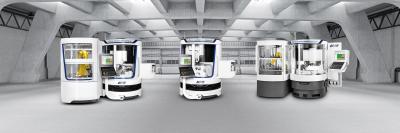
Based on a highly efficient and productive two-in-one concept, Walter Helitronic Vision Diamond 400 L, Helitronic Power Diamond 400 and Helitronic Diamond Evolution tool grinding machines, from United Grinding North America Inc., integrate both eroding and/or grinding capabilities into single grinding machine platforms. From a production standpoint, the two-in-one concept lets users completely erode tools (PCD) and completely grind tools (carbide) using the same machine to eliminate the time-consuming task of moving workpieces to a second machine.
The Walter two-in-one concept is especially beneficial in the production of modern PCD tools in which the tool’s carbide blank already has soldered PCD. The ability to erode, grind or even do both operations in one clamping gives users an unparalleled level of flexibility and reliability for their tool production applications. The machines process any PCD tool, whether for the wood, automotive or aerospace industry sectors, in addition to special/custom applications.
With the ability to perform both eroding and grinding or combinations of the two processing methods on one machine, tool makers can also expand into the PCD tool-producing field to increase new business and growth without incurring additional risk or threatening cost effectiveness.
All Walter two-in-one machines feature the company’s Fine Pulse Technology, which has set new standards in terms of achievable surface quality, cutting-edge toughness and process reliability for PCD tool production. A tool made with Fine Pulse Technology shines on its free surface, similar to a polished/ground tool. Even coarse-grained PCD types, which previously could not be fine finished, are effortlessly eroded with Fine Pulse Technology.
In some cases, entire steps in the production chain have been omitted because the eroded tools no longer require resharpening or polishing. And in addition to PCD tool productivity, the machines work with Walter Helitronic Tool Studio, a software solution that makes tool shaping even easier and clearer, especially for PCD tools.
Contact Details
Related Glossary Terms
- grinding
grinding
Machining operation in which material is removed from the workpiece by a powered abrasive wheel, stone, belt, paste, sheet, compound, slurry, etc. Takes various forms: surface grinding (creates flat and/or squared surfaces); cylindrical grinding (for external cylindrical and tapered shapes, fillets, undercuts, etc.); centerless grinding; chamfering; thread and form grinding; tool and cutter grinding; offhand grinding; lapping and polishing (grinding with extremely fine grits to create ultrasmooth surfaces); honing; and disc grinding.
- grinding machine
grinding machine
Powers a grinding wheel or other abrasive tool for the purpose of removing metal and finishing workpieces to close tolerances. Provides smooth, square, parallel and accurate workpiece surfaces. When ultrasmooth surfaces and finishes on the order of microns are required, lapping and honing machines (precision grinders that run abrasives with extremely fine, uniform grits) are used. In its “finishing” role, the grinder is perhaps the most widely used machine tool. Various styles are available: bench and pedestal grinders for sharpening lathe bits and drills; surface grinders for producing square, parallel, smooth and accurate parts; cylindrical and centerless grinders; center-hole grinders; form grinders; facemill and endmill grinders; gear-cutting grinders; jig grinders; abrasive belt (backstand, swing-frame, belt-roll) grinders; tool and cutter grinders for sharpening and resharpening cutting tools; carbide grinders; hand-held die grinders; and abrasive cutoff saws.
- polishing
polishing
Abrasive process that improves surface finish and blends contours. Abrasive particles attached to a flexible backing abrade the workpiece.
- polycrystalline diamond ( PCD)
polycrystalline diamond ( PCD)
Cutting tool material consisting of natural or synthetic diamond crystals bonded together under high pressure at elevated temperatures. PCD is available as a tip brazed to a carbide insert carrier. Used for machining nonferrous alloys and nonmetallic materials at high cutting speeds.
- shaping
shaping
Using a shaper primarily to produce flat surfaces in horizontal, vertical or angular planes. It can also include the machining of curved surfaces, helixes, serrations and special work involving odd and irregular shapes. Often used for prototype or short-run manufacturing to eliminate the need for expensive special tooling or processes.