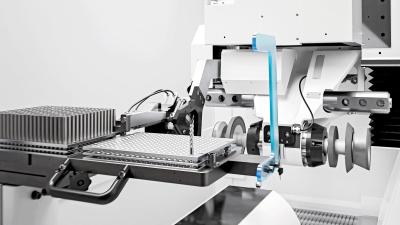
WALTER will introduce the latest addition to their comprehensive machine lineup at the GrindingHub 2022 exhibition: the compact HELITRONIC G 200 tool gringing machine. GrindingHub 2022 runs from May 17 – 20, 2022 in Stuttgart, Germany, and WALTER will be exhibitng in hall 9, booth A50. The latest HELITRONIC will also make its North American debut at IMTS 2022.
In a floor space of less than 2.3 sqaure meters (24.8 square feet), the cost-efficient HELITRONIC G 200 offers tool grinding at its best. Grinding and re-sharpening of rotationally symmetrical cutting tools ranging from 1 to 125mm (0.039” to 4.92”) in diameter with a grinding wheel up to 150mm (5.91”) is possible. The HELITRONIC G 200 can accommodate a maximum tool length of 235mm (9.25”) and a tool weight of up to 12 kg (26.45 lbs).
Designed for ease-of-use and reliability
The ergonomic design integrates a swivelling multifunction touch panel with a 21.5” monitor, facilitating easy operation and accessibility to the working area. A low-vibration solid mineral cast bed and C-frame construction offers high damping capabilities and thermal stability resulting in maximum grinding precision. The linear axes X, Y, Z are built according to the high WALTER quality standard. The rotating A and C axes are equipped with torque motors and provide an unprecedented lifetime with minimum service effort.
The HELITRONIC G 200 uses the gloablly proven HELITRONIC TOOL STUDIO grinding software from WALTER, which provides ease of programming with the greatest possible flexibility.
Automation ready
For maximum productivity, a loading system is available: the “Top Loader” is directly integrated into the work envelope of the machine for easy access and therefore requires no additional floor space. Suitable for tools from 3 mm to 16 mm (0.118” to 0.63”) in diameter, the maximum tool capacity of the loading system up 500 tools for tools with a 3 mm (0.118”) diameter. The Top Loader uses WALTER-standard robot pallets and automated electrical teaching.
Contact Details
Related Glossary Terms
- grinding
grinding
Machining operation in which material is removed from the workpiece by a powered abrasive wheel, stone, belt, paste, sheet, compound, slurry, etc. Takes various forms: surface grinding (creates flat and/or squared surfaces); cylindrical grinding (for external cylindrical and tapered shapes, fillets, undercuts, etc.); centerless grinding; chamfering; thread and form grinding; tool and cutter grinding; offhand grinding; lapping and polishing (grinding with extremely fine grits to create ultrasmooth surfaces); honing; and disc grinding.
- grinding wheel
grinding wheel
Wheel formed from abrasive material mixed in a suitable matrix. Takes a variety of shapes but falls into two basic categories: one that cuts on its periphery, as in reciprocating grinding, and one that cuts on its side or face, as in tool and cutter grinding.
- work envelope
work envelope
Cube, sphere, cylinder or other physical space within which the cutting tool is capable of reaching.