Contact Details
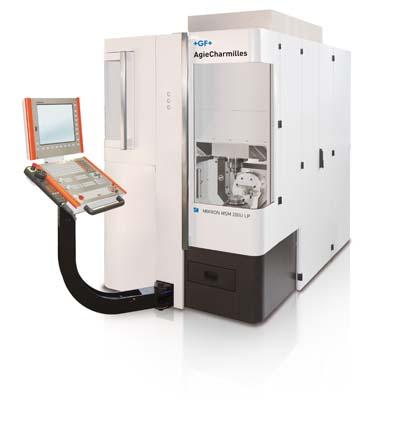
The new high-tech, high-speed MIKRON HSM 200U LP milling machine is available from GF AgieCharmilles. Offered in 3- and 5-axis versions, the MIKRON HSM 200U LP (linear performance) brings speed, efficiency and precision to the machining of small, highly complex components, such as medical implants, electrodes and watch components. With a compact footprint, the machine easily fits into most facilities, which is key for dental labs, watchmaking shops and other locations where floor space is often extremely limited.
According to Gisbert Ledvon, director of business development for GF AgieCharmilles in North America, the MIKRON HSM 200U LP accommodates the medical industry's increased need for lean manufacturing via small-footprint, high-speed machines that bring amazing accuracy and supreme surface finishes to small parts production.
The MIKRON HSM 200U LP can produce workpieces via true 5-axis simultaneous high-speed machining. Linear motor technology in the main machine axes and optimized direct-drive motors for the B and C axes result in high precision and superior part surface finishes as fine as Ra 0.05µm. Furthermore, the machine's powerful 50,000- rpm, 11.4-hp Step-Tec spindle also assists in providing excellent surface finish and part detail.
To counteract the high levels of heat that can develop over prolonged periods of high axis feedrates, the MIKRON HSM 200U LP employs a sophisticated thermal management system. Each of the linear axes features a cooling unit to systematically draw the heat out of the machine, creating geometric stability and high repeatability of movement guidance.
A Heidenhain iTNC 530 control system and smart machining modules on the MIKRON HSM 200U LP provide advanced levels of monitoring critical to the production of highvalue precision medical parts. The system allows the machine to automatically check and evaluate tools and workpieces, inspect tools for breakage and perform measurements of the workpiece. Additionally, the smart machine modules automatically monitor spindle vibration, calibrate machine geometry and transmit process status messages to an operator's cell phone.
To avoid inconsistent loading of small tools and 3D geometry errors due to the inaccurate measurement of those tools, the MIKRON HSM 200U LP features Intelligent Tool Measurement (ITM). ITM records the complete tool tip up to a diameter of 0.47" on image sensors. Special software cleans and measures the recorded tool geometry for repeatability in the micrometer range. The MIKRON HSM 200U LP's robust polymer concrete machine base provides increase performance in the areas of vibration dampening and thermal stability, extending tool life and reducing operating cost. Also, attention to the ergonomics of the machine's design allows for uncharacteristically easy access to workpieces.
Lastly, the MIKRON HSM 200U LP possesses the capability for 24/7 unattended machining using its optional MIKRON pallet magazines with System 3R and Erowa interfaces. These fully integrated pallet magazines can be loaded without interrupting cutting operations already in progress. The automation of tool or workpiece handling is possible from three sides of the machine.
Related Glossary Terms
- gang cutting ( milling)
gang cutting ( milling)
Machining with several cutters mounted on a single arbor, generally for simultaneous cutting.
- lean manufacturing
lean manufacturing
Companywide culture of continuous improvement, waste reduction and minimal inventory as practiced by individuals in every aspect of the business.
- linear motor
linear motor
Functionally the same as a rotary motor in a machine tool, a linear motor can be thought of as a standard permanent-magnet, rotary-style motor slit axially to the center and then peeled back and laid flat. The major advantage of using a linear motor to drive the axis motion is that it eliminates the inefficiency and mechanical variance caused by the ballscrew assembly system used in most CNC machines.
- micrometer
micrometer
A precision instrument with a spindle moved by a finely threaded screw that is used for measuring thickness and short lengths.
- milling
milling
Machining operation in which metal or other material is removed by applying power to a rotating cutter. In vertical milling, the cutting tool is mounted vertically on the spindle. In horizontal milling, the cutting tool is mounted horizontally, either directly on the spindle or on an arbor. Horizontal milling is further broken down into conventional milling, where the cutter rotates opposite the direction of feed, or “up” into the workpiece; and climb milling, where the cutter rotates in the direction of feed, or “down” into the workpiece. Milling operations include plane or surface milling, endmilling, facemilling, angle milling, form milling and profiling.
- milling machine ( mill)
milling machine ( mill)
Runs endmills and arbor-mounted milling cutters. Features include a head with a spindle that drives the cutters; a column, knee and table that provide motion in the three Cartesian axes; and a base that supports the components and houses the cutting-fluid pump and reservoir. The work is mounted on the table and fed into the rotating cutter or endmill to accomplish the milling steps; vertical milling machines also feed endmills into the work by means of a spindle-mounted quill. Models range from small manual machines to big bed-type and duplex mills. All take one of three basic forms: vertical, horizontal or convertible horizontal/vertical. Vertical machines may be knee-type (the table is mounted on a knee that can be elevated) or bed-type (the table is securely supported and only moves horizontally). In general, horizontal machines are bigger and more powerful, while vertical machines are lighter but more versatile and easier to set up and operate.
Additional Products from GF Machining Solutions
Pagination
- First page
- Previous page
- 1
- 2
- 3
- 4
- 5
- 6