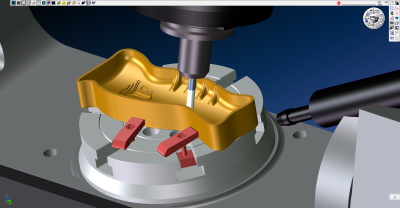
3D Systems announced the release of GibbsCAM 2016 software for production machining. Building on the Universal Kinematic Machine (UKM) technology of the previous edition, GibbsCAM 2016 delivers a variety of improvements to increase efficiency, accelerate programming speed, and enhance visualization and accuracy for CNC machine programming. The GibbsCAM platform provides a complement to additive manufacturing processes, further empowering 3D Systems’ users to transform digital concepts into physical realities.
GibbsCAM 2016 delivers a variety of improvements to increase efficiency, accelerate programming speed, and enhance visualization and accuracy for CNC machine programming.
The enhanced kinematic framework of GibbsCAM 2016 makes it a versatile CAM platform that is effective in nearly every manufacturing environment, according to the company. Enabling solutions for complex programming challenges, such as oriented turning scenarios, GibbsCAM is compatible with a wide range of programming and machining operations, including solid modeling, high speed machining, 2- to 5-axis milling, wire EDM, multitask machining and more. Recognized for its ease of use, GibbsCAM is designed to help users eliminate scrap and reduce cycle times.
New features and functions of GibbsCAM 2016 include:
Enhanced thread milling, including support for multi-point tools, tapered threads for both single- and multi-point tools, and improved simulation.
The latest VoluMill technology, providing new toolpath strategies to optimize high speed roughing of large pockets and slots, open face milling strategies that can decrease cutting time by up to 60 percent, and Technology Expert integration for ready access to optimal speeds and feeds.
New oriented turning capabilities, giving users added control in how tools interact with parts. From using a single tool at multiple B orientations to reorienting tool groups for use on a different spindle to full support of Flash Tooling for multiple-orientation turning tools, GibbsCAM 2016 delivers increased flexibility and control to CNC programmers.
Added toolpath strategies for 5-axis milling, enabling users to define toolpath direction using the natural flow of a surface with the new Flowline option. Toolpaths can also now be extended in width as well as length. Additional enhancements include improved 5-axis drilling, multi-stepped pocket roughing and new gouge checking strategies.
“The GibbsCAM platform is a key component in today’s advanced manufacturing workflows, allowing our customers to optimize their machine processes and unlock greater productivity,” said Calvin Hur, Vice President, Co-Chief Operating Officer and Chief Revenue Officer, Software Products, 3D Systems. “By working closely with users over the past year, we’ve enhanced our understanding of the evolving needs of the factory floor, and are pleased to offer these improvements to help our customers maximize efficiency, safety and profitability.”
Contact Details
Related Glossary Terms
- computer numerical control ( CNC)
computer numerical control ( CNC)
Microprocessor-based controller dedicated to a machine tool that permits the creation or modification of parts. Programmed numerical control activates the machine’s servos and spindle drives and controls the various machining operations. See DNC, direct numerical control; NC, numerical control.
- computer-aided manufacturing ( CAM)
computer-aided manufacturing ( CAM)
Use of computers to control machining and manufacturing processes.
- electrical-discharge machining ( EDM)
electrical-discharge machining ( EDM)
Process that vaporizes conductive materials by controlled application of pulsed electrical current that flows between a workpiece and electrode (tool) in a dielectric fluid. Permits machining shapes to tight accuracies without the internal stresses conventional machining often generates. Useful in diemaking.
- flash
flash
Thin web or film of metal on a casting that occurs at die partings and around air vents and movable cores. This excess metal is due to necessary working and operating clearances in a die. Flash also is the excess material squeezed out of the cavity as a compression mold closes or as pressure is applied to the cavity.
- gang cutting ( milling)
gang cutting ( milling)
Machining with several cutters mounted on a single arbor, generally for simultaneous cutting.
- milling
milling
Machining operation in which metal or other material is removed by applying power to a rotating cutter. In vertical milling, the cutting tool is mounted vertically on the spindle. In horizontal milling, the cutting tool is mounted horizontally, either directly on the spindle or on an arbor. Horizontal milling is further broken down into conventional milling, where the cutter rotates opposite the direction of feed, or “up” into the workpiece; and climb milling, where the cutter rotates in the direction of feed, or “down” into the workpiece. Milling operations include plane or surface milling, endmilling, facemilling, angle milling, form milling and profiling.
- toolpath( cutter path)
toolpath( cutter path)
2-D or 3-D path generated by program code or a CAM system and followed by tool when machining a part.
- turning
turning
Workpiece is held in a chuck, mounted on a face plate or secured between centers and rotated while a cutting tool, normally a single-point tool, is fed into it along its periphery or across its end or face. Takes the form of straight turning (cutting along the periphery of the workpiece); taper turning (creating a taper); step turning (turning different-size diameters on the same work); chamfering (beveling an edge or shoulder); facing (cutting on an end); turning threads (usually external but can be internal); roughing (high-volume metal removal); and finishing (final light cuts). Performed on lathes, turning centers, chucking machines, automatic screw machines and similar machines.
- wire EDM
wire EDM
Process similar to ram electrical-discharge machining except a small-diameter copper or brass wire is used as a traveling electrode. Usually used in conjunction with a CNC and only works when a part is to be cut completely through. A common analogy is wire electrical-discharge machining is like an ultraprecise, electrical, contour-sawing operation.