sandvik Coromant’s GC4415 and GC4425 steel turning grades are ideal for manufacturers operating in mass and batch production set-ups. GC4425 is a machinist’s first choice for steel turning, outperforming competition in a majority of steel turning applications. The new grade provides improved wear resistance, heat resistance and toughness, considerably expanding the application range. Grade GC4415 complements GC4425 when more heat resistance is needed.
To increase their use for steel turning applications across the automotive, energy and general engineering sectors, the upgrade includes more insert shapes for each grade. Having access to the correct insert shape is vital for effective finishing and roughing operations, and the insert shape should be selected relative to the entering angle accessibility required of the tool.
“In October 2020, Sandvik Coromant made a total of 547 items available as part of the grades’ release,” explained Rolf Olofsson, Product Manager at Sandvik Coromant. “However, to meet the demands of Sandvik Coromant’s wide-ranging customer base, we always aim to build on our product innovations and continuously improve. As a result, an additional 381 items have been added to the range.
“The GC4415 and GC4425 inserts show superior wear resistance over competing inserts, which contributes towards extended tool life and predictable performance with every use. This also minimizes material waste, both from the workpiece and the insert. With these benefits in mind, offering extra insert shapes that are compatible with more tool holders means that more customers will be able the take advantage of GC4415 and GC4425 for their steel turning operations.”
While still relatively new to the market, GC4415 and GC4425 have demonstrated measurable productivity benefits since their first release. One general engineering customer, using the GC4415 insert to carry out roughing on a P2.5.Z.HT steel workpiece to machine a pulling rail, saw a 80% productivity increase and a 100% increase in tool life when compared to a competing grade.
Elsewhere, when roughing an axis for a power generation customer, the GC4425 demonstrated a 90% increase in tool life, providing secure machining with stable and predictable flank wear and no notch wear.
“Despite launching at the end of 2020, GC4415 and GC4425 have already delivered huge productivity and cost-saving benefits for our customers,” said Olofsson. “Every manufacturer wants to achieve increased metal removal rates, more pieces per edge, reduced cycle times, minimised waste and optimized inventory use. For the GC4415 and GC4425, the proof is in the numbers.
“Now, with the latest upgrades to the insert range, Sandvik Coromant will be able to help even more customers enjoy the benefits of optimized, efficient steel turning.”
Related Glossary Terms
- flank wear
flank wear
Reduction in clearance on the tool’s flank caused by contact with the workpiece. Ultimately causes tool failure.
- sawing machine ( saw)
sawing machine ( saw)
Machine designed to use a serrated-tooth blade to cut metal or other material. Comes in a wide variety of styles but takes one of four basic forms: hacksaw (a simple, rugged machine that uses a reciprocating motion to part metal or other material); cold or circular saw (powers a circular blade that cuts structural materials); bandsaw (runs an endless band; the two basic types are cutoff and contour band machines, which cut intricate contours and shapes); and abrasive cutoff saw (similar in appearance to the cold saw, but uses an abrasive disc that rotates at high speeds rather than a blade with serrated teeth).
- turning
turning
Workpiece is held in a chuck, mounted on a face plate or secured between centers and rotated while a cutting tool, normally a single-point tool, is fed into it along its periphery or across its end or face. Takes the form of straight turning (cutting along the periphery of the workpiece); taper turning (creating a taper); step turning (turning different-size diameters on the same work); chamfering (beveling an edge or shoulder); facing (cutting on an end); turning threads (usually external but can be internal); roughing (high-volume metal removal); and finishing (final light cuts). Performed on lathes, turning centers, chucking machines, automatic screw machines and similar machines.
- wear resistance
wear resistance
Ability of the tool to withstand stresses that cause it to wear during cutting; an attribute linked to alloy composition, base material, thermal conditions, type of tooling and operation and other variables.